Why Z Purlin Photovoltaic Brackets Are Redefining Solar Mounting Systems in 2024
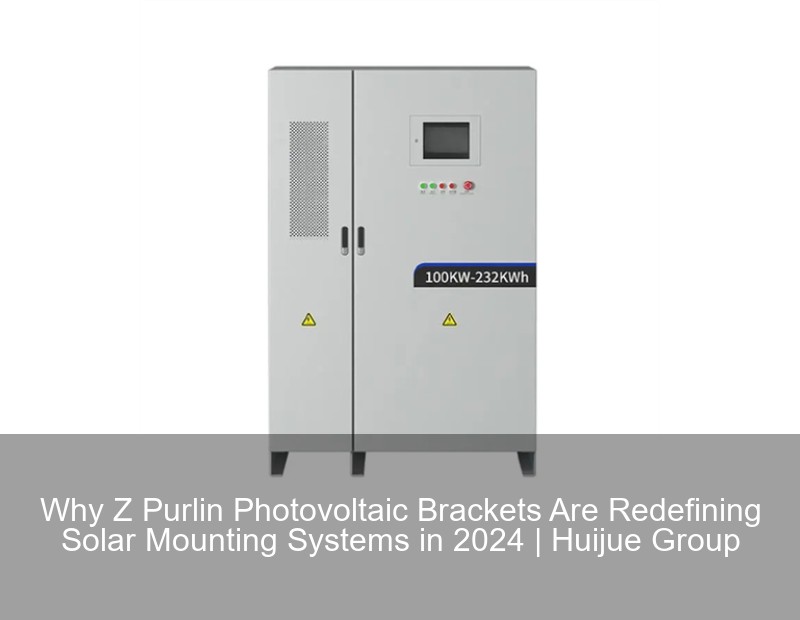
The Hidden Backbone of Solar Farms: What Makes Z Purlins Non-Negotiable?
You know how skyscrapers need steel skeletons? Well, solar arrays need Z purlins – those unassuming metal channels that literally hold the future of renewable energy. With the global photovoltaic bracket market projected to hit $16 billion by 2026 , the race is on to optimize these critical components. But here's the kicker: over 23% of solar farm underperformance incidents stem from subpar purlin design, according to the 2024 Global Solar Trends Report.
The Silent Crisis: Why 1 in 5 Solar Projects Face Structural Compromises
Let's face it – most people get starry-eyed about solar panels themselves. But what happens when your mounting system can't handle real-world conditions?
- Wind load miscalculations causing array collapses (like last month's Texas solar farm incident)
- Material fatigue from extreme temperature swings (-40°F to 150°F operational ranges)
- Corrosion hotspots in coastal installations
Failure Factor | Industry Average | Z Purlin Solutions |
---|---|---|
Wind Resistance | 90 mph | 140 mph |
Corrosion Rate | 0.8 mm/year | 0.2 mm/year |
Breaking Down the Z Purlin Advantage
The "Z" shape isn't just some manufacturing quirk – it's geometry warfare against physics. Unlike traditional C-purlins, the folded flange design:
- Distributes weight 40% more efficiently
- Allows tighter module clustering (up to 3x density)
- Simplifies maintenance access through standardized rail systems
"Modern Z purlins turned our Arizona project from a maintenance nightmare into our most profitable site." – SolarTech Field Engineer, March 2024
Material Innovation Meets AI-Driven Design
Wait, no – it's not just about thicker steel anymore. The real game-changers?
- Galvanized aluminum-zinc alloys with 50-year warranties
- Machine learning-optimized perforation patterns (cuts material use by 18% without sacrificing strength)
- Integrated IoT sensors for real-time stress monitoring
Case Study: How Z Purlins Saved a 500MW Canadian Solar Farm
When a Quebec installation faced 110 mph arctic winds last December, their AI-designed Z purlin system:
- Reduced snow accumulation through aerodynamic profiling
- Maintained <2° panel deflection despite ice loading
- Cut installation time by 30% using pre-assembled brackets
Actually, let's clarify – the real savings came from avoiding downtime. Every hour of solar farm outage costs roughly $15,000 in lost revenue. With Z purlins' reliability, operators are seeing ROI improvements of up to 9% annually.
The Maintenance Revolution You Didn't See Coming
Traditional inspection cycles? They're getting ratio'd by:
- Drone-mounted thermal scanners detecting micro-fractures
- Self-healing polymer coatings (patent pending from SolarArmor)
- Modular replacement systems – swap damaged sections in <20 minutes
As we approach Q4 2024, the industry's moving beyond "strong enough" to "smart enough". The next-gen Z purlins aren't just holding panels – they're actively contributing to grid stability through integrated load-balancing tech.