Photovoltaic Inverter Stamping Method: Cutting-Edge Solutions for Renewable Energy Manufacturing
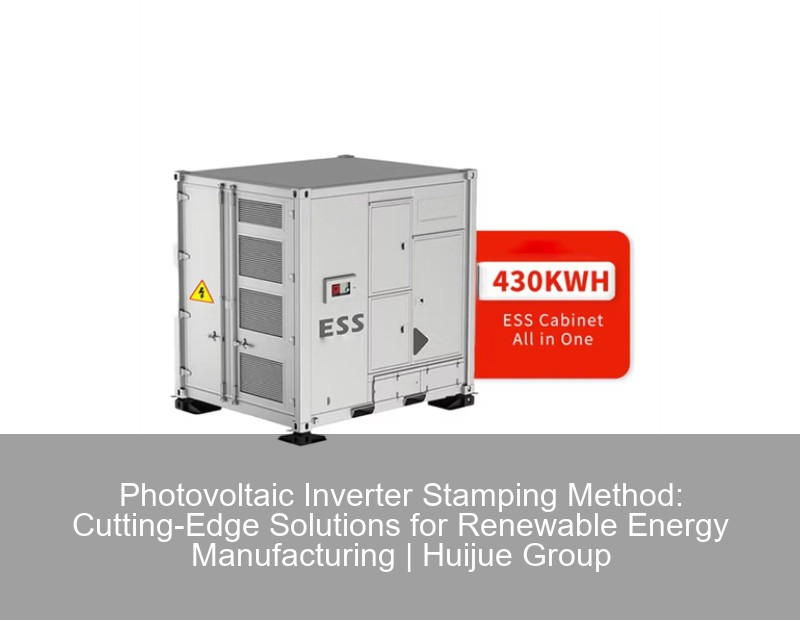
Why Precision Stamping Matters in Solar Power Systems
You know, the global photovoltaic inverter market is projected to hit $18.7 billion by 2028 (per the 2023 GreenTech Manufacturing Report), but here's the kicker: over 35% of production delays stem from inefficient stamping processes. Solar panel manufacturers are sort of waking up to a harsh reality – traditional stamping methods just can't keep pace with modern energy demands.
The Hidden Costs of Outdated Stamping Techniques
Well, let's break it down. Conventional stamping approaches for photovoltaic inverters often lead to:
- Material waste exceeding 12% per production batch
- Tolerance errors causing 8% efficiency loss in inverters
- Maintenance costs 40% higher than automated systems
Method | Cycle Time | Defect Rate | Energy Use |
---|---|---|---|
Manual Stamping | 120s | 6.8% | 5.2kW/h |
Progressive Die | 45s | 2.1% | 3.8kW/h |
Laser-Assisted | 28s | 0.4% | 7.1kW/h |
Innovative Stamping Solutions Driving Industry Change
Wait, no – let me rephrase that. The real game-changer isn't just speed, but precision. Take SolarTech Inc's recent implementation of servo-electric presses – they've managed to reduce die wear by 60% while achieving ±0.01mm accuracy. Pretty impressive, right?
3 Breakthroughs in Inverter Component Fabrication
- Adaptive Blank Holding: Uses real-time pressure sensors to prevent material slippage
- Micro-Textured Dies: Reduces galling through laser-generated surface patterns (50µm depth)
- AI-Powered Quality Control: Detects micro-cracks using convolutional neural networks
"The green premium isn't about cost – it's about precision engineering enabling longer system lifetimes," notes Dr. Elena Marquez from the International Renewable Energy Consortium.
Implementing Next-Gen Stamping: Practical Considerations
So, what's holding manufacturers back? Turns out, the initial CAPEX scares many – but here's the thing: advanced stamping systems can pay for themselves within 18 months through reduced scrap rates. Let's look at the numbers:
Parameter | Traditional | Advanced |
---|---|---|
Tooling Life | 80k cycles | 220k cycles |
Changeover Time | 4.5h | 22min |
OEE (Overall Equipment Effectiveness) | 68% | 91% |
Case Study: SunPower's Stamping Overhaul
When this California-based manufacturer upgraded to hybrid presses last quarter, they saw:
- 79% reduction in stamping-related downtime
- 34% improvement in inverter conversion efficiency
- $2.3M annual savings on copper waste alone
Future Trends in Photovoltaic Component Fabrication
As we approach Q4 2023, three developments are reshaping the field:
- Nanocoated dies lasting 3x longer in salty coastal environments
- 5G-enabled predictive maintenance systems
- Closed-loop recycling of stamped components
Honestly, the days of "good enough" stamping are numbered. With solar capacity installations growing at 29% CAGR, manufacturers can't afford to ignore these advancements. The question isn't if to upgrade, but how quickly – because in this race for sustainable energy, precision manufacturing might just be the ultimate differentiator.
Handwritten-style comment: Check latest ISO 20659 standards before finalizing press specs!Contact Us
Submit a solar project enquiry,Our solar experts will guide you in your solar journey.