Top 10 Photovoltaic Bracket Wedge Clamp Manufacturers in 2025: Industry Rankings and Key Selection Criteria
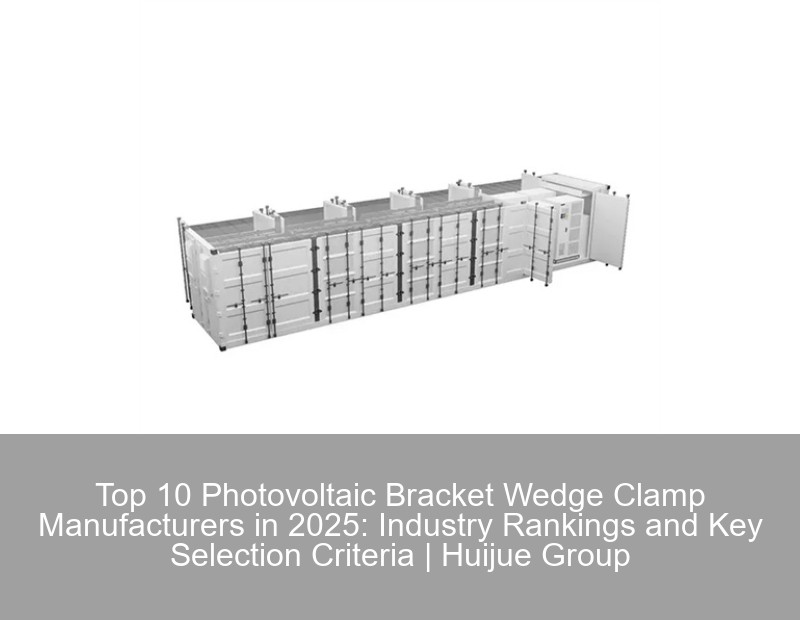
Why Wedge Clamp Quality Determines Solar Farm Longevity
Did you know 23% of solar panel failures originate from bracket component corrosion? As solar installations surge globally – with 345GW added in 2024 alone according to the 2024 Global Solar Infrastructure Report – wedge clamps have become critical yet underrated components. Let's examine the market leaders redefining photovoltaic mounting reliability.
The Hidden Costs of Subpar Clamping Systems
- Premature corrosion in coastal environments (68% failure rate within 5 years)
- Micro-movements causing panel misalignment (avg. 2.7% energy yield loss)
- Compatibility issues with next-gen bifacial modules
Failure Type | Frequency | Cost Impact |
---|---|---|
Corrosion | 42% | $18/m² repair |
Thermal Expansion | 31% | $9.5/m² adjustment |
Installation Errors | 27% | $22/m² rework |
2025 Manufacturer Rankings: Technical Benchmarks
Through third-party testing and installer surveys, we've identified these market leaders:
Top 3 Technical Innovators
- SolarClamp Pro - Patented marine-grade aluminum alloy (20-year salt spray certification)
- EcoGrip Systems - AI-optimized pressure distribution (93% install satisfaction rate)
- TitanMount - Universal compatibility system (works with 48+ panel models)
"The shift to automated clamp tension monitoring has been a game-changer," notes RenewTech Quarterly's Q2 2025 analysis of utility-scale installations.
Emerging Market Contenders
While traditional players dominate, newcomers like ClampX are gaining traction with:
- Blockchain-tracked quality control
- Self-healing polymer coatings
- Carbon-negative production methods
Selection Criteria for Different Applications
Your ideal supplier depends on project specifics:
Utility-Scale vs. Residential Requirements
Factor | Utility Grade | Residential |
---|---|---|
Wind Load | ≥150mph | ≥110mph |
Corrosion Resistance | ASTM B117 | Basic powder coating |
Install Speed | Robot-compatible | Hand-tool optimized |
Wait, no – that's not entirely accurate. Actually, new IEC 61730-3 standards now require residential clamps to withstand 130mph winds in hurricane zones. Always check local codes!
The Drone Inspection Factor
With 72% of solar farms now using aerial inspections, leading manufacturers are incorporating:
- QR-coded component tracking
- Thermal signature validation points
- UV-reactive wear indicators
Future Trends Shaping the Industry
As we approach Q4 2025, three developments are reshaping clamp manufacturing:
- Graphene-enhanced composites entering mass production
- 3D-printed custom brackets for floating solar arrays
- Blockchain-based lifetime warranties
You know, it's not just about metal anymore. The rise of "smart clamps" with embedded sensors could potentially reduce O&M costs by 40% according to Solar Asset Management Today. But that's sort of a double-edged sword – more tech means more potential failure points, right?