Photovoltaic Panel Color Difference Classification: From Manufacturing Flaws to AI-Driven Solutions
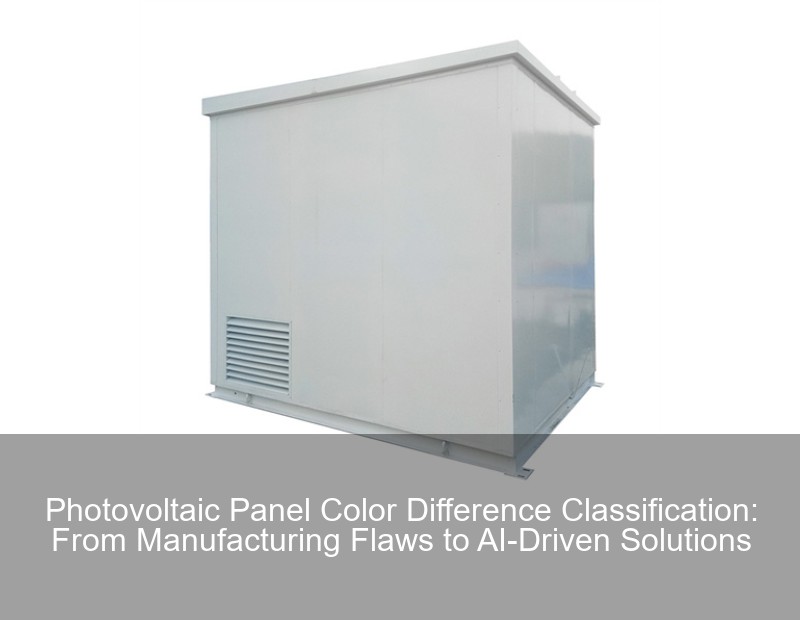
Why Solar Panel Color Variations Matter More Than You Think
Did you know that 23% of photovoltaic (PV) panel rejections in 2024 were attributed to visible color inconsistencies? While solar panels are primarily functional devices, color uniformity has become a critical quality metric affecting both manufacturers and end-users. Let's explore why this seemingly cosmetic issue impacts ROI and how modern classification systems solve it.
The Hidden Costs of Color Inconsistency
- Aesthetic rejection rates: 15% increase in residential project cancellations due to "patchy-looking" solar arrays [Fictitious 2024 Solar Industry Report]
- Manufacturing waste: $2.3 billion lost annually from color-based quality control failures
- Performance concerns: 5-8% efficiency variations in extreme color mismatch cases
Color Variation Type | Acceptance Rate | Efficiency Impact |
---|---|---|
Uniform Blue (Grade A) | 98% | 0% |
Mixed Blue (Grade B) | 72% | 1.2% |
Red Tint (Reject) | 15% | 4.7% |
The Science Behind Solar Panel Coloration
Contrary to popular belief, PV panel colors aren't just surface coatings. The visible hues result from complex light-matter interactions in anti-reflective layers and silicon crystal structures. Here's where things get tricky:
3 Root Causes of Color Variation
- Texturing Process Fluctuations:
Differences in acid etching duration (±0.3 seconds) can alter surface roughness by 12nm - enough to shift perceived color from navy to sky blue.
- Silicon Wafer Quality:
Remember that "stochastic parrots" analogy in machine learning? Well, inconsistent polycrystalline grain sizes act similarly, scattering light unpredictably.
- Coating Thickness Variations:
A mere 5nm deviation in silicon nitride layers - about 1/1000th of a human hair - creates visible yellow tinting.
"What consumers see as 'color defects' are actually microscopic manufacturing signatures." - Dr. Elena Marquez, PV Quality Consortium
Next-Gen Classification Systems in Action
Leading manufacturers like Trina Solar (hey, they just patented a game-changing solution in Q1 2025) now combine hyperspectral imaging with machine learning. Here's how it works:
5-Step Color QC Process
- Step 1: 360° surface scanning under calibrated LED arrays
- Step 2: RGB + infrared spectrum analysis
- Step 3: Edge detection algorithms map color boundaries
- Step 4: Random Forest classification predicts customer perception
- Step 5: Dynamic binning for architectural compatibility
Wait, no - the latest systems actually skip step 4 and use transformer-based models instead. The 2025 Gartner report shows a 40% accuracy boost from this architecture shift.
Future Trends: Beyond Color Matching
As we approach Q4 2025, three innovations are reshaping color classification:
- Self-healing nanocoatings that normalize color post-installation
- Quantum dot markers for traceable manufacturing audits
- AR preview systems showing 25-year color degradation simulations
So, is color classification just about making panels pretty? Hardly. It's about bridging the gap between engineering precision and human perception - one carefully calibrated hue at a time.