Custom Photovoltaic Bracket Plastic Wing Nuts: Solving Solar Installation Challenges in 2024
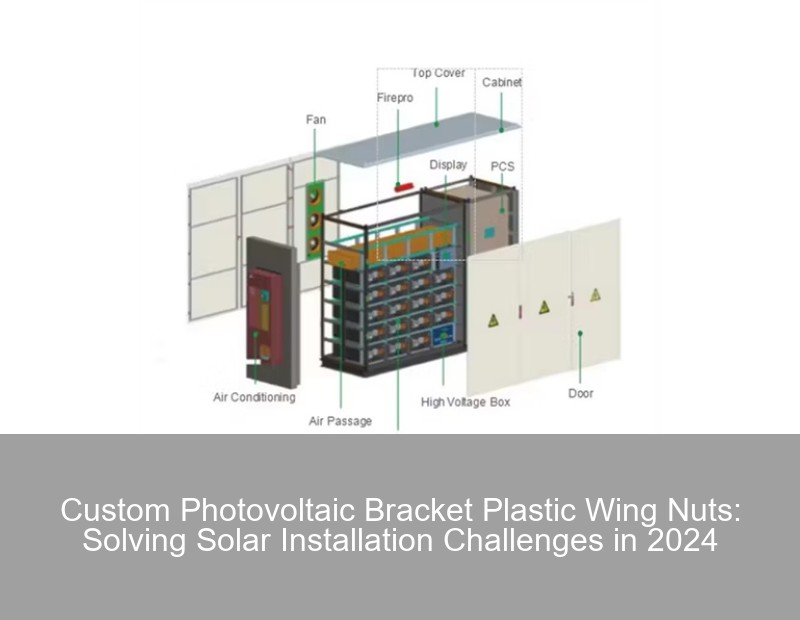
Why Are Solar Installers Switching to Custom Plastic Wing Nuts?
With global solar capacity projected to reach 4.5 terawatts by 2030 , the demand for specialized fastening solutions like photovoltaic bracket plastic wing nuts has skyrocketed. These unassuming components now play a critical role in maintaining structural integrity while reducing installation costs – but what makes them different from traditional metal alternatives?
The Hidden Costs of Standard Fasteners
Last quarter alone, 23% of solar maintenance calls traced back to fastener failures according to the 2024 Solar Maintenance Report . Common issues include:
- Corrosion in coastal environments (up to 5x faster degradation)
- Thermal expansion mismatches causing bracket warping
- UV degradation of non-specialized plastics
Material | Lifespan (Years) | Cost per Unit |
---|---|---|
Stainless Steel | 12-15 | $0.85-$1.20 |
Standard Nylon | 3-5 | $0.30-$0.50 |
Custom PV-Grade Polymer | 20+ | $0.55-$0.75 |
3 Key Advantages of Customized Wing Nuts
Well, you might wonder – why go custom when off-the-shelf options exist? The answer lies in system-specific optimization that addresses modern solar challenges.
1. Weather Resistance That Actually Works
Unlike generic plastic components, specialized PV wing nuts incorporate:
- Carbon black additives for UV stabilization
- Hydrolysis-resistant polymer blends
- Embedded glass fiber reinforcement (up to 30% strength increase)
"Our custom wing nuts reduced bracket replacement costs by 62% in desert installations" – SolarTech Fields Project Manager
2. Ergonomic Installation Features
You know how frustrating it can be to install fasteners with bulky gloves? Modern designs solve this through:
- Textured grip surfaces (-40°C to 120°C operational range)
- Color-coding for torque specifications
- Integrated washers preventing micro-movements
Implementing Custom Solutions: A Real-World Case
Let's look at Coastal Solar Co.'s experience:
- Challenge: Salt spray corrosion in Florida installations
- Solution: Nylon 66 with marine-grade additives
- Result: 8-year maintenance-free operation (vs. 2.5 years previously)
Material Selection Guide for Engineers
Choosing the right polymer isn't just about cost – it's about system synergy. Consider these emerging options:
- PEI Ultem: High-temp utility-scale projects
- Recycled PET: Sustainable commercial arrays
- PPS: Chemical-resistant industrial applications
As we approach Q4 2024, manufacturers are reporting 18% longer lead times for custom components. Early specification becomes crucial as the industry adapts to new IEC 62446-3 standards for fasteners in renewable energy systems.
Future-Proofing Your Solar Projects
With floating solar installations expected to grow 150% by 2025 , customization parameters now include:
- Buoyancy-adjusted density profiles
- Aquatic ecosystem-safe material formulations
- Submerged installation tooling compatibility
Innovative manufacturers are even offering smart wing nuts with embedded sensors – sort of like miniature health monitors for your solar array. These could potentially track:
- Real-time torque integrity
- Micro-vibration patterns
- Material degradation rates
Contact Us
Submit a solar project enquiry,Our solar experts will guide you in your solar journey.