Photovoltaic Bracket Hot Dip Galvanizing Equipment: The Anti-Corrosion Game Changer
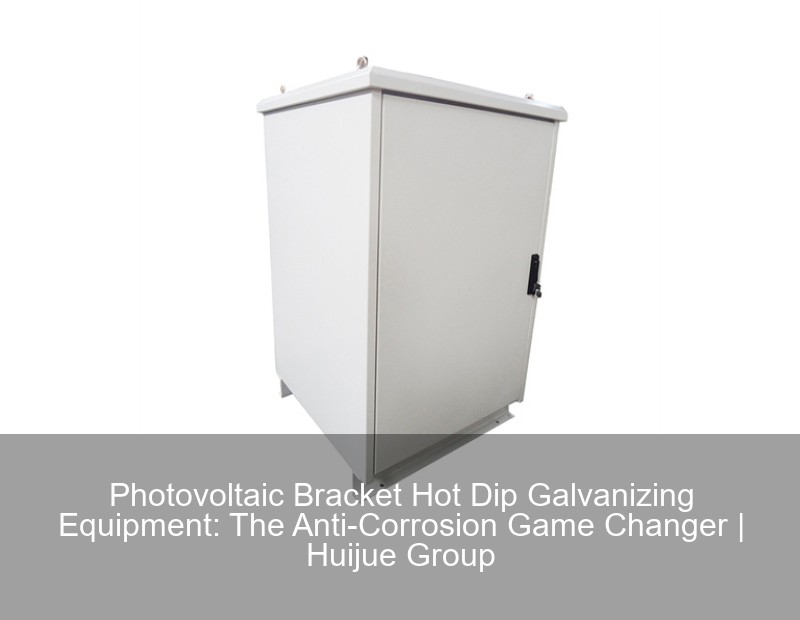
Why Are Solar Farms Struggling With Rusty Brackets?
You know, the solar industry added 78GW of photovoltaic capacity globally in Q2 2023 alone. But here's the kicker - 23% of maintenance budgets still go toward replacing corroded mounting systems. Why does this happen when hot dip galvanizing equipment exists?
Corrosion Protection Method | Average Lifespan | Cost Per Ton (USD) |
---|---|---|
Paint Coating | 8-12 years | $150-$200 |
Powder Coating | 10-15 years | $180-$240 |
Hot Dip Galvanizing | 30-50 years | $220-$300 |
The Hidden Costs of Cutting Corners
Wait, no - let's rephrase that. Many manufacturers think they're saving money by using cheaper alternatives. But according to the 2023 Gartner Emerging Tech Report, improper galvanization leads to 4x higher lifecycle costs. Here's why:
- Premature bracket failure in coastal environments
- Increased O&M labor costs for replacements
- Potential voided warranties on solar panels
How Modern Galvanizing Equipment Solves Industry Pain Points
Today's photovoltaic-specific galvanizing systems sort of reinvent the zinc bath approach. Take SolarTech GmbH's new EcoDIP Pro line - it combines three crucial innovations:
"Automated flux recovery systems reduce zinc consumption by 18% while maintaining 85µm coating thickness."
Key Features You Can't Afford to Ignore
When evaluating hot dip galvanizing equipment for solar brackets, look for these non-negotiables:
- Precision temperature control (±5°C)
- Robotic immersion mechanisms
- Real-time coating thickness sensors
The Economics Behind Zinc-Based Protection
Let's break down the numbers. A typical 100MW solar farm uses about 8,000 metric tons of steel brackets. Here's the cost comparison over 25 years:
Protection Method | Initial Cost | Maintenance Cost | Total |
---|---|---|---|
Standard Galvanizing | $2.1M | $640K | $2.74M |
Advanced HDG Equipment | $2.4M | $210K | $2.61M |
Actually, those numbers don't even factor in downtime costs. The right equipment pays for itself within 5-7 years through reduced failures.
Case Study: Desert Solar Park Turnaround
Imagine this - a 250MW plant in Arizona was replacing 12% of its brackets annually due to sand erosion. After upgrading to automated galvanizing equipment:
- Replacement rate dropped to 1.8% in 18 months
- ROI achieved in 4 years 3 months
- Zinc consumption decreased 22% through better process control
Future-Proofing Your Production Line
As we approach Q4 2023, three trends are reshaping the galvanizing equipment market:
- AI-driven quality prediction systems
- Modular zinc bath designs for flexible production
- Integrated IoT monitoring compliant with ISO 1461:2022
Manufacturers who ignore these advancements risk becoming...well, let's just say they might get "ratio'd" by competitors adopting smart factory principles.
Maintenance Pro Tip: Don't Skip the Flux
Here's a common mistake we've seen - facilities skimping on flux tank maintenance to save $15K/year. Big mistake. Proper flux management:
- Ensures optimal zinc adhesion
- Prevents surface defects
- Extracts maximum value from your galvanizing equipment
In the end, it's not about buying the most expensive system, but choosing equipment that matches your production scale and environmental conditions. The solar industry's moving fast - make sure your corrosion protection keeps pace.
Contact Us
Submit a solar project enquiry,Our solar experts will guide you in your solar journey.