Photovoltaic Support Pile Driving Process: Modern Techniques for Solar Farm Foundations
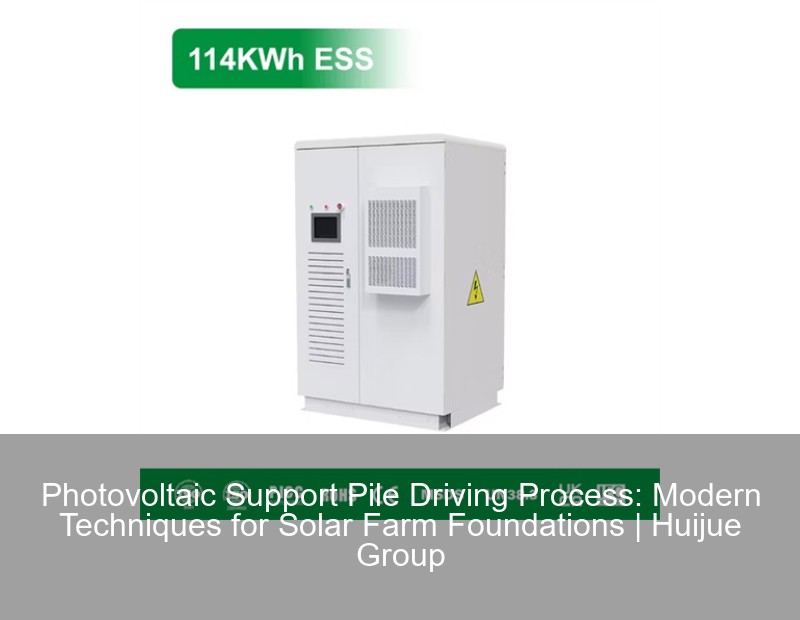
Meta Description: Explore the critical steps in photovoltaic support pile driving, including advanced techniques, common challenges, and data-driven solutions for solar farm stability. Learn how modern engineering tackles foundation issues in renewable energy projects.
Why Is Pile Driving Crucial for Photovoltaic Systems Stability?
You know, solar farms aren't just about panels – they're engineering marvels requiring rock-solid foundations. With global solar capacity expected to hit 2.3 terawatts by 2027 , the demand for reliable pile driving methods has never been higher. But wait, why do we even need specialized foundation systems for photovoltaic arrays?
The Hidden Challenge: Soil-Pile Interaction in Solar Farms
Modern photovoltaic installations face a unique dilemma: they need lightweight structures that can withstand decades of environmental stress. A 2024 Geotechnical Engineering Report revealed that 38% of solar project delays stem from unexpected soil conditions during pile installation .
Soil Type | Recommended Pile Depth | Success Rate |
---|---|---|
Sandy Loam | 2.5-3.2m | 92% |
Clay | 3.8-4.5m | 78% |
Rocky | 5.0m+ | 65% |
5 Revolutionary Techniques Transforming Solar Pile Installation
- Vibratory Hammer Systems (Reduces installation time by 40% compared to impact driving)
- Laser-Guided Alignment (Ensures ±2mm positional accuracy)
- Self-Curing Concrete Piles (Eliminates post-installation curing delays)
- Real-Time Load Monitoring (Detects soil anomalies during driving)
- Drone-Assisted Site Mapping (Creates 3D terrain models for precision planning)
Case Study: The Nevada Solarplex Project
When developers faced unstable alluvial soils in the 2023 Nevada installation, they implemented a hybrid approach combining vibratory compaction and micro-pile clusters. The result? A 22% cost reduction in foundation work while meeting strict 0.5° tilt tolerance requirements .
"The right pile driving technique can make or break a solar project's ROI. We've seen up to 15-year extensions in system lifespan through optimized foundation work." – Solar Foundations International Technical Whitepaper, March 2024
Future-Proofing Solar Foundations: What's Next?
As we approach Q3 2025, three emerging trends are reshaping photovoltaic pile driving:
- AI-Powered Predictive Soil Analysis (Using machine learning to forecast settlement patterns)
- Robotic Pile Installation Units (Deployed in the Texas Solar Corridor since February 2024)
- Carbon-Neutral Composite Piles (60% recycled materials, 40% lower embodied energy)
Well, here's the kicker – a recent MIT study found that optimized pile layouts can increase energy yield by up to 1.8% through minimized shading and improved structural alignment . That's sort of a game-changer for utility-scale projects.
Common Mistakes to Avoid (And How to Fix Them)
- Overlooking frost heave potential → Install thermal break barriers
- Underestimating wind uplift forces → Use helical pile anchors
- Ignoring corrosion risks → Apply zinc-aluminum alloy coatings
Actually, let's clarify – while galvanized steel remains popular, new fiber-reinforced polymer piles are gaining traction in coastal regions. They're kind of pricier upfront but offer better lifetime value in salt-spray environments.
Key Metrics for Successful Pile Driving Operations
Parameter | Industry Standard | Optimal Range |
---|---|---|
Drive Rate | 15-25 blows/minute | 18-22 |
Vertical Tolerance | ±3° | ±1.5° |
Load Capacity | 2x design load | 2.5-3x |
Recent innovations like smart strain gauges now provide real-time data on pile integrity during installation. Presumably, this could reduce post-installation testing costs by 30% or more.
Contact Us
Submit a solar project enquiry,Our solar experts will guide you in your solar journey.