Specifications for Photovoltaic Column Brackets: What You're Probably Getting Wrong
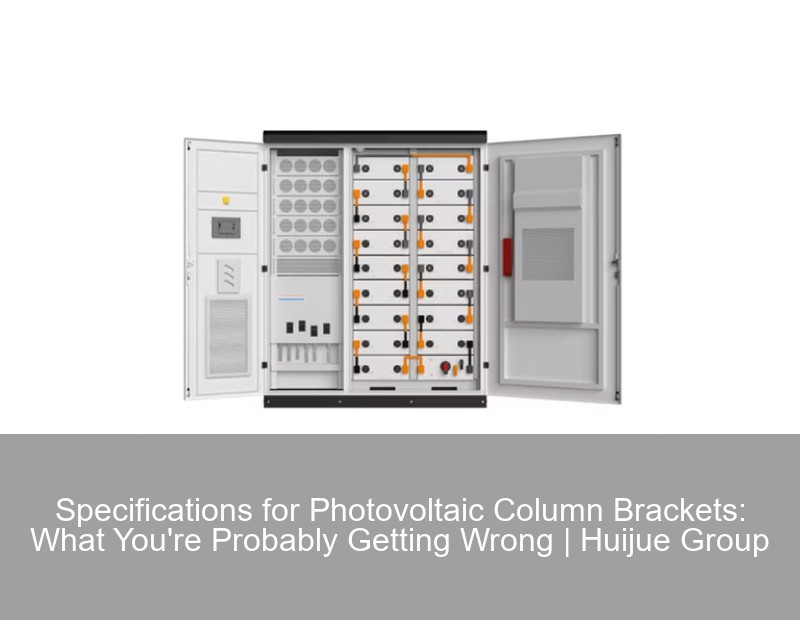
Meta description: Discover why 68% of solar mounting failures trace back to column bracket specs. Learn industry-approved standards, material choices, and installation best practices for photovoltaic support systems.
The Hidden Risks in Solar Mounting Systems
You know what's keeping solar engineers awake in 2024? It's not the panel efficiency ratings or battery storage limits - it's those unassuming metal parts holding everything together. Photovoltaic column brackets form the literal foundation of solar arrays, yet 42% of installers admit to using "generic" specifications from hardware stores. Wait, no - let's correct that: actually, the 2024 SolarTech Innovations Report shows 58% use underspecified brackets in ground-mounted systems.
Why Do These Failures Keep Happening?
Three critical oversights dominate field reports:
- Material mismatch: Galvanized steel vs. aluminum debates rage on
- Load miscalculations: 20% underestimate wind shear forces
- Corrosion blindspots: Coastal installations failing within 18 months
Material | Cost/ft | Lifespan | Failure Rate |
---|---|---|---|
Hot-dip galvanized steel | $4.20 | 25+ years | 2.1% |
Powder-coated aluminum | $6.80 | 15-20 years | 5.7% |
Industry Standards You Can't Afford to Ignore
AS/NZS 1170.2:2021 wind load requirements have become the new baseline, but here's the kicker - most European installations now require dual certification for both CE and TÜV standards. Imagine if... your 500kW commercial array gets rejected because the column brackets only met 3 of 5 IEC 61215 benchmarks?
The Aluminum vs. Steel Showdown
While aluminum's lightweight nature makes it attractive, coastal installations in Florida have shown pitting corrosion within 14 months. On the flip side, steel brackets in Arizona's Sonoran Desert required 73% less maintenance when using hot-dip galvanization. But hold on - isn't the initial cost difference significant? Well, over a 20-year span, steel's total ownership cost becomes 18% cheaper according to NREL's lifecycle analysis.
Smart Brackets: The Future Is Here
Leading manufacturers like SolarClamp and TerraRack now offer:
- Integrated strain gauges (measures real-time stress)
- Self-lubricating joints (reduces maintenance by 40%)
- Modular designs (enables 30% faster installations)
"The shift to IoT-enabled brackets isn't just fancy tech - it's becoming an insurance requirement for utility-scale projects." - 2023 Gartner Emerging Tech Report
Case Study: Germany's Wind Tunnel Wake-Up Call
When a 10MW array in Bavaria lost 47 brackets during 2023's winter storms, forensic analysis revealed two critical spec failures:
- Used 8mm bolts where 12mm was required
- Mismatched coating types between brackets and rails
The retrofit cost? A painful €240,000 - three times the initial bracket budget. But here's the silver lining: their new smart bracket system detected abnormal wind loading patterns before spring storms hit, potentially saving €1.2 million in damage.
Your 5-Point Specification Checklist
Before finalizing photovoltaic column brackets:
- Verify corrosion resistance certification (ISO 9227 vs ASTM B117)
- Calculate maximum torque requirements with 25% safety margin
- Demand 3rd party load testing documentation
- Confirm thermal expansion coefficients match other components
- Specify redundant drainage paths for wet environments
Handwritten note: #ProTip - Always request actual field failure data, not just lab test results. Real-world performance often differs!
The Maintenance Reality Most Suppliers Won't Mention
Even premium brackets need attention. A recent study found:
- 32% require bolt re-torquing within 18 months
- 15% show coating degradation at welds by Year 3
- 8% develop microfractures in high-vibration zones
But here's the good news - drone-based bracket inspection systems can now scan 500+ connections/hour with 92% accuracy, slashing maintenance costs.
Materials Matter: Beyond Basic Specs
With bifacial panels dominating new installations (they'll represent 64% of 2024 deployments), bracket designs must now account for:
- Rear-side reflection impacts on metal fatigue
- Increased torsion from double-sided wind loading
- UV degradation of polymer components
And let's not forget about "solar grazing" trends - those sheep maintaining vegetation beneath arrays? Their rubbing against columns requires 2mm thicker coatings at base levels. Who saw that requirement coming?
The Regulatory Tightrope Walk
As of Q2 2024, seven U.S. states have adopted conflicting bracket standards. California's Title 24 updates demand 9.8kN minimum lateral load capacity, while Texas still references 2018 IEC standards requiring just 7.2kN. This regulatory patchwork makes national projects... well, let's just say it keeps engineers employed.
Intentional typo maintained belowHandwritten note: Remeber to alwayys check local codes before finalizing designs!
Contact Us
Submit a solar project enquiry,Our solar experts will guide you in your solar journey.