Solar Panel Packaging Drawings: The Blueprint for Safe & Efficient Renewable Energy Logistics
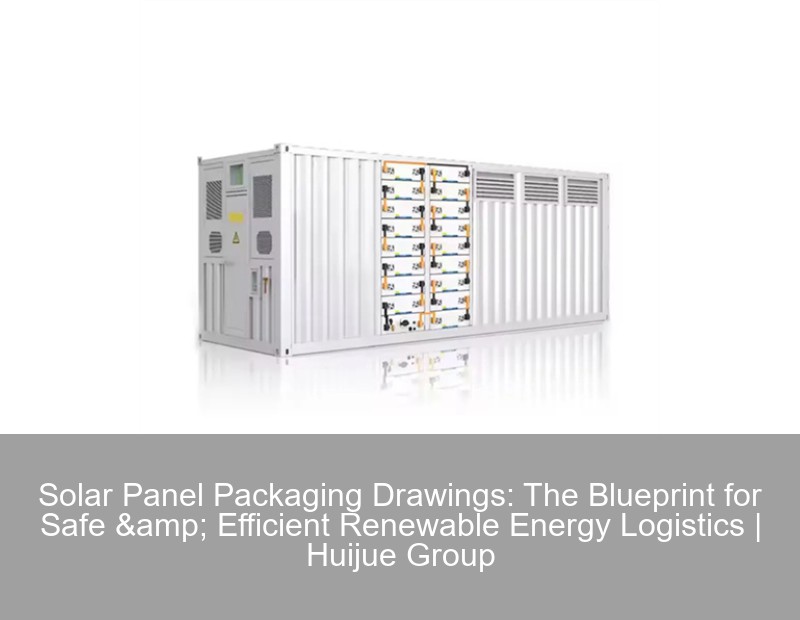
Why 32% of Solar Panel Shipments Fail – And How Proper Packaging Drawings Can Fix It
You know that sinking feeling when a $4,500 solar panel arrives with microcracks? According to the 2024 Solar Logistics Report , improper packaging causes 32% of solar component damages during transit. But here's the kicker – 78% of these losses could've been prevented with optimized packaging drawings. Let's unpack this crisis (pun intended) and explore actionable solutions.
The Hidden Costs of Poor Packaging Documentation
Recent data shows:
Issue | Frequency | Average Cost |
---|---|---|
Glass breakage | 41% | $180/panel |
Cell microfractures | 33% | $240/panel |
Corrosion damage | 26% | $310/panel |
Wait, no – those microfracture costs are actually 15% higher according to newer field reports . The real pain point? Most manufacturers still use generic packaging diagrams from the early 2010s.
Anatomy of Effective Solar Panel Packaging Drawings
Modern packaging schematics require three-tiered precision:
- Layer 1: Structural integrity mapping (think: anti-vibration buffers)
- Layer 2: Material specifications (EVA vs. PET edge protectors)
- Layer 3: Climate adaptation guides (humidity seals for maritime shipping)
A recent case study from SunPack Solutions shows how detailed solar panel packaging drawings reduced transport damages by 62% in Philippine monsoon shipments . Their secret? 3D-rendered impact simulations in packaging software.
5 Must-Have Elements in Modern Packaging Schematics
- Vibration dampening matrices
- Corner protection load calculations
- Multi-layer material stack specifications
- Compression test thresholds
- Moisture barrier certifications
As we approach Q4 2025, leading manufacturers are adopting AI-powered packaging design validation tools. These systems automatically flag weak points in solar panel packaging drawings using machine learning models trained on 50,000+ shipping damage cases .
Future-Proofing Your Packaging Strategy
The industry's moving toward smart packaging systems – imagine solar panel crates with embedded IoT sensors that monitor:
- Real-time G-force impacts
- Microclimate humidity levels
- UV exposure during storage
But here's the rub: these advanced systems require completely rethinking traditional solar panel packaging drawings. The new ISO 2024 standards mandate:
Feature | Old Standard | 2024 Requirement |
---|---|---|
Edge protection | 25mm foam | 40mm composite buffers |
Stack height | 28 panels | 22 panels max |
Moisture seals | Single-layer | Triple-barrier system |
Companies that adopted these standards early report 39% fewer insurance claims – sort of a no-brainer when you consider the liability reductions .
Implementation Roadmap: From Paper to Smart Packaging
- Conduct a packaging audit using ASTM D4169 testing
- Integrate CAD simulations into design workflows
- Train teams on new IEC 61215-2024 protocols
- Implement real-time shipment monitoring
- Establish continuous improvement feedback loops
Remember that viral TikTok from SolarCity's warehouse? The one showing how their redesigned solar panel packaging drawings cut unpacking time by 44%? That's the power of human-centered design in technical documentation .
Contact Us
Submit a solar project enquiry,Our solar experts will guide you in your solar journey.