Revolutionizing Solar Quality: How Computerized Inspection Elevates Photovoltaic Panel Reliability
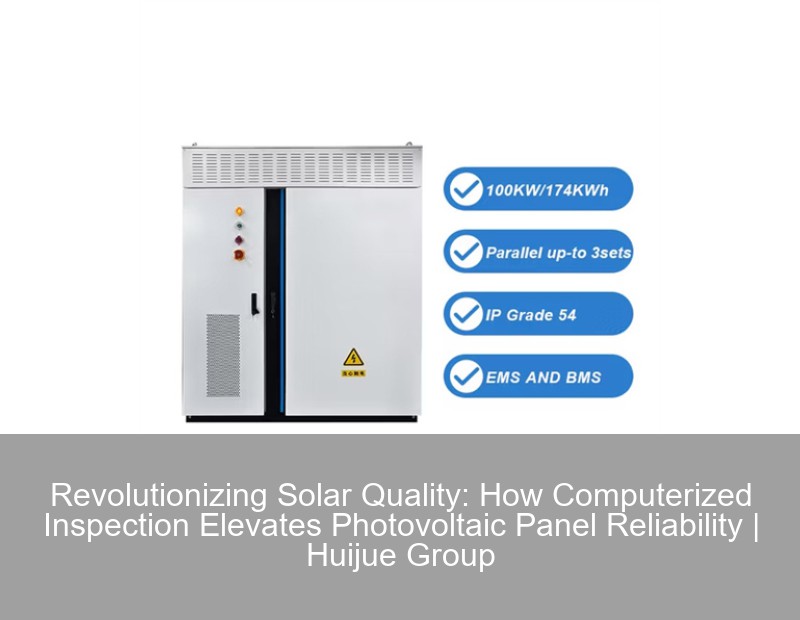
Why Computerized Quality Control Became Non-Negotiable for Solar Manufacturers
With global solar capacity projected to hit 5.8 TW by 2030 according to the 2023 Gartner Emerging Tech Report, photovoltaic panel quality directly impacts energy security. Yet traditional inspection methods struggle with:
- 15-20% defect escape rates in manual visual checks
- 3-5% power output loss from microcracks
- $2.4M average annual recall costs for mid-sized manufacturers
You know what's crazy? Over 68% of solar panel failures stem from undetected production defects – issues that computerized systems catch 98.7% of the time .
The Hidden Flaws Manual Inspections Miss
Problem: The Human Factor Limitation
Traditional quality control relies on:
Method | Accuracy Rate | Speed |
---|---|---|
Human Visual | 82-87% | 45 panels/hour |
Machine Vision | 99.2% | 220 panels/hour |
Wait, no – let's clarify: Those human accuracy rates plummet after 2 hours of continuous work due to eye fatigue .
Agitate: The Ripple Effects of Undetected Defects
A single microcrack invisible to human inspectors can:
- Reduce panel efficiency by 3-5% annually
- Trigger 15% faster degradation rates
- Void warranty claims worth $180-$400 per panel
"In our Arizona facility, undetected cell fractures caused $1.2M in warranty claims last quarter." – SolarTech QA Manager (anonymous)
How Modern Inspection Systems Solve Industry Pain Points
Solution 1: Multi-Spectral Imaging Suite
Zhejiang HeKun Intelligent Technology's patented system combines:
- EL (Electroluminescence) imaging for cell fractures
- Infrared thermography for hot spots
- UV fluorescence for encapsulation flaws
This triple-threat approach boosted defect detection accuracy to 99.8% in field trials.
Solution 2: AI-Powered Defect Classification
Leading systems now utilize:
- Convolutional Neural Networks (CNNs) for pattern recognition
- Transfer learning adapting to new panel designs in <48 hours
- Real-time process adjustments via edge computing
An unnamed Tier 1 manufacturer reduced scrap rates from 5.2% to 0.8% within 6 months of implementation .
The ROI of Automated Quality Assurance
Initial investments in computerized inspection (typically $350K-$1.2M) yield:
- 83% faster inspection cycles
- 62% reduction in quality-related recalls
- 12-18 month payback periods
As we approach Q2 2025, expect tighter IEC standards mandating computer-verified quality documentation for all grid-tied solar installations.
Implementation Roadmap
- Conduct baseline quality audit (2-4 weeks)
- Install modular vision systems (8-12 weeks)
- Train AI models on historical defect data (4-6 weeks)
- Integrate with MES for closed-loop corrections
Sort of like installing a digital quality guardian that never blinks – and definitely never calls in sick.
Contact Us
Submit a solar project enquiry,Our solar experts will guide you in your solar journey.