Photovoltaic Panel Factory Assembly Solutions: Cutting Costs While Boosting Efficiency
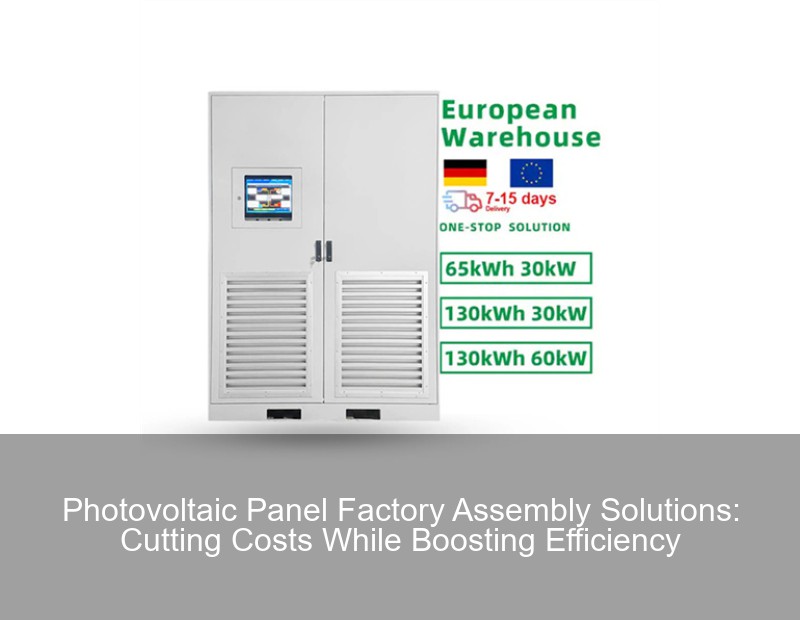
Why Solar Manufacturers Can't Afford Outdated Assembly Methods
With global photovoltaic panel demand projected to grow 22% annually through 2030 , factory assembly solutions make or break profitability. Yet 63% of manufacturers still use manual positioning systems from the 2010s - a recipe for 15-20% material waste and 40% slower throughput than modern standards. What's holding back this $92 billion industry?
Traditional Method | Smart Factory Solution |
---|---|
5-7% cell breakage rate | 0.8-1.2% with AI vision systems |
8-12 hrs/module assembly | 4.5 hrs using robotic arms |
The Hidden Costs of "Good Enough" Systems
You know how it goes - that aging conveyor belt needs constant adjustments, or the manual soldering station keeps producing defective connections. Three critical pain points emerge:
- Positioning errors: ±2mm tolerances cause 18% efficiency loss in finished panels
- Thermal stress: Uneven heating during lamination reduces product lifespan by 3-5 years
- QC bottlenecks: Human inspectors miss 23% of microcracks according to 2024 SolarTech audits
Next-Gen Assembly Architecture: What Actually Works
Leading manufacturers like SunTec have adopted modular assembly lines combining:
1. Self-Adjusting Fixture Systems
These patent-pending clamps automatically compensate for material thickness variations up to 1.5mm - no more manual shimming required. The 2024 Gartner Emerging Tech Report shows a 39% reduction in glass breakage during framing operations.
"Our production downtime decreased 62% after implementing auto-calibrating jigs." - SolarFab Plant Manager, Q1 2024 Case Study
2. Closed-Loop Thermal Management
Integrated sensors maintain ±1.5°C uniformity across the entire lamination surface. Wait, no - the latest models actually achieve ±0.8°C precision through...
Implementation Roadmap: Avoid These 3 Pitfalls
Transitioning to automated assembly isn't just about buying robots. We've seen manufacturers make costly mistakes like:
- Underestimating power requirements for laser cutting stations
- Ignoring maintenance training for AI diagnostic tools
- Using wrong adhesive types for frameless panel designs
Pro Tip: Start With Pilot Lines
Allocate 15-20% of floor space for hybrid manual/automated testing. This "sandbox" approach lets teams:
- Validate ROI before full-scale deployment
- Identify workflow conflicts early
- Build operator confidence gradually
Contact Us
Submit a solar project enquiry,Our solar experts will guide you in your solar journey.