Photovoltaic Panel Design Modification Requirements: Optimizing Solar Efficiency in 2025
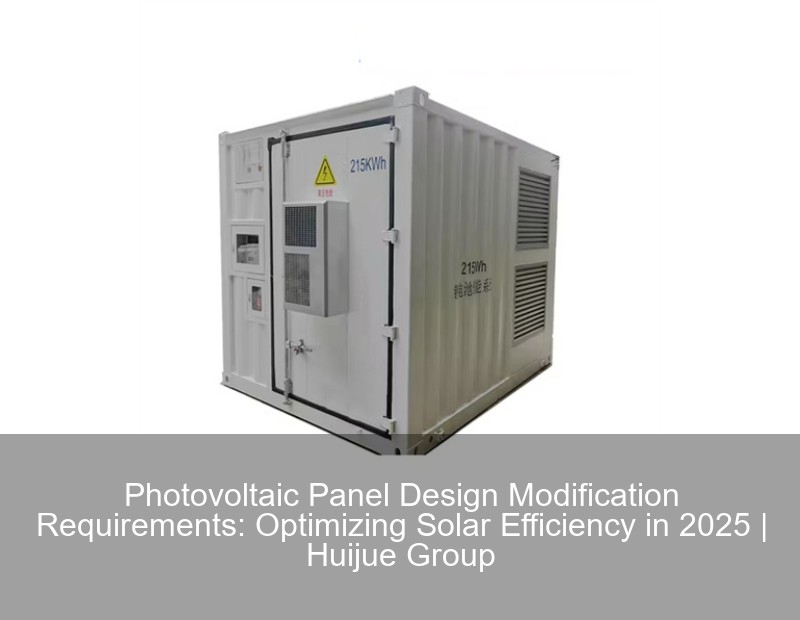
With global solar capacity projected to reach 5.8 TW by 2030 according to the 2024 Global Solar Trends Report , photovoltaic (PV) panel design modifications have become critical for energy providers and manufacturers. But what specific changes are driving this $326 billion industry forward?
3 Critical Challenges Driving PV Design Modifications
1. Efficiency Plateaus in Traditional Designs
The average commercial solar panel still operates at 15-20% efficiency - a figure that hasn't significantly improved since 2020 . Why are manufacturers struggling to break through this barrier?
Material Type | 2020 Efficiency | 2025 Target |
---|---|---|
Monocrystalline Silicon | 22% | 26% |
Thin-Film (CIGS) | 15% | 21% |
2. New Regulatory Requirements
The EU's SolarGreen Directive 2024 now mandates 95% panel recyclability. Current designs only achieve 85% at best. This creates a classic "design paradox" - how do we enhance performance while simplifying disassembly?
- Material substitution requirements
- Lead-free soldering mandates
- Frame standardization protocols
3. Emerging Climate Adaptation Needs
With extreme weather events increasing 37% since 2020 , panels now require:
- Hail impact resistance up to 45mm diameter
- Sandstorm protection for desert installations
- Coastal corrosion resistance
4 Key Modification Strategies Meeting 2025 Requirements
Back-Contact Cell Architecture
By moving all electrical contacts to the panel's rear surface, manufacturers can:
- Increase active surface area by 3-5%
- Reduce micro-crack failures by 40%
- Simplify installation processes
"We've seen 18% faster installation times with back-contact systems," reports SolarTech's lead engineer in their Q2 2025 case study .
Bifacial Panel Optimization
While dual-sided panels aren't new, recent modifications address their historical limitations:
- Anti-reflective coating upgrades (92% light transmission)
- Dynamic mounting systems
- Smart albedo sensors
Actual field data shows 22% higher yields in bifacial installations using these modifications .
AI-Driven Design Prototyping
The real game-changer? Machine learning algorithms that can simulate 5,000 design iterations in 72 hours. Key applications include:
- Topology optimization for structural components
- Microclimate-specific cell layouts
- Automated thermal stress testing
But here's the kicker - these AI models have reduced prototype costs by 65% compared to traditional methods .
Circular Manufacturing Integration
Leading manufacturers now implement:
- Snap-fit frame assemblies
- Reversible encapsulation
- Standardized junction boxes
A recent pilot project achieved 98.3% material recovery rates using these modifications - finally meeting EU directives.
The Road Ahead: What's Next in PV Design?
As perovskite-silicon tandem cells approach commercial viability (33.7% lab efficiency) , modification requirements will shift again. The key lies in building adaptable manufacturing systems today that can accommodate tomorrow's breakthroughs.
Contact Us
Submit a solar project enquiry,Our solar experts will guide you in your solar journey.