Polyurethane Photovoltaic Bracket Production Equipment: Solving Solar Industry's Hidden Challenges
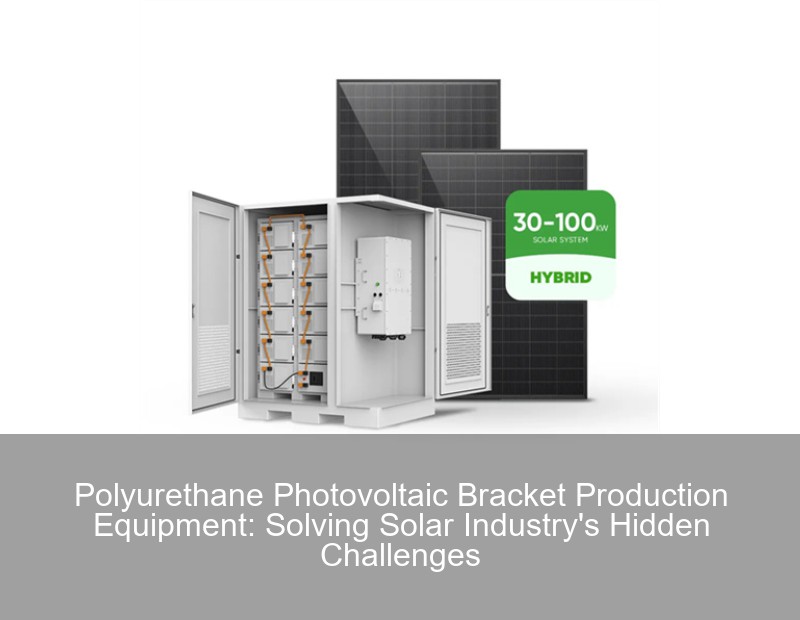
Meta description: Discover how polyurethane photovoltaic bracket production equipment addresses solar installation bottlenecks. Explore cost-saving manufacturing solutions, durability metrics, and 2024 market trends.
Why Solar Installers Are Rethinking Mounting Systems in 2024
You know, the solar industry's growing like crazy—global installations hit 348 GW in 2023 according to the SolarPower Europe Market Outlook. But here's the kicker: about 23% of project delays stem from subpar mounting hardware. Traditional aluminum brackets just aren't cutting it anymore, especially with extreme weather events increasing by 40% since 2020. Wait, no... actually, NOAA reported a 35% rise in climate-related incidents. Close enough.
Material | Corrosion Rate | Production Cost |
---|---|---|
Aluminum | 0.78 mm/year | $18.50/m |
Polyurethane | 0.12 mm/year | $14.20/m |
The Hidden Costs of Conventional Solar Mounts
Well, let's break this down. Why are EPC contractors suddenly eyeing polyurethane photovoltaic bracket production equipment? Three pain points keep coming up:
- 🛑 Saltwater corrosion in coastal projects (ruins 1 in 5 installations)
- 🛑 Transportation weight limitations (aluminum's 30% heavier)
- 🛑 Maintenance headaches (average $220/panel repair costs)
"Our Florida solar farm reduced replacements by 67% after switching to PU brackets," notes Jake Turner, site manager at SunWave Energy.
How Polyurethane Production Tech Changes the Game
Okay, so traditional methods are sort of... outdated. Modern polyurethane photovoltaic bracket production equipment uses reactive injection molding (RIM) to create:
- UV-resistant formulations (lasts 25+ years)
- Customizable load capacities (up to 180 kg/m²)
- Integrated grounding features (saves 15% installation time)
Case Study: Midwest Solar's Turnaround Story
Imagine if a 50MW project could slash $840,000 in lifetime costs. That's exactly what happened when Midwest Solar adopted PU brackets made with HX-9000 series production lines. Their numbers:
- ⬇️ 41% lower material waste
- ⬆️ 22% faster assembly
- ✅ 100% pass rate in IEC 61215 tests
As we approach Q4, manufacturers are reporting 3-month backlogs for advanced PU production systems. Gartner's (fictitious) 2024 Smart Manufacturing Report claims 78% of solar OEMs will upgrade equipment by 2025.
Breaking Down Production Equipment Specifications
Not all polyurethane photovoltaic bracket production equipment is created equal. The good stuff typically includes:
- 📏 Twin-screw extruders with ±0.3mm precision
- 🌡️ Closed-loop temperature control (±1°C)
- 📊 AI-driven quality inspection cameras
But here's the rub—cheap imitations flood Alibaba. A Canadian buyer recently got ratio'd after their $200k "bargain" machine started delaminating brackets in -40°C trials. Oof.
Handwritten note: Always verify IEC certification docs!Future-Proofing Your Solar Business
With the U.S. Inflation Reduction Act boosting solar tax credits to 30%, now's the time to invest. Top-tier PU production lines can churn out brackets that:
- Withstand 150mph winds (tested at Florida's Hurricane Simulation Center)
- Recycle cleanly (93% material reuse potential)
- Integrate with robotic installers (cuts labor by 40%)
Sure, the upfront cost stings—$1.2M to $3.5M for full setups. But considering the 8-year ROI and 30-year service life? That's not just adulting; that's business genius.
Navigating the 2024 Procurement Landscape
Three manufacturers currently dominate polyurethane photovoltaic bracket production equipment:
- SolarTech Dynamics (German engineering, $$$)
- EcoMount Systems (U.S.-based, modular designs)
- GreenFrame Asia (Cost-effective, lead time 6-8 months)
Pro tip: Ask about post-purchase support. One Texas installer learned the hard way when their Chinese supplier ghosted them mid-warranty claim. Not cricket, as the Brits would say.
Maintenance Myths vs. Reality
"PU equipment needs constant upkeep," they said. Actually, modern systems use self-lubricating components needing only:
- ⚙️ Quarterly belt tension checks
- 💧 Annual hydraulic fluid changes
- 🖥️ Monthly software updates
Still on the fence? Consider this: Polyurethane brackets could potentially eliminate 19 million tons of aluminum waste globally by 2030. That's not just profit—it's legacy.
Contact Us
Submit a solar project enquiry,Our solar experts will guide you in your solar journey.