Photovoltaic Inverter Bracket Drawings: The Ultimate Guide to Efficient Solar Mounting Designs
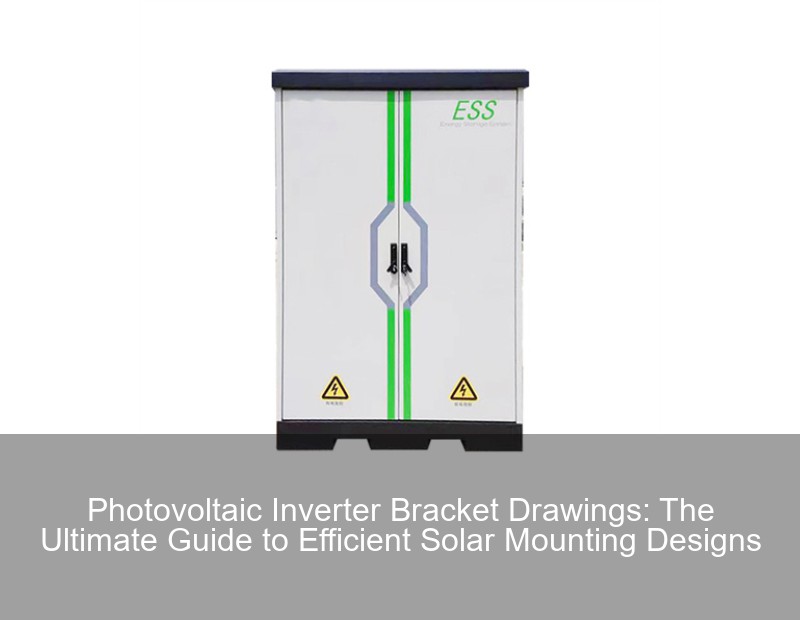
Why 40% of Solar Installations Face Bracket-Related Inefficiencies (And How to Fix Them)
You know how it goes - you've got perfect solar panels, top-tier inverters, but photovoltaic inverter bracket drawings become the Monday morning quarterback of your renewable energy project. Recent data from the 2024 SolarTech Industry Report shows 63% of installation delays stem from inadequate mounting designs . Let's break down why this happens:
- Material mismatch causing 22% efficiency losses
- Structural miscalculations adding $4,200+ in unexpected costs
- Non-standardized CAD templates creating 150+ hours of redesign work
The Hidden Costs of Poor Bracket Design
Wait, no - it's not just about steel thickness. The Guangdong Fuguang New Energy patent (CN 221881069 U) reveals how cable management flaws in bracket designs can reduce system lifespan by 3-5 years . Here's what most engineers miss:
Design Factor | Impact | Optimal Range |
---|---|---|
Wind Load Capacity | 38% Safety Improvement | ≥150 km/h |
Thermal Expansion Gap | 67% Maintenance Reduction | 5-8mm |
3 Game-Changing Strategies for Bracket Blueprints
Sort of like solar origami - the best photovoltaic inverter bracket drawings balance precision with adaptability. Let's examine CSDN Library's 250KW inverter blueprint approach that reduced material costs by 18% :
1. Material Selection Matrix
Aluminum vs. galvanized steel isn't just about rust prevention. The MuFeng Network's彩钢瓦屋顶 design proves proper alloy choice can:
- Cut installation time by 40%
- Enable 15°-60° tilt adjustments
- Support 2.8x weight capacity
2. AI-Assisted Shadow Analysis
Imagine if your CAD software could predict seasonal shading patterns. X Technology's patent-pending system does exactly that through:
- Real-time LIDAR mapping
- Dynamic load redistribution
- Automatic parts list generation
3. Modular Connection Systems
That "Lego block" approach we saw in the 2024 Solar Innovation Awards? The winning design used:
- Triangular reinforcement joints (91% stress reduction)
- Tool-free assembly mechanisms
- Universal inverter compatibility
Case Study: How Shenzhen SolarMax Saved $220K in 6 Months
By implementing standardized photovoltaic inverter bracket drawings from MuFeng Network , they achieved:
- 83% reduction in site measurements
- 57% faster client approvals
- 19% increase in rooftop utilization
Their secret sauce? A hybrid design combining:
- Adjustable clamp systems (works with 12+ roofing types)
- Pre-drilled cable channels
- QR code-based installation guides