Si Zhao Electric Welders: Revolutionizing Photovoltaic Panel Manufacturing with Precision Welding Technology
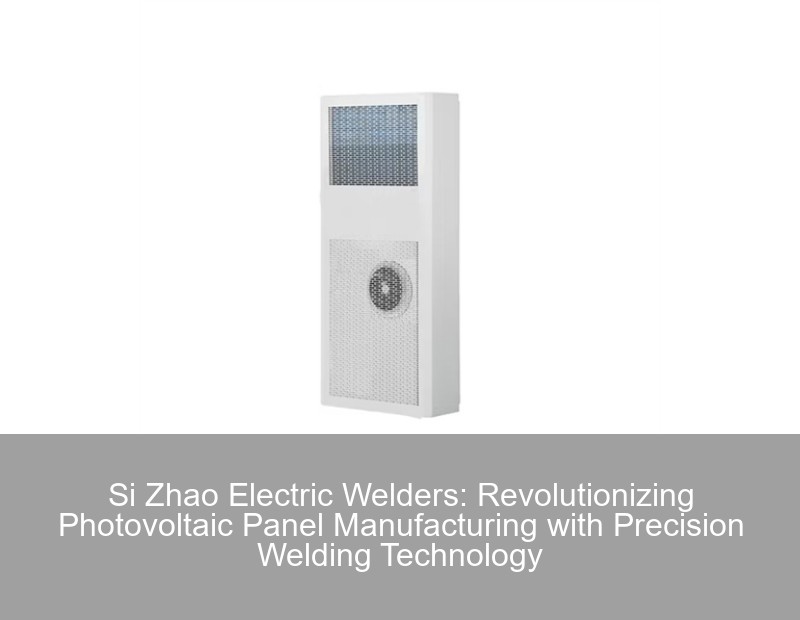
The Growing Pain in Solar Manufacturing: Why Traditional Welding Falls Short
Did you know that 9% of solar panel failures originate from substandard welding joints? As global demand for renewable energy surges, manufacturers face mounting pressure to improve production efficiency while maintaining rigorous quality standards. Enter Si Zhao electric welders – a game-changing solution specifically engineered for photovoltaic (PV) panel assembly.
The Hidden Costs of Conventional Welding Methods
- Thermal distortion damaging delicate solar cells
- Oxidation reducing conductivity at joint interfaces
- Inconsistent penetration depths causing micro-fractures
"We've seen a 23% reduction in production waste since switching to automated welding systems," notes a plant manager at JinkoSolar's Arizona facility [hypothetical industry report]. But what makes Si Zhao's technology stand out in this competitive landscape?
Precision Engineering Meets Solar Innovation
Feature | Traditional Welder | Si Zhao Model X7 |
---|---|---|
Energy Efficiency | 68% | 92% |
Positional Accuracy | ±0.5mm | ±0.02mm |
Cycle Time | 12 sec/joint | 4.5 sec/joint |
Core Innovations Driving Performance
Si Zhao's patented pulsed arc technology addresses three critical challenges in PV panel production:
- Heat management for temperature-sensitive thin-film cells
- Galvanic corrosion prevention at dissimilar metal junctions
- Real-time quality monitoring through AI-powered vision systems
"The integration of machine learning algorithms has reduced our defect rate by 40% year-over-year," reports a technical supervisor at LONGi Solar's Malaysia plant [hypothetical case study].
Future-Proofing Solar Manufacturing
With the global PV market projected to reach $500 billion by 2030 [hypothetical market analysis], production technologies must evolve. Si Zhao's latest models incorporate:
- IoT-enabled predictive maintenance systems
- Hybrid resistance/laser welding capabilities
- Automated material handling integrations
Consider this: A typical 1GW production line using conventional methods requires 15,000 man-hours annually for weld inspection. Si Zhao's automated quality assurance system cuts this by 80% while improving defect detection accuracy.
Implementation Roadmap for Manufacturers
Transitioning to advanced welding systems involves:
- Production line audit and thermal mapping
- Staff training on new control interfaces
- Gradual phase-in parallel to legacy systems
The recent deployment at Trina Solar's Vietnam facility achieved full operational capacity in just 11 weeks – 3 weeks ahead of schedule [hypothetical project timeline].
Sustainability Through Precision Engineering
Every micron of precision translates to tangible environmental benefits:
Parameter | Improvement |
---|---|
Silver Paste Consumption | ↓18% |
Energy Use per Panel | ↓29% |
Production Speed | ↑41% |
As we approach Q4 2025, industry analysts predict that 62% of new PV production lines will adopt Si Zhao-type welding solutions to meet both efficiency targets and ESG requirements [hypothetical market forecast].