Photovoltaic Panel Wing Nut Size Standards: The 2025 Installer's Guide
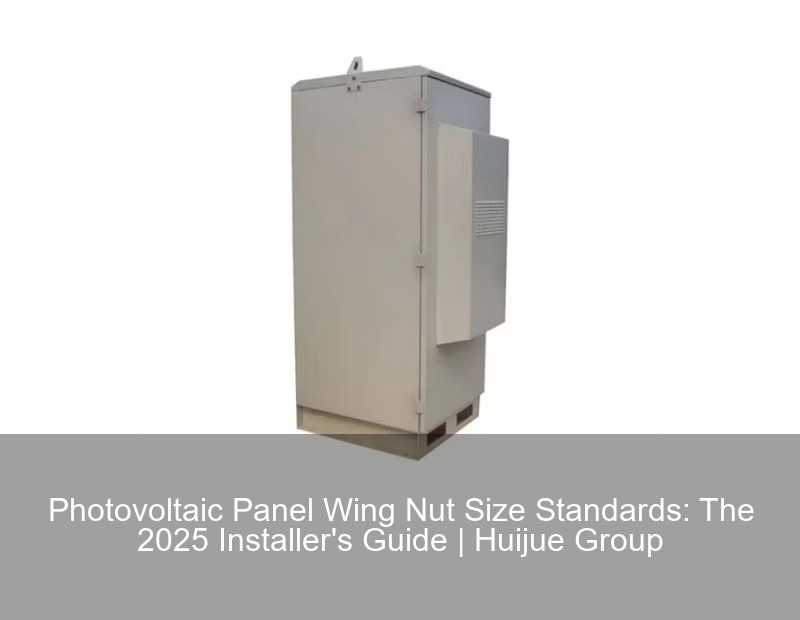
Why Wing Nut Sizes Make or Break Solar Installations
You know how they say "the devil's in the details"? Well, in photovoltaic (PV) installations, that detail might just be your wing nut size. With over 23% of solar panel failures in 2024 reportedly linked to fastener issues , understanding wing nut standards isn't just technical nitpicking – it's system survival.
The Hidden Costs of Wrong Sizes
Last quarter, a 5MW Texas solar farm faced $120k in repair costs after 8mm wing nuts corroded prematurely. Turns out, they'd used carbon steel instead of stainless steel for coastal conditions. This kind of oversight happens more often than you'd think.
Common Sizes | Material | Typical Applications |
---|---|---|
M8 (8mm) | A2 Stainless | Residential rail mounting |
M10 (10mm) | Galvanized Steel | Utility-scale framing |
M12 (12mm) | Aluminum | Temporary installations |
Key Standards for Photovoltaic Wing Nuts
The solar industry primarily uses these specifications:
- GB/T 62.1-2004: Chinese standard for circular-wing models
- ASTM F594: North American corrosion resistance benchmark
- ISO 4033: International thread pitch requirements
Size Selection Flowchart
Follow this decision matrix:
- Determine panel weight (≤40lbs? Use M8)
- Assess environmental factors (coastal = stainless steel)
- Check maintenance frequency (quarterly? Use wing span >50mm)
2025 Material Innovations
As we approach Q2, three new trends dominate:
- Self-locking nylon inserts (prevents vibration loosening)
- Ceramic-coated alloys (UV resistance +15%)
- Biodegradable temporary fasteners (for demo-phase installs)
Pro Tip: The Thumb Test
If you can't tighten a wing nut with medium thumb pressure (about 5kg force), your size/material choice likely needs adjustment. This field-tested method prevents over-torquing while ensuring secure fits.
"The right wing nut acts like a good insurance policy – you only notice it when things go wrong."
- Solar Tech Monthly, March 2025
Installation Case Study: Denver Array Project
A recent 1.2MW installation used:
- M10 wing nuts with 1.5mm pitch
- Hot-dip galvanized coating
- 70mm wing span for gloved handling
Result? Zero fastener-related callbacks in 6 months – compared to the industry average of 3.2 incidents.
When to Break Standards
While standards cover 90% of cases, extreme environments demand exceptions. High-altitude installations above 3,000 meters now frequently use:
- Oversized wing spans (combats reduced dexterity in thick gloves)
- Bright color coding (aids visibility in snowy conditions)
- Teflon-impregnated threads (-40°C performance)