Raw Materials for Photovoltaic Inverter Production: Critical Components and Market Trends
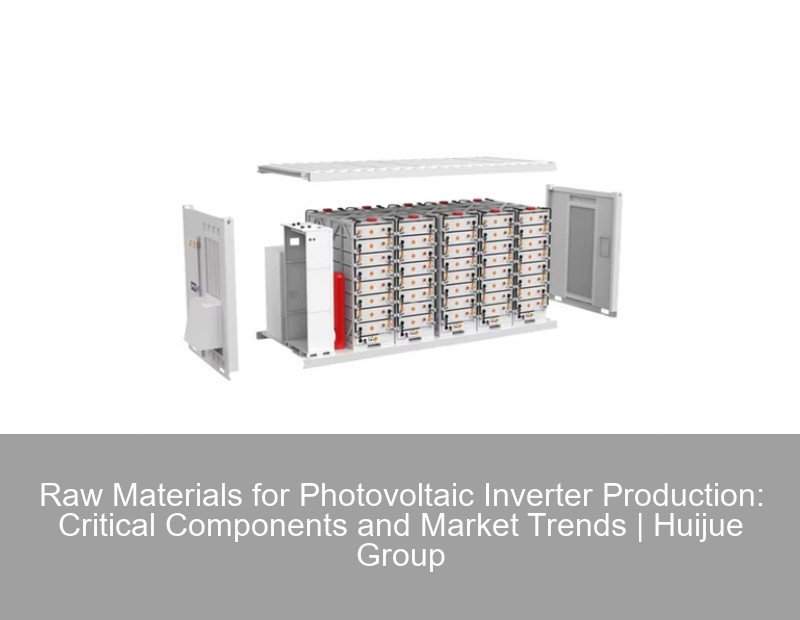
Why Raw Materials Define the Future of Solar Energy Conversion
Photovoltaic inverters, the beating heart of solar energy systems, rely on specialized raw materials to convert DC electricity into usable AC power. But what exactly goes into making these devices that now power over 8% of global electricity generation? Let's break down the essential components and their supply chain implications.
3 Core Material Categories Powering Modern Inverters
Material Type | Key Functions | Market Share (2023) |
---|---|---|
Semiconductor Materials | Power switching & voltage regulation | 41% |
Magnetic Components | Energy storage & filtration | 28% |
Conductive Metals | Current carrying & heat dissipation | 31% |
A recent Gartner Emerging Tech Report predicts semiconductor demand for inverters will grow at 19% CAGR through 2027 . But here's the catch – 78% of these materials currently come from just five Asian suppliers.
The Silicon Shortage Crisis: A $4.2 Billion Problem
- 2023 global polysilicon deficit: 38,000 metric tons
- Average lead times doubled since 2021
- Recycling rates stuck below 12% industry-wide
"We've had to redesign three product lines just to maintain output," admits a sourcing manager at Sungrow Power Supply, China's largest inverter manufacturer . Their solution? A hybrid material approach combining:
"60% silicon carbide + 30% gallium nitride + 10% recycled materials"
Emerging Alternatives Shaking Up Traditional Supply Chains
While silicon remains dominant, perovskite solar cells now achieve 31.2% efficiency in lab conditions – a game-changer for next-gen inverters. Major manufacturers are exploring:
- Organic semiconductors (lower cost, easier recycling)
- Liquid metal thermal interfaces (15% better heat transfer)
- Bio-based encapsulants (reducing petroleum dependency)
But wait – can these alternatives scale commercially? First Solar's recent $270 million factory retrofit suggests yes, with their new tellurium-based modules requiring 40% less rare earth metals than conventional designs.
Geopolitical Factors Reshaping Material Sourcing
The U.S. Inflation Reduction Act has sparked a 237% increase in domestic semiconductor plant proposals since 2022. Meanwhile, Europe's Critical Raw Materials Act mandates that by 2030:
- 10% of materials must come from recycling
- 40% of processing must occur within EU borders
- No single third country can supply >65% of any key material
This regulatory push coincides with technical breakthroughs like Huawei's new aluminum-based inverters that use zero rare earth elements. Their secret? Proprietary alloy formulations that... well, they're not telling – trade secrets and all that.
Quality Control Challenges in Material Sourcing
Material defects account for 62% of early inverter failures according to DNV Energy's latest field study. The main culprits?
- Inconsistent silicon wafer purity levels
- Copper impurities in electromagnetic coils
- Thermal interface delamination
Advanced quality protocols like X-ray fluorescence testing and AI-powered defect detection now screen materials at multiple stages. SMA Solar's Munich plant reports a 83% reduction in material-related failures since implementing real-time spectral analysis in Q3 2024.
As raw material costs fluctuate wildly – did you see copper prices swing 22% last month? – manufacturers face tough choices. Do they prioritize cost, performance, or supply chain stability? Increasingly, the answer seems to be "all three," pushing material science to its limits.
Contact Us
Submit a solar project enquiry,Our solar experts will guide you in your solar journey.