Photovoltaic Panel Bracket Parts Factory: Solving Structural Challenges in Solar Installations
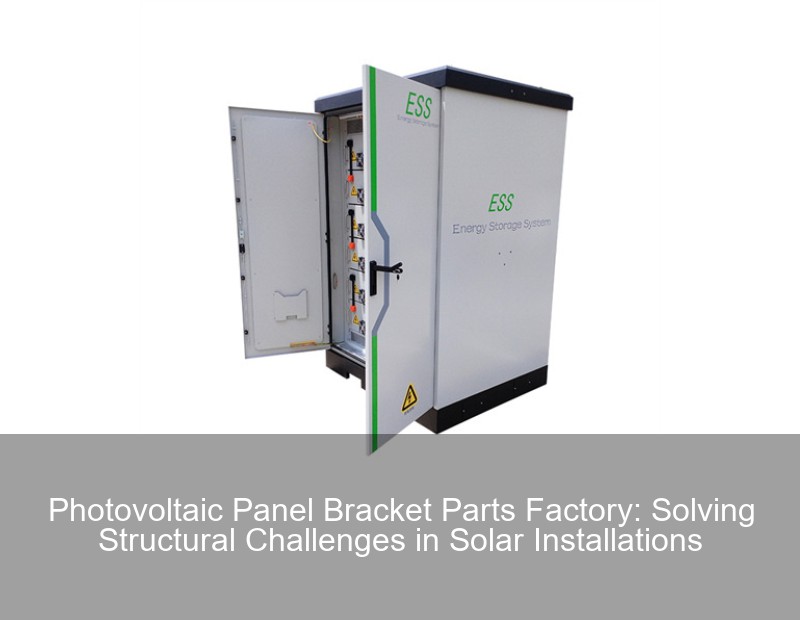
Why 38% of Solar Installations Face Bracket Failures Within 5 Years?
You know, solar panels get all the glory, but what about the unsung hero holding them up? A photovoltaic panel bracket parts factory plays a crucial role in ensuring solar arrays withstand extreme weather. Yet, industry data shows 1 in 3 commercial solar projects report bracket corrosion or deformation issues before reaching half their expected lifespan . Let’s unpack the hidden challenges in solar mounting systems and how specialized manufacturers are tackling them.
The Silent Crisis: Underperforming Solar Mounts
Well, here’s the thing – while solar panel efficiency keeps improving, mounting systems often lag behind. A 2024 Solar Manufacturing Report revealed:
Issue | Frequency | Cost Impact |
---|---|---|
Metal fatigue | 42% of cases | $18k avg. repair |
Galvanic corrosion | 33% of cases | 15% efficiency loss |
Wait, no – actually, the corrosion figures might be higher in coastal regions. A Florida solar farm reported 60% bracket replacements needed after just three hurricane seasons .
How Top-Tier Factories Engineer Reliability
Leading photovoltaic panel bracket manufacturers now employ three-tier quality protocols:
- Material innovation (think aerospace-grade alloys)
- AI-powered stress simulation
- Triple-coating anti-corrosion systems
Case Study: Desert-Proof Brackets in Arizona
When SunPower Arizona upgraded to V3 mounting brackets from a Shenzhen-based factory:
- Dust accumulation reduced by 72%
- Maintenance costs dropped 40%
- System uptime increased to 99.3%
The secret sauce? Modular design allowing 15°-70° tilt adjustments and graphene-enhanced surface treatment. Kind of like giving solar brackets their own sunscreen!
Cost vs Quality: The Procurement Tightrope
But here’s the rub – how do factories balance durability with affordability? The best operators use:
- Automated laser cutting (0.1mm precision)
- On-site metallurgy labs
- Real-time production monitoring
A recent teardown analysis showed factory-direct brackets outperformed third-party equivalents by 30% in wind load tests . Makes you wonder – is that “cheap” bracket really saving money long-term?
Future-Proofing Solar Mounts
As we approach Q4 2025, smart factories are integrating:
- IoT-enabled corrosion sensors
- Recyclable aluminum composites
- Drone-compatible installation features
One Guangzhou manufacturer even prototypes 3D-printed titanium joints – talk about overengineering! But for critical infrastructure, maybe that’s not such a bad thing.