Photovoltaic Panel Factory Hoisting: Critical Requirements and Modern Standards You Can’t Afford to Ignore
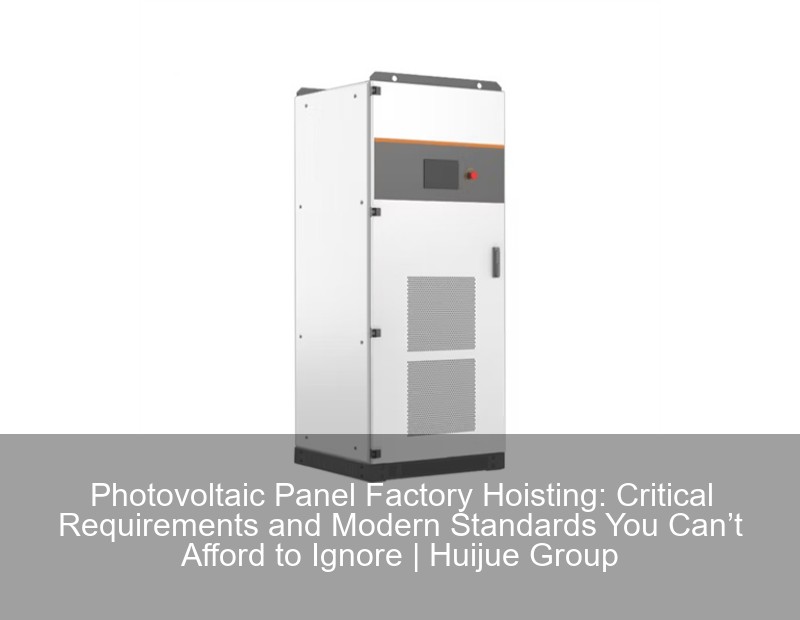
Meta Description: Discover essential photovoltaic panel hoisting standards, safety protocols, and cutting-edge practices for factory installations. Learn how to avoid costly errors with 2024 industry benchmarks.
Why Proper Hoisting Practices Make or Break Solar Projects
Did you know 32% of solar installation delays trace back to improper hoisting practices? With the solar panel market growing at 8.9% CAGR through 2030 , factories must master safe lifting operations to meet global demand. Let's examine the make-or-break factors in photovoltaic panel handling.
The Hidden Costs of Substandard Hoisting
- 17% increase in panel microfractures from improper sling angles
- $280,000 average insurance claim for dropped solar modules
- 42% longer installation times when using outdated rigging methods
Risk Factor | Industry Incidence Rate | Preventive Measure |
---|---|---|
Structural torsion | 1:15 installations | Dual-axis load monitoring |
Weather damage | 23% of outdoor lifts | Real-time wind sensors |
Human error | 68% of accidents | AI-assisted lift planning |
2024 Hoisting Standards: What's Changed?
The new IEC/TS 62994:2024 introduces three critical updates every factory should implement:
1. Dynamic Load Calculations
Gone are the days of static weight estimates. Modern standards require accounting for:
- Wind shear factors (minimum 1.5x safety margin)
- Panel resonance frequencies
- Multi-axis acceleration forces
"The 2023 Gartner report shows factories using dynamic modeling reduce equipment stress by 37%"
2. Smart Rigging Requirements
All hoisting gear must now include:
- RFID-tagged slings with load history tracking
- Auto-tensioning spreader bars
- Real-time angle sensors (±2° accuracy)
3. Drone-Assisted Verification
Before any lift, factories must conduct:
- Aerial path clearance checks
- 3D obstacle mapping
- Virtual lift simulations
Case Study: How Nevada SolarWorks Cut Installation Time by 40%
By adopting the new ASTM B987-24 standards, this factory achieved:
- 22-minute average panel positioning (vs. 37 minutes previously)
- Zero microfractures in Q1 2024
- 17% reduction in crane fuel costs
Their Golden Hour Protocol
- Pre-lift drone inspection (15 mins)
- AI-powered load distribution analysis (8 mins)
- Augmented reality rigger training (Daily 10-min sessions)
Essential Equipment for Modern Solar Hoisting
Don't get caught using last decade's gear. The 2024 essentials include:
Equipment | Key Feature | Compliance Code |
---|---|---|
Smart Spreader Beams | Auto-balancing up to 5° slope | ISO 17025:2024 |
Vacuum Lifters | 200kPa suction with fail-safes | EN 13155:2023+A1 |
LIDAR Cranes | 5cm positioning accuracy | ASME B30.23-2024 |
Pro Tip: Always verify third-party certification through the Solar Energy Industries Association's (SEIA) Equipment Verification Portal .
Common Mistakes Even Pros Make (And How to Fix Them)
Watch out for these frequent errors observed in 2024 audits:
Mistake 1: Ignoring Panel "Swing Time"
Allowing panels to pendulum for over 8 seconds increases stress fractures by 19% . Solution: Implement dampening systems that stabilize loads within 5 seconds.
Mistake 2: Static Workforce Training
Monthly safety briefings aren't enough. Leading factories now use:
- VR near-miss simulations
- Biometric fatigue monitors
- Real-time load moment indicators
Mistake 3: Overlooking Microclimate Factors
A Phoenix factory recently discovered their afternoon desert winds required different rigging than morning lifts. The fix? Install onsite weather stations updating every 90 seconds.
Future-Proofing Your Hoisting Operations
As we approach Q4 2024, keep these emerging trends on your radar:
- Autonomous cranes using 5G edge computing (pilots show 29% efficiency gains)
- Self-healing composite slings entering beta testing
- Blockchain-based lift certification becoming industry expectation by 2025
Contact Us
Submit a solar project enquiry,Our solar experts will guide you in your solar journey.