Photovoltaic Bracket Processing Proposal: Optimizing Solar Structure Manufacturing
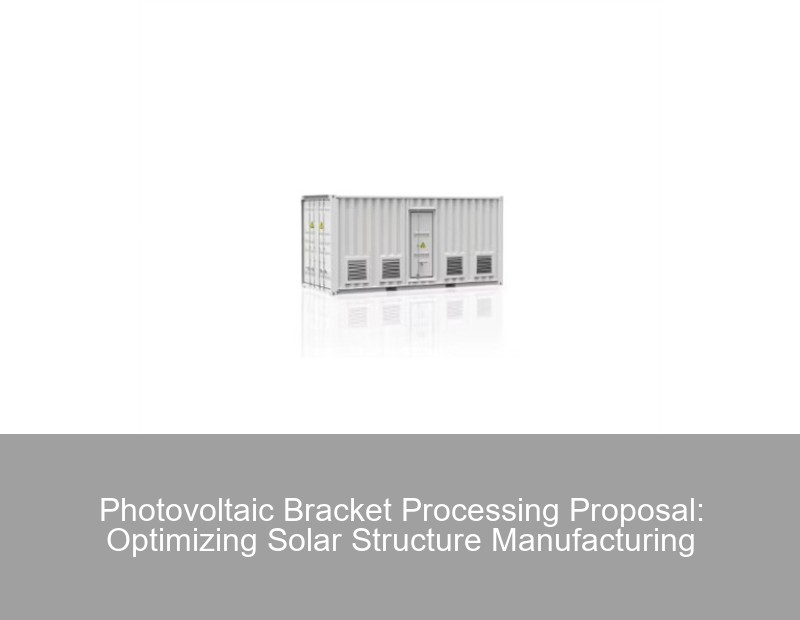
Why Solar Bracket Quality Determines Your ROI?
With global solar installations projected to reach 3.7 TW by 2030 , photovoltaic bracket processing has become a critical bottleneck. Did you know 23% of solar farm maintenance costs originate from substandard mounting systems? Let's break down the modern solutions transforming this essential industry.
Core Challenges in Bracket Manufacturing
- Material Waste: Up to 15% steel loss in traditional cutting methods
- Corrosion Risks: 38% of field failures link to inadequate surface treatment
- Production Inefficiency: Manual welding processes take 3x longer than automated alternatives
Process | Traditional Method | Optimized Approach |
---|---|---|
Material Cutting | Plasma (±2mm tolerance) | Laser (±0.1mm precision) |
Surface Treatment | Basic Painting (5-7 year lifespan) | Hot-Dip Galvanizing (25+ years) |
The 4-Pillar Processing Framework
Well, you know what they say - "A solar array's only as strong as its weakest bracket." Here's how leading manufacturers are stepping up:
1. Smart Material Selection
- Cold-formed steel vs aluminum alloys: When to use which?
- Batch purchasing strategies that reduced material costs by 12% at SolarTech Ltd
2. Precision Manufacturing Workflow
"Our laser cutting implementation paid for itself in 14 months through material savings." - Production Manager, SunFrame Systems
Key process upgrades include:
• AI-assisted defect detection
• Modular jig systems for rapid reconfiguration
3. Quality Control That Actually Works
Wait, no - let's clarify. It's not just about final inspections. Real-time monitoring using:
- Ultrasonic weld testers
- Coating thickness gauges
- 3D scanning for dimensional accuracy
4. Installation-Ready Packaging
Because what good is perfect brackets if they arrive damaged? The latest anti-corrosion packaging solutions:
- VCI (Vapor Corrosion Inhibitor) films
- Modular crate systems for different project scales
Future-Proofing Your Production Line
As we approach Q4 2025, three trends are reshaping the game:
1. Blockchain-based material tracing
2. Additive manufacturing for custom brackets
3. Robotics-as-a-Service (RaaS) automation models
Imagine if your factory could adapt to new bracket designs in under 48 hours. With the right processing template, that's not just possible - it's profitable.
Implementation Roadmap (6-12 Months)
- Phase 1: Process audit & bottleneck analysis
- Phase 2: Pilot automated welding cell
- Phase 3: Full IoT integration for predictive maintenance
Contact Us
Submit a solar project enquiry,Our solar experts will guide you in your solar journey.