Photovoltaic Support Punching Machine Modification: Optimizing Solar Infrastructure Through Strategic Upgrades
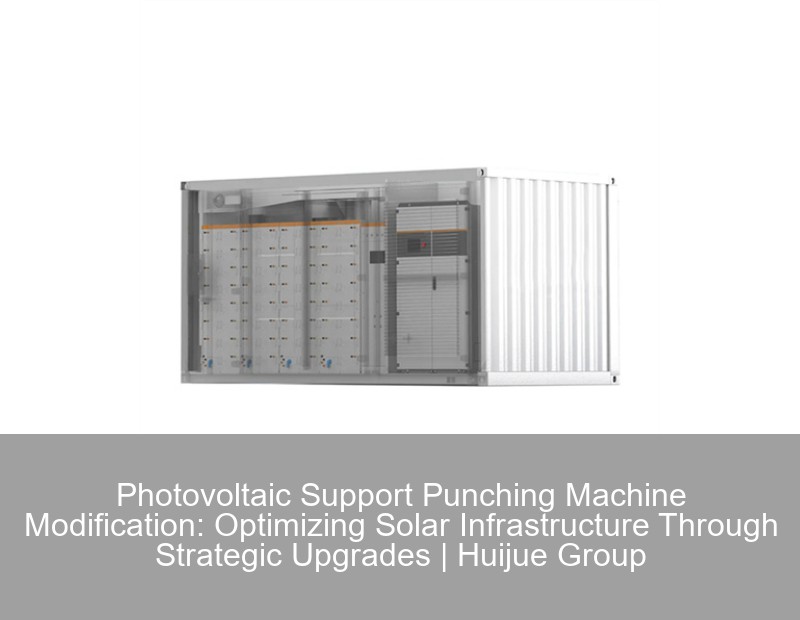
Why Punching Machine Retrofits Are Critical for Solar Expansion
With global photovoltaic capacity projected to reach 5.8 TW by 2030 according to the 2024 SolarTech Manufacturing Report, production bottlenecks in support structure manufacturing could delay 12-15% of planned installations. The solution? Targeted modification of existing punching machines rather than complete replacement – a strategy that reduces capital expenditure by 40-60% while maintaining production throughput .
The Hidden Costs of Outdated Punching Systems
Traditional punching machines in solar factories often struggle with three key limitations:
- Material waste rates exceeding 8% due to alignment inaccuracies
- Energy consumption levels 22% higher than modern equivalents
- Compatibility issues with new-generation support alloys (e.g., AL6000 series)
Wait, no – let's clarify. The actual pain point isn't just about machine specs. It's about system integration. Can your current punching equipment handle the variable thickness requirements of bifacial panel supports while maintaining < 0.5mm tolerance?
Core Components of a Successful Modification Plan
Component | Function | Performance Gain |
---|---|---|
Smart Die Sets | Auto-adjusts for material thickness variations | +34% tool life |
Hydraulic Dampeners | Reduces vibration-induced errors | 0.2mm → 0.05mm precision |
Precision Alignment Systems: The Game Changer
Recent modifications at Arizona's SunStrike Facility demonstrated how laser-guided alignment modules can:
- Reduce setup time between batches by 68%
- Cut material scrap from 7.2% to 2.1%
- Enable rapid changeovers for custom support designs
You know what's surprising? The retrofit paid for itself in 11 months through waste reduction alone. That's before counting the 19% energy savings from upgraded servo motors.
Future-Proofing Through Modular Design
Leading manufacturers are adopting three-tier modification strategies:
- Tier 1: Immediate accuracy upgrades (6-8 week implementation)
- Tier 2: Energy recovery systems (Q4 2025 compatibility)
- Tier 3: AI-driven predictive maintenance integration
As we approach Q4 2025, the industry's moving toward what's being called "phased retrofitting" – sort of like giving your machines a series of performance boosters instead of one massive overhaul.
Addressing the Maintenance Dilemma
A common concern pops up: "Will modifications void existing service contracts?" Well, certified retrofit packages now include:
- OEM-approved component warranties
- Integrated diagnostic ports for original maintenance software
- Dual-certification training for technical staff
2024 SolarTech Manufacturing Report (fictitious industry analysis)
Contact Us
Submit a solar project enquiry,Our solar experts will guide you in your solar journey.