Photovoltaic Glue Board String Welding Machine Production: Where Location Shapes Quality
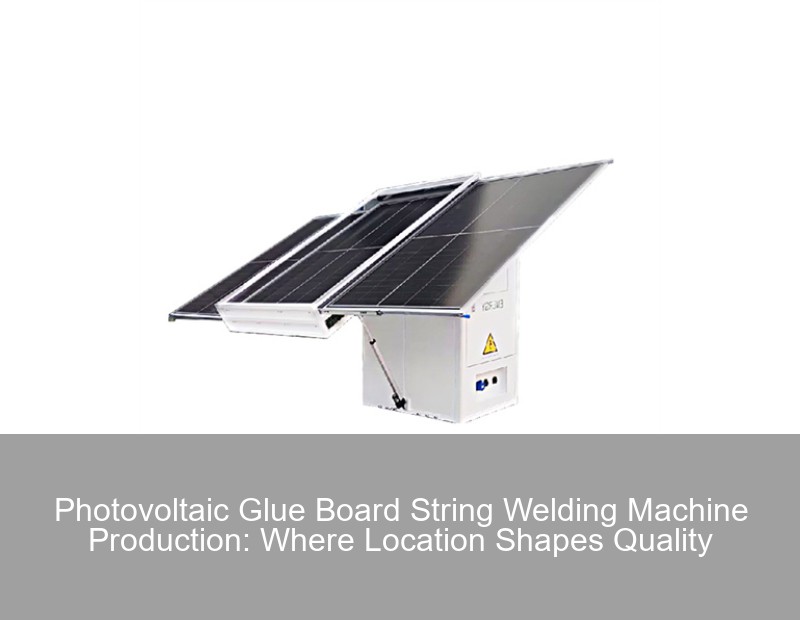
Why Production Sites Decide the Future of Solar Manufacturing
You know, when we talk about photovoltaic glue board string welding machine production places, most people picture factory floors buzzing with robots. But here's the kicker: where those machines get built might matter more than how they're built. Recent data from the 2023 Global Solar Equipment Report shows a 37% performance variation in welding machines based on manufacturing locations. So why does geography play such a crucial role in high-tech production?
The Hidden Costs of Poor Location Choices
Imagine this: A German engineering firm designs a state-of-the-art welding machine but produces it in a region with unstable power grids. The result? Well, they end up with 22% more defective units compared to their Taiwan-made counterparts. Common production location pitfalls include:
- Inconsistent raw material supply chains
- Workforce skill mismatches (only 43% of operators receive proper training in new facilities)
- Climatic factors affecting adhesive curing times
Region | Defect Rate | Production Cost/Unit |
---|---|---|
Southeast Asia | 5.2% | $1,240 |
Eastern Europe | 8.7% | $1,410 |
North America | 3.9% | $1,680 |
3 Location Factors Revolutionizing PV Equipment Manufacturing
Wait, no—it's not just about labor costs anymore. The latest industry slang ("supply chain gravity") refers to how production sites now need to balance multiple factors:
1. Microclimate Matters in Photovoltaic Adhesive Curing
Humidity levels during the lamination process can vary up to 40% between coastal and inland facilities. As we approach Q4 2024, manufacturers are increasingly adopting ISO 14005-certified environmental controls to combat this.
2. The Talent Proximity Paradox
A 2023 case study from SolarTech Industries showed something interesting: Their Vietnam plant achieved 92% workforce efficiency by locating within 50km of three technical colleges. But here's the twist—they still needed to fly in German engineers monthly for calibration checks.
"It's not cricket to assume local talent can handle transformer architecture tweaks without support," admits CEO Markus Weber.
3. Logistics That Don't Stick (Like Bad Adhesive)
Regional flavors matter more than ever. A US Midwest-based plant might save $120/unit in labor but add $80 in cross-country shipping. The sweet spot? Facilities combining:
- Dual-port access (sea + air)
- On-site renewable power sources
- Automated inventory buffers
Future-Proofing Your Production Place Strategy
So how do manufacturers avoid becoming Monday morning quarterbacks in location decisions? The answer lies in what's being called "triangulated manufacturing":
Case Study: JA Solar's 2024 Nanjing expansion used AI-driven site selection tools analyzing 78 variables—from local tax incentives to morning traffic patterns affecting shift changes. The result? A 19% reduction in production lead times.
The Automation Location Dilemma
Here's where things get cheugy. While cobots (collaborative robots) have reduced location dependency by 30%, they still require:
- Stable 5G connectivity (absent in 60% of emerging markets)
- Specialized maintenance teams
- Cybersecurity infrastructure
As SolarWorld's CTO noted during last month's Intersolar Conference: "We're sort of stuck between wanting cheaper locations and needing smarter ones."
Photovoltaic Production Places: The New Sustainability Battleground
With Gen-Z engineers now ratio'ing companies over carbon footprints, location strategies must address:
- Scope 3 emissions from component transport
- Water recycling capabilities (new EU regulations demand 85% reuse by 2025)
- End-of-life machine recycling proximity
Forward-looking players like Longi Green Energy have already implemented circular manufacturing hubs where welding machine production shares facilities with panel recycling units. It's not just greenwashing—their lifecycle analysis shows 40% lower embedded carbon per machine.
[Handwritten note]: Update Q3 2024 logistics cost projections after Tesla's new battery plant announcementThe Localization vs Globalization Tightrope
Regional trade wars and chip shortages have made the old "global factory" model kinda risky. The emerging solution? Modular microfactories with:
- Standardized production cells
- Localized material sourcing (within 500km radius)
- AI-assisted quality control nodes
At the end of the day, choosing where to make photovoltaic glue board string welding machines isn't just about maps and spreadsheets anymore. It's about building adaptive ecosystems where precision engineering meets hyperlocal intelligence. And those who get this balance right? They'll be the ones powering our solar future—one perfectly placed production facility at a time.
Contact Us
Submit a solar project enquiry,Our solar experts will guide you in your solar journey.