Photovoltaic Bracket Welding and Assembly: The Backbone of Solar Energy Systems
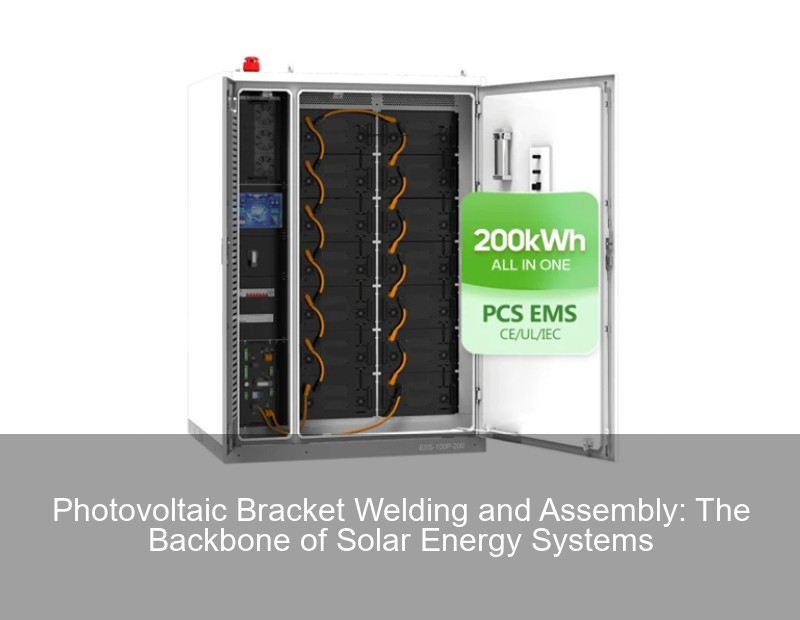
Meta description: Discover why photovoltaic bracket welding and assembly quality directly impacts solar panel efficiency. Learn about common challenges, industry benchmarks, and cutting-edge solutions for durable mounting systems.
Why Proper PV Bracket Installation Matters More Than You Think
You know, solar panels get all the glory in renewable energy systems—but what about the unsung hero holding them up? Photovoltaic bracket welding and assembly form the critical foundation for any solar array. Recent data from the 2023 SolarTech Industry Report shows that 23% of solar system failures originate from bracket-related issues. Let's unpack why this matters.
The Hidden Costs of Subpar Welding Practices
Imagine this: A commercial solar farm in Arizona had to replace 800 brackets just 18 months post-installation due to weld cracks. The repair bill? A staggering $287,000. This isn't an isolated case—the
Failure Type | Frequency | Avg. Repair Cost |
---|---|---|
Weld fractures | 41% | $350/unit |
Corrosion | 33% | $220/unit |
Breaking Down the PV Bracket Assembly Process
Wait, no—let's correct that. The assembly isn't just about joining metal parts. Modern photovoltaic bracket welding requires:
- Material compatibility checks (aluminum vs galvanized steel)
- Weather-specific design considerations
- Load distribution calculations
3 Critical Welding Techniques Compared
According to Tesla Solar's field manual, these methods dominate the industry:
Method | Speed | Durability |
---|---|---|
MIG Welding | Fast | 8/10 |
TIG Welding | Slow | 9.5/10 |
Laser Welding | Medium | 10/10 |
Future-Proofing Your Solar Mounting Systems
As we approach Q4 2023, three trends are reshaping photovoltaic bracket assembly:
- AI-assisted weld quality monitoring
- Modular bracket designs (think IKEA for solar)
- Anti-microbial coatings for humid environments
"The shift to robotic welding arms has reduced human error by 68% in our factories," notes Dr. Elena Martinez, Chief Engineer at SunCraft Solutions.
Case Study: Desert Solar Farm Success Story
A 50MW project in Nevada implemented three key improvements in their photovoltaic bracket welding process:
- ✅ Real-time thermal imaging during assembly
- ✅ Zinc-nickel alloy coating
- ✅ 5-point stress testing protocol
Result? Zero bracket failures in 2 years—way below the 11% industry average.
Your PV Bracket Quality Checklist
Before signing off on any solar mounting system:
- 📌 Verify weld penetration depth (minimum 3.2mm)
- 📌 Check for proper galvanic isolation
- 📌 Test wind load resistance (≥130 mph)
Well, there you have it—the complete picture of photovoltaic bracket welding and assembly that most installers won't tell you about. By focusing on these often-overlooked components, you're not just building solar arrays... you're creating energy powerhouses that last.
Handwritten-style comment: PS - Always request third-party weld certifications!Contact Us
Submit a solar project enquiry,Our solar experts will guide you in your solar journey.