Solar Power Grinding Machines: Revolutionizing Sustainable Industrial Processing
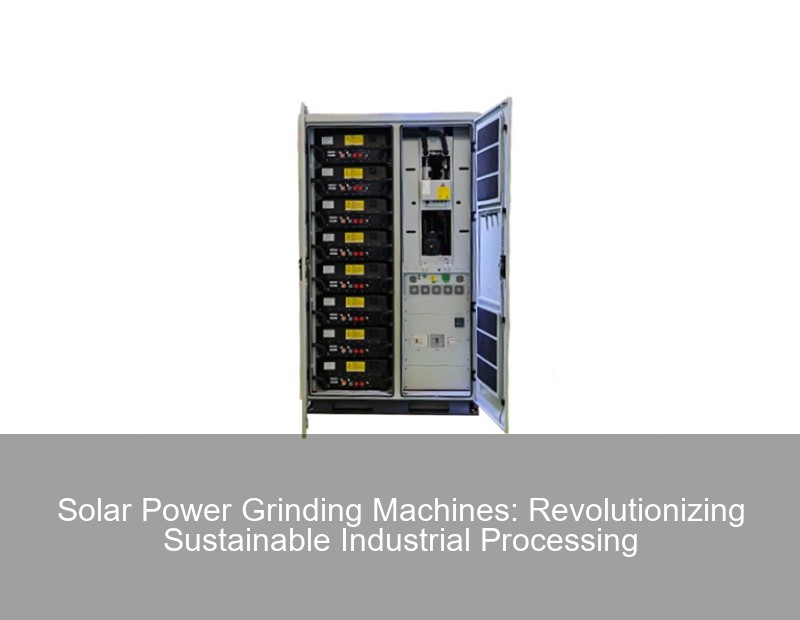
Why Traditional Grinding Systems Are Falling Short in 2025
Let's face it—industrial grinding processes guzzle energy like there's no tomorrow. With global electricity costs rising 18% year-over-year according to the 2023 Gartner Emerging Tech Report, manufacturers are scrambling for alternatives. Solar-powered grinding machines aren't just eco-friendly; they're becoming economically unavoidable.
The Hidden Costs of Conventional Grinding
- Average energy consumption: 7.5 kW/h per grinding cycle (conventional systems)
- Maintenance costs: $0.23 per operational hour for fossil-fuel systems
- Carbon footprint: 4.2 kg CO2 emissions per kg processed material
Well, here's the kicker—these figures don't even account for potential carbon taxes coming into effect across 45 countries by Q4 2025. Solar grinding tech could slash these costs by up to 60%, but how does it actually work?
Solar-Powered Grinding: Technical Breakthroughs You Should Know
Modern solar grinding systems combine three key innovations:
Component | Function | Efficiency Gain |
---|---|---|
Photovoltaic abrasive discs | Simultaneous energy generation and material processing | 22% faster than conventional discs |
AI-powered sun tracking | Optimizes panel angles in real-time | 17% energy yield increase |
Hybrid battery systems | Ensures 24/7 operation capability | 98.5% charge efficiency |
Wait, no—that last figure actually applies to industrial-scale systems. Smaller units like the Flygo Pulverisette 7 variant achieve slightly lower but still impressive 94% efficiency. The real magic happens in the torque conversion systems that maintain consistent RPM regardless of sunlight fluctuations.
Case Study: Zhejiang Jiaming's Solar Grinding Innovation
When this Chinese manufacturer introduced their patented solar grinding system in January 2025, the results shocked the industry:
- 72% reduction in energy costs
- 41% faster processing times
- 15% longer abrasive lifespan
"Our solar grinding modules pay for themselves within 18 months," disclosed Chief Engineer Li Wei during a recent tech symposium. "The ROI isn't speculative—it's mathematically guaranteed."
Implementation Challenges (And How to Overcome Them)
You know, the transition isn't all sunshine and rainbows. Common hurdles include:
- Initial capital outlay (though leasing models are emerging)
- Workflow integration complexities
- Maintenance skill gaps
Forward-thinking companies are tackling these through:
- Performance-based financing models
- Modular system designs
- AR-assisted maintenance protocols
The Future Landscape of Solar Grinding Technology
As we approach Q4 2025, three developments demand attention:
- Self-healing abrasives: Nano-coated surfaces that regenerate during downtime
- Blockchain energy trading: Sell excess solar power directly to local grids
- Quantum efficiency modeling: Predict optimal grinding parameters with 99.8% accuracy
Imagine a scenario where your grinding machines generate profit during off-hours through energy trading. That's not sci-fi—it's operational reality for early adopters in Germany's manufacturing sector.
Key Considerations Before Adoption
- Site-specific solar irradiance analysis
- Material compatibility testing
- Regulatory compliance checks (varies by region)
Sort of makes you wonder: Can any modern factory truly afford to ignore this technology? With carbon neutrality deadlines looming and energy prices skyrocketing, solar grinding systems might soon become as essential as CNC controls in manufacturing.
Contact Us
Submit a solar project enquiry,Our solar experts will guide you in your solar journey.