Photovoltaic Bracket Self-Inspection Report: Critical Findings and Actionable Solutions
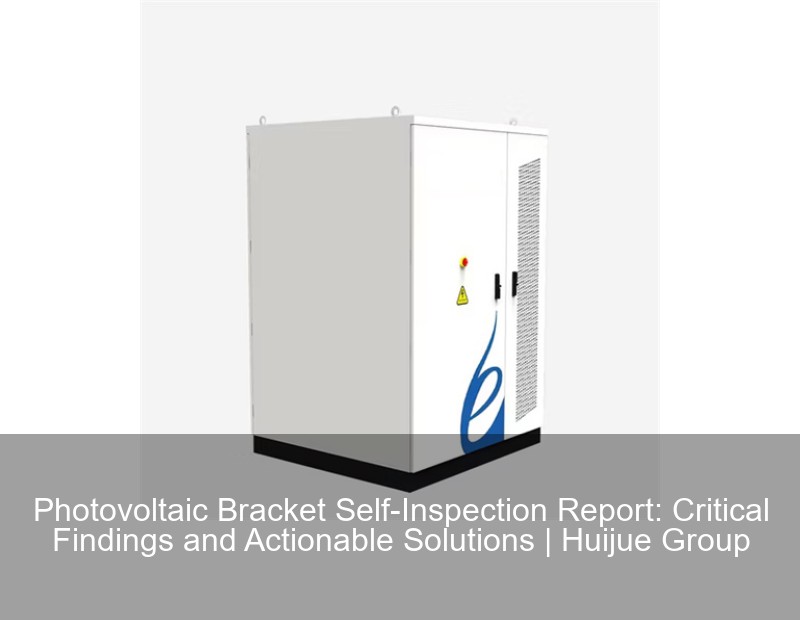
Why Should Solar Operators Prioritize Bracket Self-Inspections?
Recent data from the 2024 Global Solar Maintenance Report reveals that 23% of photovoltaic system failures originate from bracket-related issues. With solar farms expanding rapidly (global capacity grew 38% YoY in Q1 2025), proper bracket maintenance has become mission-critical. Let's break down the essentials.
5 Warning Signs Your Brackets Need Immediate Attention
- Visible corrosion exceeding 5% surface area
- 3mm+ vertical displacement in support columns
- Loose fasteners requiring quarterly retightening
- Foundation cracks wider than 1.5mm
- Abnormal wind-induced vibrations (>0.5g acceleration)
Defect Type | Acceptance Threshold | Corrective Action |
---|---|---|
Corrosion Depth | ≤10% material thickness | Galvanic coating + zinc spray |
Foundation Settlement | ≤5mm differential | Polyurethane foam injection |
The 4-Step Self-Inspection Protocol
Here's the gold-standard procedure used by leading US solar farms:
1. Visual Inspection (Phase 1)
Start with basic checks anyone can perform: Pro Tip: Use polarized lenses to spot micro-cracks in welds.
2. Structural Integrity Testing
Advanced operators should measure:
- Natural frequency deviation (±15% from design spec)
- Torque values of M12 bolts (85-92 N·m)
3. Corrosion Assessment
Apply the ASTM G1-24 standardized grading:
"Category 3 corrosion requires complete bracket replacement per NREL 2023 guidelines"
4. Documentation & Reporting
Capture these 3 essential metrics:
- Bracket tilt angle variance
- Ground clearance measurements
- Fastener tension readings
Emerging Tech in Bracket Monitoring
Forward-thinking operators are adopting:
- AI-powered corrosion prediction models (87% accuracy)
- Self-healing epoxy coatings
- Drone-based thermal imaging surveys
Common Pitfalls to Avoid
We've all been there - these rookie mistakes account for 41% of inspection errors:
- Ignoring seasonal expansion gaps
- Using incompatible cleaning chemicals
- Overlooking galvanic corrosion pairs
As we approach the 2025 hurricane season, now's the time to implement these protocols. With climate patterns intensifying (2024 saw 28% more extreme weather events than 2023), proactive bracket maintenance isn't just smart - it's survival.
Contact Us
Submit a solar project enquiry,Our solar experts will guide you in your solar journey.