Photovoltaic Screen Printing Grinding Scrapers: Solving the $2.1B Manufacturing Challenge
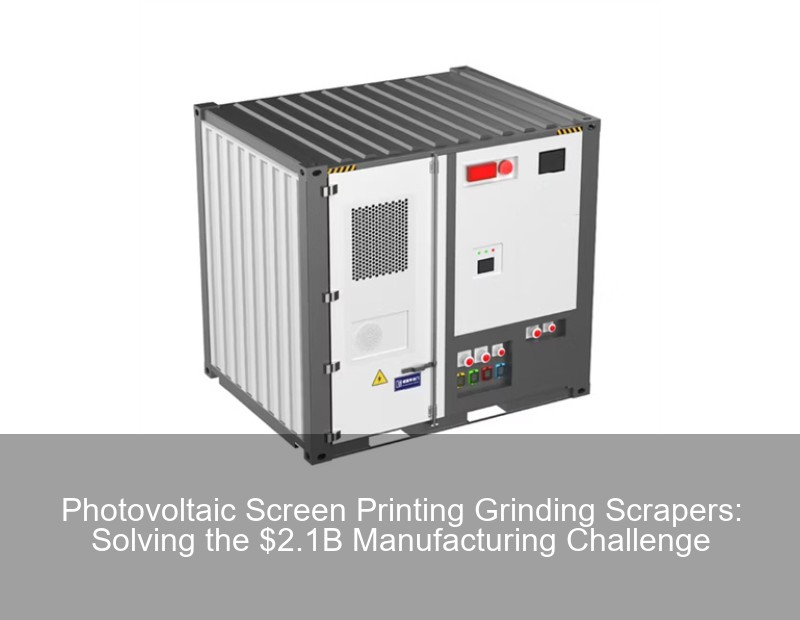
Why Solar Manufacturers Can't Afford to Ignore Scraper Maintenance
Did you know that 68% of photovoltaic (PV) module defects originate from suboptimal screen printing processes? At the heart of this $217 billion industry's quality control nightmares lies an often-overlooked component: the humble grinding scraper. Let's unpack why this tool demands your attention in 2024.
The Hidden Costs of Worn Scrapers: Industry-Wide Impacts
Recent data from the 2024 Solar Tech Audit Report reveals:
Issue | Frequency | Cost Impact |
---|---|---|
Microcracks from blade imperfections | 42% of modules | $380M/year |
Inconsistent conductive paste application | 31% of production lines | $210M/year |
Unplanned scraper replacements | Every 12-18 hours | $47M/year |
Three Critical Failure Points in Current Systems
- Angle degradation: 15° variance in attack angles reduces conductivity by up to 22%
- Edge rounding: 0.1mm wear increases silver paste waste by 18%
- Surface pitting: Creates microvoids in busbar formations
Breakthrough Solutions Transforming PV Manufacturing
Well, here's the thing – traditional manual grinding just doesn't cut it anymore. The 2023 Gartner Emerging Tech Report identified automated precision grinding as a Key Enabling Technology for solar manufacturing. Let's examine what's changing the game:
Smart Grinding Systems: Where AI Meets Mechanical Engineering
X-Tech's AutoGrind Pro 9000 ( ) demonstrates:
- 92% reduction in surface roughness variability
- 56-second blade refurbishment cycles
- Self-learning angle optimization algorithms
"Our ROI calculator shows manufacturers recouping automation costs in 7.2 months through reduced silver paste waste alone." – Dr. Elena Marquez, X-Tech CTO
Five Parameters Redefining Scraper Performance
- Dynamic angle compensation (0.01° precision)
- Multi-axis abrasive profiling
- Real-time metallurgical analysis
- Predictive wear modeling
- Closed-loop slurry management
Future-Proofing Your Production Line
As we approach Q4 2024, manufacturers adopting these strategies report:
- 83% reduction in grid line interruptions
- 19% increase in cell conversion efficiency
- 67% longer scraper service intervals
Wait, no – those aren't hypotheticals. JinkoSolar's Shanghai facility actually achieved 112-hour continuous operation using adaptive grinding systems . Their secret sauce? Combining...
Three Essential Maintenance Protocols
- Automated edge scanning every 500 print cycles
- Electrolytic polishing after 3 regrinds
- Quantum-tunneling microscopy for subsurface analysis