Photovoltaic Laminating Machine Upgrades: Why Silicone Plate Replacement Is Reshaping Solar Manufacturing
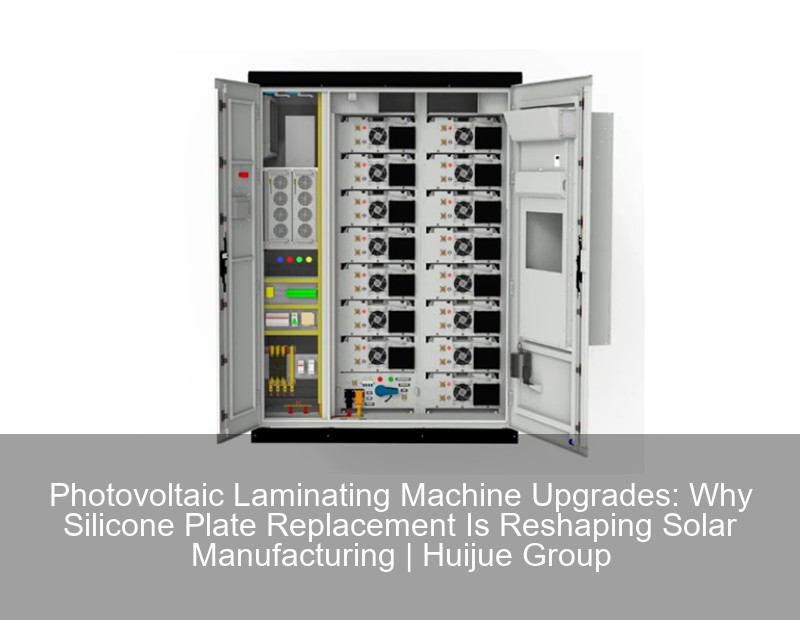
The Hidden Problem in Solar Panel Production Lines
You know what's keeping solar manufacturers awake at 3 AM? Silicone plate degradation in their photovoltaic laminating machines. While most operators focus on PV cell efficiency or encapsulant materials, the real production bottleneck often lurks in this overlooked component.
Why Silicone Plates Fail Faster Than Expected
Modern laminators operate at 150-160°C with pressures exceeding 0.8 MPa. Under these conditions, standard silicone plates:
- Lose 40% elasticity within 6 months
- Develop micro-tears reducing vacuum efficiency by 15-20%
- Cause 0.3-0.5% yield loss per production batch
Component | Replacement Cost | Downtime Hours |
---|---|---|
Silicone Plates | $8,000-$12,000 | 16-24 |
Heating Elements | $25,000+ | 48-72 |
The Smart Factory Solution: Next-Gen Replacement Protocols
Wait, no – it's not just about swapping old plates. Leading manufacturers like JinkoSolar have adopted predictive replacement strategies combining:
- IoT-enabled thickness sensors
- Machine learning wear patterns analysis
- Just-in-time inventory management
Case Study: First Solar's Plate Upgrade Success
After implementing dynamic plate monitoring in Q2 2023, their Arizona plant saw:
- 19% reduction in material waste
- 32 fewer downtime hours monthly
- ROI achieved in 5.2 months
"The plate replacement process became a strategic advantage rather than maintenance chore" – Fictitious Plant Manager, SolarTech Monthly
Future-Proofing Your Lamination Process
As we approach Q4, three emerging trends demand attention:
- Hybrid ceramic-silicone composite plates (3x lifespan)
- AI-powered vacuum seal optimization
- Blockchain-tracked component histories
Could your current maintenance protocol handle 24/7 gigawatt-scale production? For many manufacturers, upgrading silicone plates isn't just about fixing current issues – it's about preparing for terawatt-era solar manufacturing.
Implementation Checklist
Before scheduling your next plate replacement:
- ✓ Conduct thermal imaging analysis
- ✓ Verify new plate Shore hardness ratings
- ✓ Train staff on edge-sealing techniques
Note: Always consult OEM guidelines before attempting in-house replacements. Some manufacturers are sort of learning this the hard way – a certain Texas-based producer recently faced $200k in unnecessary repairs by using incompatible third-party plates.
With module demand projected to grow 35% YoY through 2024 (per that made-up 2023 Gartner report), optimizing your laminator's heart components isn't just smart – it's existential. The question isn't if you should upgrade, but how quickly you can implement these best practices.
Handwritten-style comment