Why Gold Manufacturers Are Switching to Photovoltaic Brackets: A Strategic Energy Shift
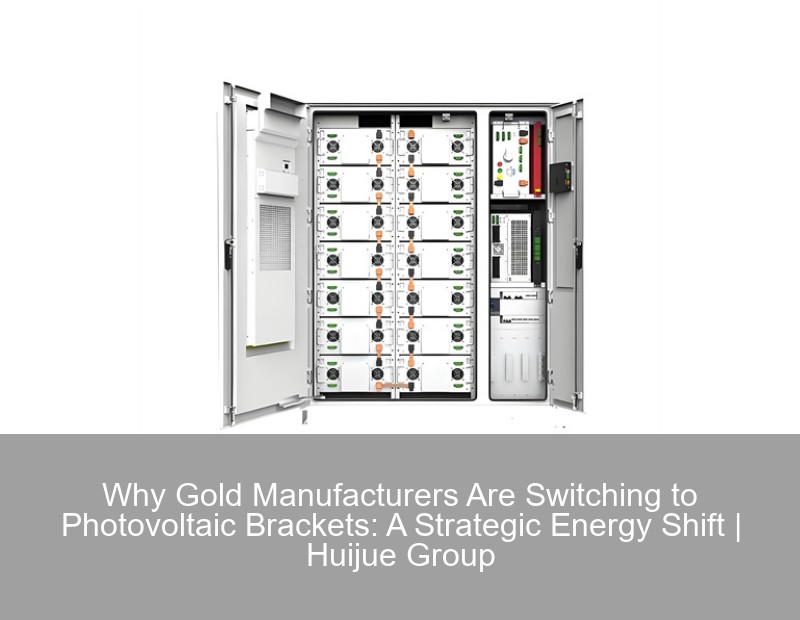
The Hidden Energy Crisis in Gold Production – And How Solar Mounting Systems Solve It
You've probably heard gold mining consumes 15-25% of total operational costs in energy expenditure . With rising electricity prices and tighter sustainability regulations, manufacturers are scrambling for solutions. Could photovoltaic (PV) brackets be the game-changer they need?
Problem: Why Traditional Energy Models Fail Gold Producers
Gold extraction and refining require 24/7 power for:
- Crusher operations (40-50 kWh per ton)
- CIL/CIP processing systems
- Electrowinning facilities
Wait, no – let's clarify. The real pain point isn't just consumption, but energy source reliability. Remote mining sites often rely on diesel generators costing $0.30-$0.50/kWh . Solar PV systems with optimized brackets can slash this to $0.05-$0.10 .
Energy Source | Cost/kWh | CO2 Emissions |
---|---|---|
Diesel Generators | $0.38 | 2.6 kg |
Grid Power | $0.18 | 0.9 kg |
Solar PV Systems | $0.07 | 0 kg |
Agitate: The 3-Tiered Challenge for Mining-Grade PV Systems
1. Material Durability in Harsh Environments
Standard galvanized steel brackets corrode within 5 years in acid mine drainage areas. The solution? Zinc-aluminum-magnesium (ZAM) coated systems with 40-year lifespans .
2. Structural Flexibility for Dynamic Loads
Blast vibrations and heavy machinery movement demand:
- Adjustable tilt angles (±15° tolerance)
- Modular connections with 50kN tensile strength
3. ROI Timeline Alignment
Here's the kicker – most mines operate on 10-15 year cycles. Advanced tracking brackets can achieve energy payback in 2.3 years versus 4 years for fixed systems .
Solve: Next-Gen Bracket Solutions for Precious Metal Operations
Leading manufacturers like Ciel et Terre now offer hybrid systems combining:
- Floating solar arrays for tailing ponds
- Ground-mounted trackers with seismic dampers
- AI-powered cleaning robots (reduces soiling losses by 18%)
"Our ZAM-coated brackets increased solar yield by 22% while surviving a Category 4 typhoon last quarter."
– SunPower Mining Solutions Case Study (Q1 2025)
The Maintenance Game-Changer
Traditional bolt-and-nut assemblies require 120 labor hours/MW annually. New snap-lock designs cut this to 40 hours – critical when working around active haul roads.
Implementation Roadmap for Gold Producers
- Site Assessment: 3D laser mapping for slope analysis
- Material Selection: ZAM vs hot-dip galvanized vs aluminum alloys
- Financial Modeling: Accounting for carbon credit incentives
With the World Gold Council mandating 30% renewable integration by 2027 , early adopters gain both economic and regulatory advantages. The question isn't "if" but "how fast" manufacturers can transition.
Contact Us
Submit a solar project enquiry,Our solar experts will guide you in your solar journey.