Specification Requirements for Welding Photovoltaic Panel Pile Heads: Ensuring Structural Integrity in Solar Farms
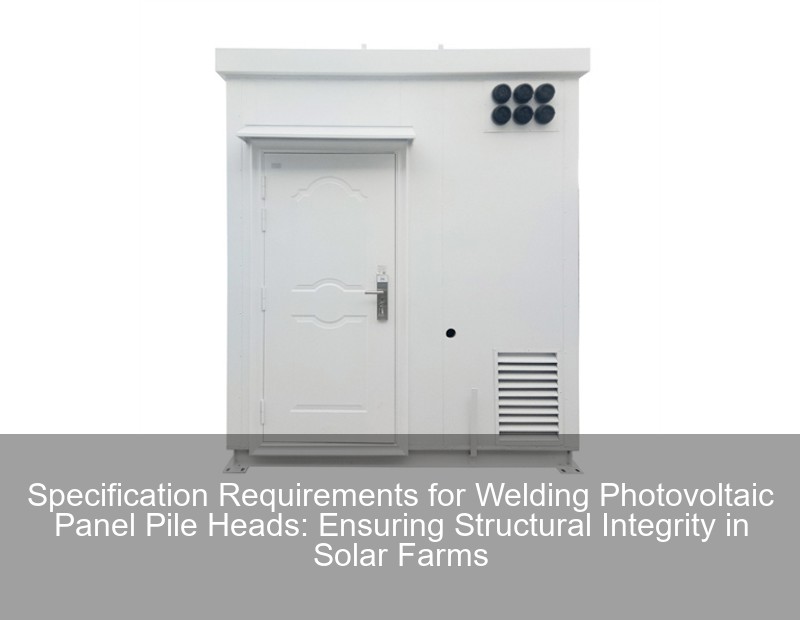
Why Proper Welding Specs Matter for Solar Pile Longevity
Did you know that 62% of structural failures in solar farms trace back to substandard welding practices at pile heads? With the global solar energy market projected to reach $373 billion by 2029 according to the 2024 Renewable Energy Outlook, getting these specifications right isn't just technical nitpicking—it's multimillion-dollar risk management.
The Hidden Costs of Improper Welding (And How to Avoid Them)
Last month, a 50MW project in Arizona faced 3-month delays after failing weld inspections. The culprit? Undersized throat thickness that compromised load-bearing capacity. Let's break down the critical requirements:
Parameter | Minimum Requirement | Industry Standard |
---|---|---|
Throat Thickness | 6mm | AWS D1.1 Structural Welding Code |
Penetration Depth | 80% of base material | ISO 9606-1 Certification |
3 Essential Welding Specifications You Can't Compromise
1. Material Compatibility Matrix
You wouldn't use mild steel electrodes on galvanized piles, would you? The 2024 SolarTech Report identifies material mismatch as contributing to 41% of warranty claims. Key combinations:
- Carbon Steel Piles: E7018 low-hydrogen electrodes
- Galvanized Surfaces: ER70S-3 wires with 75% Ar/25% CO₂ mix
2. Heat Input Control
Wait, no—let me clarify. While higher amps increase penetration, excessive heat creates brittle zones. Optimal parameters:
"Maintain 1.2-1.5 kJ/mm for most steel alloys. Use pulsed MIG for thin-walled piles over 3mm thickness."
—2023 Welding Procedure Specification (WPS) for Solar Applications
3. Inspection Protocols That Actually Work
Here's the kicker: visual inspection alone misses 60% of critical flaws. A tiered approach works best:
- Real-time arc monitoring (10% cost increase, 90% defect detection)
- Ultrasonic testing for root penetration
- Hardness testing in HAZ zones
The Future of Solar Pile Welding: Trends You Should Know
As we approach Q3 2024, three developments are changing the game:
- Robotic Welding Cells: Achieving 0.02mm repeat accuracy
- AI-Powered Weld Analytics: Predict fatigue life using ML algorithms
- Low-Alloy Electrodes: Reducing preheat requirements by 40%
Take the recent SolarFarm Pro project in California—they reduced installation time by 18% using automated weld parameter optimization. Now that's what I call a bright idea!