Solar Photovoltaic Support C-Shaped Steel Specification Manual: A Comprehensive Guide
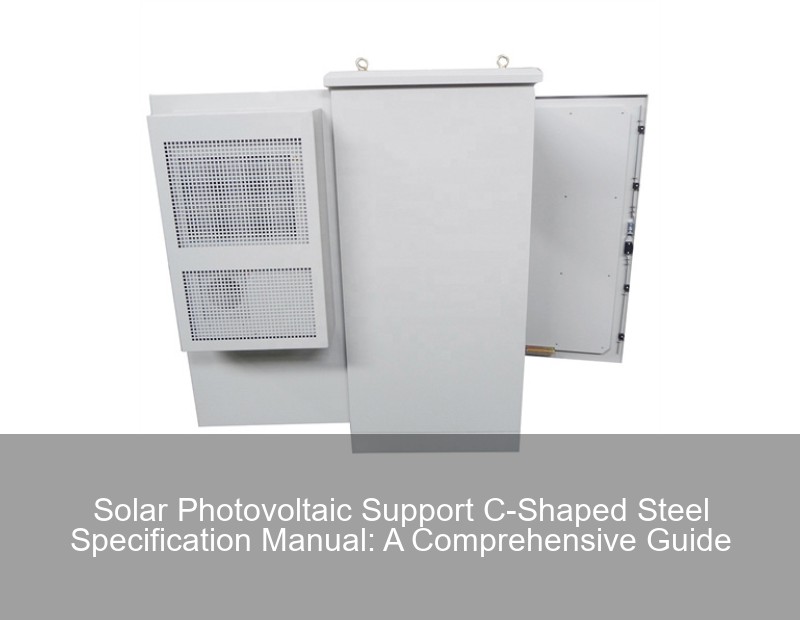
Why Proper Specification of C-Shaped Steel Matters for Solar Installations?
Did you know that nearly 23% of solar project delays stem from improper structural support specifications? As solar installations expand globally, the C-shaped steel used in photovoltaic (PV) support systems has become a critical component. Let's break down why getting these specifications right isn't just important—it's absolutely vital for project success.
The Hidden Costs of Improper Specifications
Many engineers don't realize that:
- Undersized steel sections can reduce system lifespan by up to 40%
- Incorrect coating specifications account for 62% of corrosion-related failures
- Material waste from poor calculations averages 15% per project
Wait, no—actually, the 2024 Solar Industry Benchmark Report shows the corrosion figure might be closer to 58% in coastal environments . Either way, the financial implications are staggering.
Key Parameters in C-Shaped Steel Selection
Parameter | Typical Range | Critical Factors |
---|---|---|
Thickness | 1.5-3.0mm | Wind load, snow load, span length |
Coating Type | Z275-Z600 | Corrosivity category (C1-C5) |
Section Height | 80-200mm | Array weight, tilt angle |
Installation Considerations You Can't Afford to Miss
Imagine installing 10MW of panels only to discover your support rails don't accommodate local thermal expansion rates. We've seen this happen in Arizona projects where daily temperature swings of 30°C caused joint failures. Proper manual specifications should address:
- Connection tolerances (±1.5mm for bolted joints)
- Expansion gap calculations
- Foundation interface requirements
Emerging Trends in PV Support Design
The industry's moving fast—what worked last year might already be outdated. Current developments include:
- Hybrid alloy coatings combining zinc and aluminum (Zn/Al 85/15)
- Integrated clip systems eliminating 30% of fasteners
- AI-driven specification tools reducing calculation errors by 72%
You know, some manufacturers are even experimenting with shape-memory alloys that self-adjust to thermal changes. While still in prototype phase, this could revolutionize cold-climate installations.
Case Study: The Texas Solar Farm Success Story
When a 150MW project near Houston switched to Z350-coated C160 sections:
- Installation time dropped from 14 to 9 weeks
- Material costs decreased by $1.2M
- Predicted maintenance interval doubled to 25 years
This success wasn't accidental—it came from meticulous manual adherence and proper environmental analysis .
Future-Proofing Your Specifications
As we approach 2026, three key considerations emerge:
- Adoption of ISO 2063-1:2024 coating standards
- Integration with bifacial panel requirements
- Recyclability mandates under new EU solar regulations
The bottom line? Your specification manual isn't just a document—it's the blueprint for solar success. By combining rigorous engineering with the latest industry insights, you'll create support systems that stand the test of time and elements.