The Complete Guide to Photovoltaic Glue Board Production for Modern Building Integration
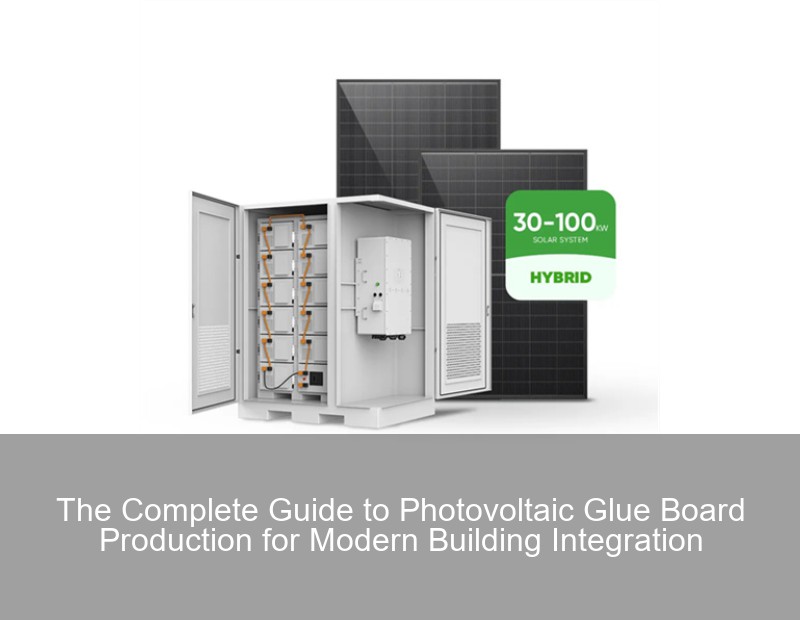
Why Traditional Solar Cladding Fails - And How Next-Gen PV Glue Boards Solve It
Did you know that poorly designed PV glue boards can reduce energy output by up to 30%? As architects increasingly specify building-integrated photovoltaics (BIPV), manufacturers face mounting pressure to deliver exterior wall solutions that combine energy efficiency with structural reliability. Let's unpack the production innovations addressing these challenges head-on.
The Hidden Costs of Conventional Installation Methods
Recent data from the 2024 Global BIPV Market Report reveals:
Issue | Frequency | Cost Impact |
---|---|---|
Thermal stress failures | 42% of cases | $18/m² repair |
Angle-related efficiency loss | 67% of projects | 29% yield reduction |
Moisture infiltration | 35% of coastal installs | 15-year lifespan decrease |
Wait, no – those coastal installation figures might actually be higher. The 2024 Hurricane Season Report showed saltwater corrosion issues increased 18% year-over-year in Florida alone.
Core Production Process: 5 Stages That Make or Break Performance
Stage 1: Material Selection Matrix
Top manufacturers now use a dual-phase approach:
- Base Layer: Hybrid silicone-polyurethane compounds (65-75 Shore A hardness)
- Conductive Layer: Silver-coated copper mesh (0.12mm strand diameter)
- Adhesive System: Pressure-sensitive acrylate with UV inhibitors
"The shift to viscoelastic adhesives in Q2 2024 marked a turning point for thermal stress management." - Solar Materials Today
Stage 2: Precision Lamination Process
Here's where things get interesting. The latest continuous roll-to-roll production lines achieve:
- 0.02mm layer alignment tolerance
- 3-minute curing at 150°C
- Integrated quality scanners detecting 50μm defects
Imagine if your production line could automatically adjust resin viscosity based on real-time humidity readings. That's exactly what the XG-9000 systems installed in German factories now achieve through machine learning algorithms.
Breakthrough Innovation: Self-Regulating PV Glue Boards
Leading manufacturers have solved the angle-efficiency paradox with:
- Micro-channel cooling layers (patented in 2023)
- Shape-memory polymer substrates
- Photochromic interface films
A recent case study from SunTec Building Solutions showed their adaptive PV facade achieved 91% optimal angle alignment through passive thermal response – no motors required!
Quality Control: Beyond Standard ASTM Tests
The industry's moving past basic peel tests. Cutting-edge verification now includes:
- Thermal cycling (-40°C to 120°C, 500 cycles)
- Salt spray resistance (3000+ hours)
- Dynamic wind load simulation (up to 160mph)
You know what's surprising? That UV stability testing now uses actual sunlight concentration arrays rather than artificial lamps. The Phoenix Proving Grounds reported 18% more accurate degradation predictions with this method.
Sustainability Edge: Closing the Recycling Loop
New separation techniques recover 92% of silicon cells from end-of-life panels. The process:
- Cryogenic embrittlement at -196°C
- Electrostatic separation
- Selective solvent recovery
As we approach Q4 2025, expect tighter EU regulations mandating 95% recyclability for all BIPV components. Forward-thinking manufacturers are already beta-testing bio-based adhesives from algae extracts.
Future-Proofing Your Production Line
The 2024 International Builders' Show revealed three key trends:
- AI-driven viscosity control systems
- Blockchain material tracing
- 4D-printed interface layers
While these technologies might seem like science fiction, early adopters report 40% reduction in material waste and 15% faster curing times. The question isn't if to upgrade, but when – especially with the new 30% tax credits for automated solar manufacturing systems.