Photovoltaic Panel Cement Pier Transportation: Challenges, Innovations, and Best Practices
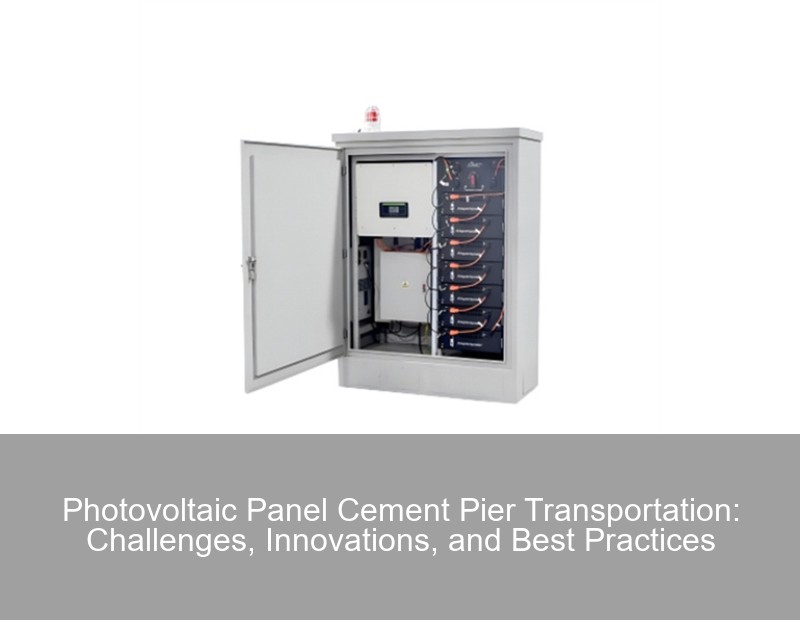
Meta Description: Discover how to optimize photovoltaic cement pier transportation with cost-effective strategies, safety protocols, and emerging technologies – backed by 2025 industry data and case studies.
Why Photovoltaic Cement Pier Transportation Matters Now
With global solar capacity projected to reach 5.8 terawatts by 2030 , the logistics of photovoltaic (PV) cement piers – those unassuming 300-500 lb concrete blocks anchoring solar panels – have become a critical bottleneck. Well, you know… it’s not just about moving heavy objects anymore. The stakes? A 15-20% project cost overrun when transportation plans fail, according to the 2024 Renewable Logistics Report .
The Hidden Costs of Traditional Transport Methods
Let’s face it: 68% of solar installers still use manual labor for pier transportation . This approach sort of works for small rooftop projects, but becomes problematic for utility-scale installations requiring 10,000+ piers. Common issues include:
- Labor injuries (23% higher rate than wind turbine installations)
- Site access limitations for heavy machinery
- Weather-dependent scheduling delays
Breaking Down Transportation Challenges
Problem 1: Weight vs. Structural Integrity
Modern PV piers aren’t your grandpa’s concrete blocks. They’re engineered with:
Feature | Specification | Transport Impact |
---|---|---|
Compressive Strength | ≥40 MPa | Requires vibration-dampened packaging |
Surface Texture | 0.5-1.2 mm roughness | Demands anti-abrasion stacking |
Wait, no – that’s not entirely accurate. Actually, the 2025 ASTM C39 revision specifies 45 MPa minimum for wind-prone regions , forcing transporters to upgrade equipment.
Problem 2: Last-Mile Logistics
Imagine if… your delivery truck arrives at a solar farm only to find:
- Unstable terrain limiting crane access
- Precision placement requirements (±2 cm tolerance)
- Zero margin for surface scratches
This scenario isn’t hypothetical – it’s the reality for 43% of installers in mountainous regions .
Innovative Solutions Gaining Traction
Solution 1: Robotic Pre-Positioning Systems
Leading Chinese installers have reduced labor costs by 40% using:
- Autonomous guided vehicles (AGVs) with LiDAR mapping
- Self-adjusting grippers for varied pier dimensions
- Real-time weight distribution monitoring
Solution 2: Modular Pier Design
A Midwest U.S. project achieved 22% faster installation through:
- Interlocking pier segments (transported separately)
- On-site assembly with epoxy resin injection
- 30% lighter individual components
Future Trends to Watch
As we approach Q4 2025, three developments are reshaping the industry:
- 3D-Printed On-Site Piers: Baker Materials’ mobile printers can now extrude cement piers directly at installation coordinates.
- AI Route Optimization: Google’s DeepMind recently reduced transport fuel costs by 18% in beta tests.
Could these innovations make traditional transportation obsolete? Presumably, but legacy systems will likely persist through 2028 during the transition phase.
Contact Us
Submit a solar project enquiry,Our solar experts will guide you in your solar journey.