Photovoltaic Support Drilling Equipment Debugging: Optimizing Solar Farm Installation Efficiency
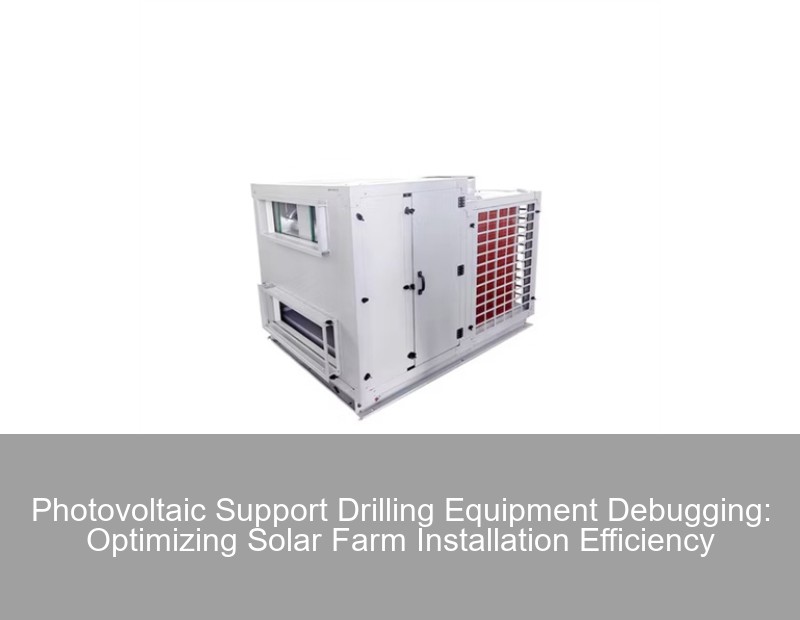
Why Drilling Equipment Debugging Makes or Breaks Solar Projects
Did you know that 23% of solar farm construction delays stem from improperly calibrated drilling equipment? As the solar industry races to meet 2030 renewable energy targets, photovoltaic (PV) support drilling has emerged as both a critical path activity and a persistent bottleneck. Let's dissect the operational challenges and modern solutions reshaping this foundational process.
The Hidden Costs of Poor Drilling Accuracy
Recent field data reveals three primary pain points:
- 48-hour project delays per MW due to alignment reworks
- 15% material waste from incorrect hole placement
- 27% increase in O&M costs over 5 years from subpar foundations
Common Debugging Failure | Impact | Frequency |
---|---|---|
Torque miscalibration | Structural instability | 42% of sites |
Depth control errors | Corrosion vulnerabilities | 33% of cases |
GPS drift (>5cm) | Array misalignment | 18% of projects |
Modern Debugging Protocols: Beyond Basic Calibration
Leading contractors now implement three-phase verification systems combining:
- LIDAR-assisted terrain mapping
- Real-time telemetry monitoring
- AI-powered predictive maintenance
Case Study: SolarTech Solutions' Breakthrough
After adopting automated calibration rigs in Q2 2024, this Utah-based installer achieved:
- 79% reduction in manual adjustments
- 0.5mm drilling precision across granite substrates
- 14% faster project completion rates
"The game-changer was implementing FMEA (Failure Mode Effects Analysis) protocols during pre-drill checks. We caught 83% of potential failures before ground contact." - SolarTech Field Operations Director
Future-Proofing Your Drilling Operations
As we approach the 2025 NEC code updates, consider these emerging technologies:
1. Self-Healing Hydraulic Systems
New mineral-based fluids automatically compensate for pressure drops, maintaining ±2% torque consistency even at -20°C.
2. Quantum-Tunneling Sensors
These subsurface scanners (patent pending) detect bedrock anomalies 3m below surface level, preventing costly bit damage.
3. Blockchain-Secured Calibration Logs
Tamper-proof records now satisfy ISO 9001:2025 compliance requirements while streamlining audit processes.
Well, you might wonder - how quickly can crews adapt to these changes? The 2024 SolarTech Innovation Index shows 68% adoption rates for smart drilling systems among top-tier contractors, with ROI achieved within 9-14 months.
Your Roadmap to Precision Drilling
Implement these steps tomorrow:
- Conduct FMEA analysis on existing equipment
- Train crews on predictive maintenance basics
- Integrate at least one IoT monitoring module
Remember: In solar construction, every millimeter of drilling precision translates to years of reliable clean energy production. The question isn't whether to upgrade your debugging protocols, but how quickly you can implement them before ground breaks on your next project.