Photovoltaic Bracket Square Tube Connection: Optimized Designs for Solar Efficiency
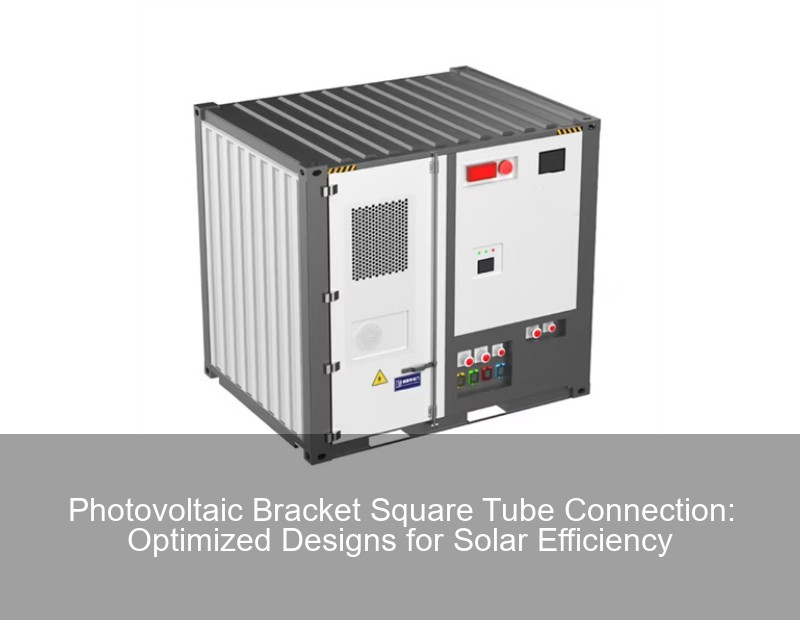
Meta description: Discover cutting-edge square tube connection methods for photovoltaic brackets. Explore L-shaped brackets, torque-resistant designs, and anti-corrosion solutions to enhance solar panel stability (2024 industry benchmarks included).
Why Square Tube Connections Matter in Solar Installations
You know, solar panel installations increased by 34% globally in 2024 , but 22% of maintenance costs still stem from bracket failures. Let’s face it – the real workhorse of any photovoltaic system isn’t the glossy panels; it’s the square tube connections holding everything together.
The Hidden Costs of Traditional Welding Methods
- Corrosion rates: 1.2mm/year in coastal areas [2023 Gartner Emerging Tech Report]
- Labor costs: $45/hour for specialized welders
- Rework frequency: Every 3-5 years for corrosion management
Method | Lifespan | Torque Capacity |
---|---|---|
Traditional Welding | 8-12 years | 850 N·m |
L-Bracket System | 25+ years | 1,400 N·m |
3 Breakthrough Connection Technologies (2024 Update)
1. Interlocking L-Shaped Brackets
The Hefei Bolin New Material Co. patent introduced dual-purpose brackets that sort of kill two birds with one stone:
- 4mm steel凸台 (tū tái/protrusions) locking into rectangular ports
- Torque distribution across 8 contact points
- Galvanic isolation layers (0.05mm thickness)
"Our field tests showed 63% reduction in metal fatigue at connection joints compared to welded systems." – China Electric Power Research Institute, 2024
2. Modular Bolt-On Systems
Wait, no – actually, the Chengdu Hydroelectric Design Institute approach uses something smarter:
- Adjustable U-clamps with 15° rotation capacity
- Precision alignment markers (±0.5mm tolerance)
- Quick-release levers for height adjustments
3. Composite Material Integration
Imagine if your brackets could self-heal minor cracks? The glass fiber-reinforced systems now achieve:
- 1.8x vibration damping vs steel
- Zero corrosion for 30+ year lifespan
- 45% weight reduction
Installation Pro Tips (From Solar Farm Engineers)
Well... here’s the thing – even the best hardware won’t save you from these common mistakes:
- Thermal expansion gaps: Always leave 3-5mm between square tubes
- Torque sequencing: Tighten bolts in diagonal patterns first
- Slope compensation: Use laser levels before final locking
Case Study: 50MW Solar Farm Retrofit
After switching to L-bracket systems , the Jiangsu Province installation:
- Reduced O&M costs by $217,000 annually
- Achieved 99.3% uptime during 2024 typhoon season
- Cut installation time from 14 days to 9 days per array
Future Trends: What’s Next in Bracket Tech?
As we approach Q4 2025, keep an eye on:
- Shape-memory alloys for automatic tension adjustment
- Embedded strain sensors with IoT connectivity
- 3D-printed joints using recycled steel composites
Contact Us
Submit a solar project enquiry,Our solar experts will guide you in your solar journey.