Laser Irradiation in Photovoltaic Panel Manufacturing: Key Processes and Innovations
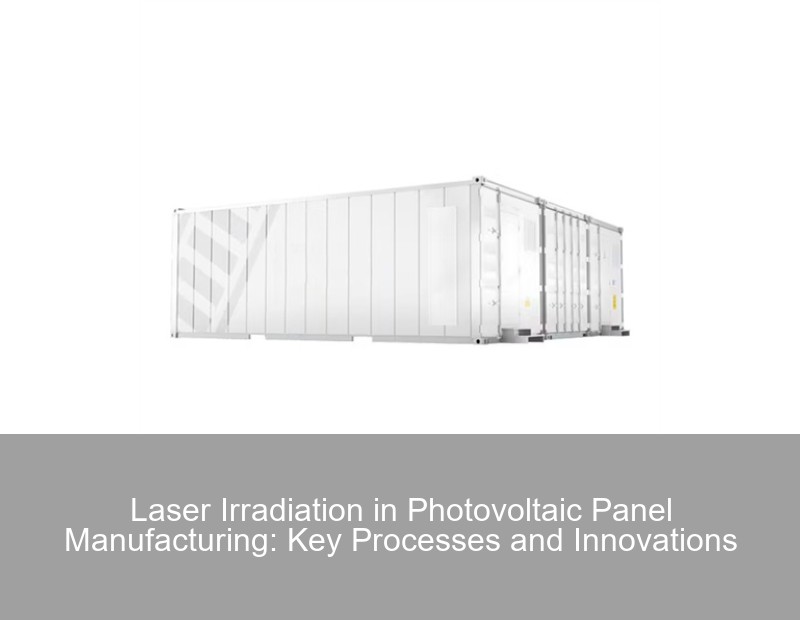
Why Solar Manufacturers Are Rethinking Traditional Production Methods
Did you know over 23% of silicon waste in photovoltaic (PV) production comes from imprecise cutting techniques? As the solar industry pushes for higher efficiency rates and thinner wafers, conventional mechanical methods are becoming sort of obsolete. Enter laser irradiation - the game-changing technology that's reshaping PV manufacturing landscapes.
The Precision Problem in Solar Panel Production
Traditional diamond wire cutting leaves micro-cracks that reduce cell efficiency by up to 1.5% absolute. Laser irradiation offers:
- Non-contact material processing
- Sub-micron accuracy
- Thermally optimized ablation
Technique | Kerf Loss | Surface Defects |
---|---|---|
Diamond Wire | 150μm | High |
Laser Irradiation | 40μm | Low |
Case Study: TOPCon Cell Edge Isolation
Trina Solar's 2024 pilot project achieved 26.1% conversion efficiency using ultraviolet laser doping. The key? Precise control of beam parameters:
- Pulse duration: 10-15ns
- Spot size: 20μm
- Fluence: 2.5J/cm²
Four Revolutionary Applications of Laser Tech
Well, you might ask - what makes lasers so versatile in PV manufacturing? Let's break it down:
1. Laser-Doped Selective Emitters
By using green lasers (532nm), manufacturers can create localized doping regions without damaging passivation layers. The 2023 ITRPV Roadmap predicts this technique will dominate 78% of PERC cell production by 2026.
2. Anti-Reflective Surface Texturing
Femtosecond lasers create micro-pyramids that reduce reflection losses to <2% across visible wavelengths. JinkoSolar's latest patent (US2024178321) reveals a 0.8% efficiency gain using this method.
"Laser texturing enables tunable light trapping structures that mechanical etching simply can't match." - 2024 SolarTech Innovation Report
The Cost-Efficiency Equation
While laser systems require higher upfront investment ($2.8M vs. $1.2M for traditional tools), they offer:
- 38% lower operating costs
- 60% faster processing speeds
- 92% material utilization rate
Maintenance Considerations
Actually, modern fiber lasers need 45% less maintenance than CO₂ systems. The catch? You'll want to monitor:
- Beam quality (M² factor)
- Gas purity levels
- Optical path contamination
Future Trends: Where's the Industry Headed?
As we approach Q4 2025, three developments are worth watching:
- Hybrid laser/plasma etching systems
- AI-driven beam path optimization
- Ultrafast laser crystallization for perovskite layers
Manufacturers adopting these technologies could potentially achieve 30% module efficiencies by 2028 - a target that seemed impossible just five years ago.
Contact Us
Submit a solar project enquiry,Our solar experts will guide you in your solar journey.