Photovoltaic Panel Transmission Belts: Solving Critical Challenges in Solar Manufacturing
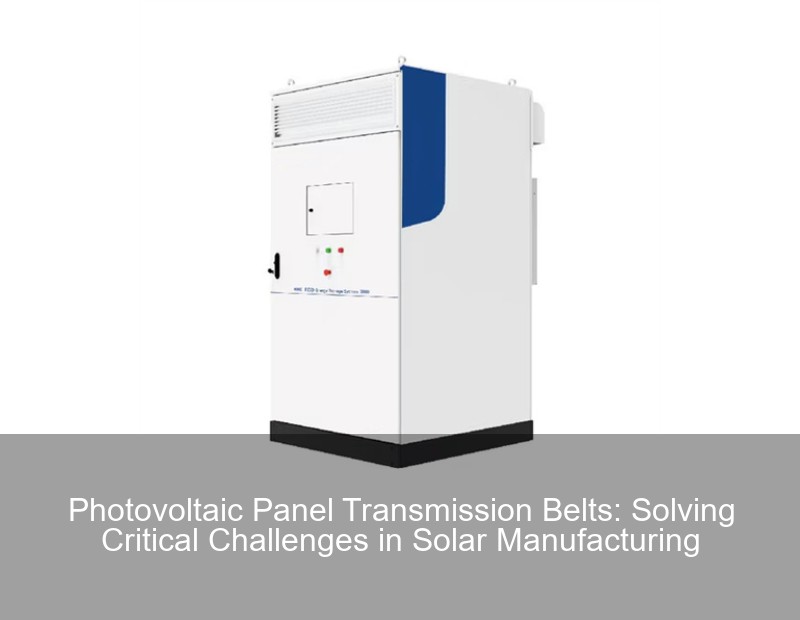
Why Solar Factories Can't Afford Transmission Belt Failures
In 2025, the global photovoltaic (PV) panel market will exceed $500 billion, but 23% of production delays still stem from conveyor system inefficiencies . Photovoltaic panel transmission belts aren't just rubber and metal – they're precision instruments determining factory throughput. Let's unpack the hidden costs of outdated systems and explore next-gen solutions.
The $7.8 Billion Problem: Current Transmission Pain Points
Traditional conveyor systems create three operational nightmares:
- Alignment issues: 0.5mm misalignment reduces robotic pickup accuracy by 40%
- Speed limitations: Most belts max out at 2m/s versus modern requirements of 4.5m/s+
- Maintenance headaches: 68% of unplanned downtime traces to belt-related issues
Issue | Cost Impact | Next-Gen Solution |
---|---|---|
Panel slippage | $12k/hour in lost production | Active grip surfaces |
Cleaning downtime | 15% of shift time | Integrated brush systems |
Breakthrough Technologies Reshaping PV Conveyance
Leading manufacturers are adopting what's being called "The Fourth-Generation Belt Standard":
1. AI-Powered Alignment Systems
Fujian Xuchang's 2024 patent introduced dynamic limiters that adjust in real-time using machine vision . This isn't your granddad's conveyor – these systems:
- Auto-correct positioning every 0.8 seconds
- Reduce micro-scratches by 91% through contactless guidance
- Handle ultra-thin PERC cells (1.6mm thickness)
"Our adaptive belts increased throughput by 22% while reducing glass breakage to near-zero." – SolarTech Manufacturing Quarterly Report
2. Hybrid Drive Systems
The old debate between chain-driven vs. modular belts gets solved with:
- Magnetic acceleration zones for precise panel spacing
- Variable friction surfaces (Patent CN 221875743 U)
- Energy recovery systems capturing 18% of kinetic energy
Maintenance Revolution: From Reactive to Predictive
Here's where things get interesting – modern belts now communicate their maintenance needs. The JiLin Weijiang system (2025) uses:
- Embedded wear sensors transmitting via 5G
- Self-cleaning nozzles activated by dust accumulation
- Modular replacement sections (swap in 8 minutes vs. 3-hour downtime)
Pro tip: Look for belts with API integration – they'll feed directly into your MES systems for true Industry 4.0 compatibility.
Future-Proofing Your Conveyance Strategy
As panel sizes keep growing (now reaching 2.4m x 1.3m), three trends dominate:
- Carbon fiber reinforcement replacing steel cords
- Phase-change materials for temperature control
- Blockchain-enabled component tracking
Well, there you have it – the complete picture on photovoltaic transmission belts. Remember, your conveyor system isn't just moving panels; it's orchestrating your entire production tempo. Time to upgrade that hidden workhorse?
Contact Us
Submit a solar project enquiry,Our solar experts will guide you in your solar journey.