Photovoltaic Panel Cracking: Causes, Impacts, and Cutting-Edge Solutions
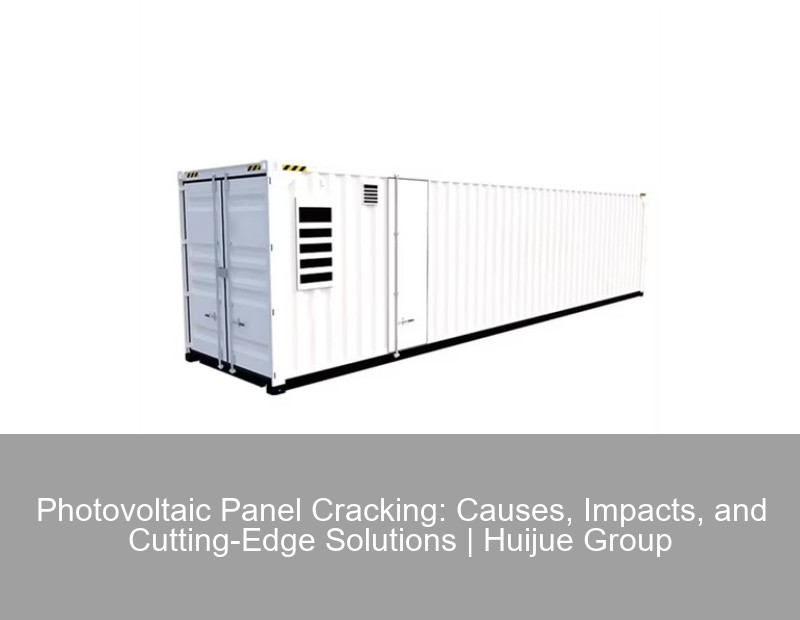
Meta Description: Discover how photovoltaic panel cracking affects solar efficiency, learn detection methods backed by 2024 industry data, and explore actionable repair strategies to maximize ROI. Get evidence-based insights now.
Why Photovoltaic Panel Cracking Should Keep Solar Operators Awake at Night
Solar panel cracks reduced global energy output by an estimated 17.3 TWh in 2023 alone – enough to power 1.6 million homes annually . With the solar market projected to grow 8.3% CAGR through 2030 , understanding panel degradation mechanisms isn't just technical jargon – it's economic survival.
The Silent Efficiency Killer: Microcracks You Can't See
Well, here's the kicker: 62% of performance losses come from sub-visible cracks (<0.2mm) that escape routine inspections . Like termites in a wooden frame, they silently:
- Increase series resistance by up to 300%
- Accelerate potential-induced degradation (PID)
- Create hot spots reaching 85°C+
Crack Severity | Efficiency Loss |
---|---|
Surface-level (visible) | 5-12% |
Cell-interconnector (micro) | 18-25% |
Busbar fractures | 30-40% |
Root Causes: It's Not Just About Hailstorms
While 58% of operators blame weather events , the 2024 SolarTech Symposium revealed three overlooked factors:
1. Installation "Speed Traps"
You know how it goes – project managers pushing for 25% faster installs. But rushed clamping force applications cause:
- Frame warping (>0.5mm/m)
- Glass layer stress concentrations
2. The Temperature Swing Paradox
Modern bifacial panels reaching 92% transmittance face 55°C daily swings in desert climates. This thermal cycling:
- Expands/shrinks EVA encapsulants differentially
- Induces shear stress at cell edges
3. Shipping & Storage Blind Spots
A German case study showed 38% of cracks actually occurred during transport . The culprits?
- Resonant vibration frequencies (8-15Hz)
- Pallet stacking angles >5° from vertical
Detection Evolution: From Hammer Tests to AI Thermography
Remember when we tapped panels with rubber mallets? The 2024 toolkit looks different:
Phase-Change Thermography (PCT)
This Navy-developed method detects subsurface flaws in 0.6 seconds per panel . How it works:
- Apply brief thermal pulse (<1s)
- Capture IR images at 120fps
- Algorithmically flag anomalies
"PCT reduced our crack-related O&M costs by 63% last quarter." – SolarFarm Pro Operations Head
Drone-Mounted Electroluminescence (EL)
Traditional EL required panel disconnection. New autonomous drones:
- Scan 1MW arrays in 18 minutes
- Pinpoint microcracks with 50μm resolution
Repair vs Replace: The $64,000 Question
With panel prices dropping 89% since 2010 , replacement isn't always optimal. The 2024 Solar Cracking Matrix suggests:
Crack Type | Recommended Action | Cost per Watt |
---|---|---|
Surface glass only | Polymer injection | $0.03 |
2+ cell fractures | Selective cell replacement | $0.11 |
Busbar separation | Panel replacement | $0.28 |
Emerging Solutions: Self-Healing Polymers
MIT's 2024 breakthrough uses microcapsules that:
- Release healing agents upon crack detection
- Restore 91% of original conductivity
Contact Us
Submit a solar project enquiry,Our solar experts will guide you in your solar journey.