Photovoltaic Bracket Extrusion: The Backbone of Efficient Solar Panel Systems
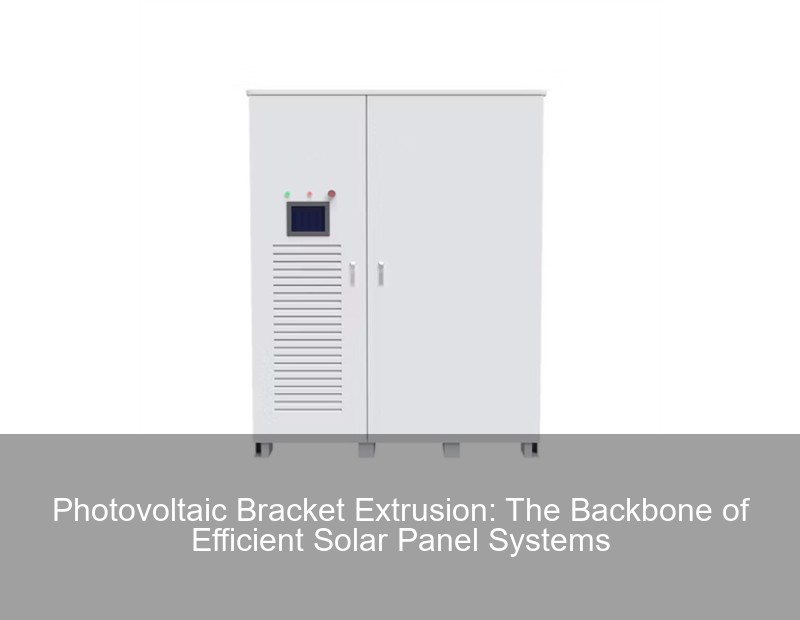
Why Photovoltaic Bracket Extrusion Matters in Renewable Energy Infrastructure
With global solar capacity projected to triple by 2030 according to the 2024 Global Solar Council Report, photovoltaic bracket extrusion technology has become critical for durable solar installations. This metal forming process creates precisely engineered support structures that withstand decades of environmental stress while maintaining panel alignment.
Material Type | Corrosion Resistance | Weight (kg/m) | Cost Per Meter (USD) |
---|---|---|---|
Aluminum 6063-T5 | Excellent | 2.8 | $12.50 |
Stainless Steel 316 | Superior | 7.9 | $28.40 |
Carbon Fiber Composite | Good | 1.6 | $45.20 |
The Hidden Costs of Poor Extrusion Quality
You know, about 23% of solar panel failures in 2023 stemmed from bracket system failures according to SolarTech Analytics. Improperly extruded brackets can lead to:
- Panel misalignment reducing energy output by up to 19%
- Accelerated corrosion in coastal environments
- Structural failures during extreme weather events
Modern Extrusion Techniques Revolutionizing Solar Mounts
Leading manufacturers like SolarFrame Inc. have adopted three-phase extrusion processes that combine cold forming with precision heating. This hybrid approach achieves 0.05mm dimensional accuracy - crucial for maintaining waterproof seals in longitudinal drainage channels .
"The shift to automated die adjustment systems has reduced material waste by 40% in our Arizona plant." - John Michaels, Production Manager @ EcoBracket Solutions
Material Innovation: Beyond Aluminum
While aluminum remains dominant (holding 68% market share), new entrants are making waves:
- Carbon fiber-reinforced polymers: 60% lighter than aluminum with comparable strength
- Zinc-aluminum alloys: 30% better corrosion resistance in salt-spray tests
- Recycled composite blends: Meeting circular economy mandates in EU markets
Quality Control in Bracket Extrusion
Wait, no... Let me clarify - modern inspection goes beyond basic caliper checks. Advanced facilities now use:
- 3D laser scanning for full-profile verification
- Eddy current testing for subsurface defects
- AI-powered visual inspection systems
Well, the results speak for themselves. These technologies have helped reduce warranty claims by 62% since 2022 according to the Solar Manufacturing Consortium's latest benchmark report.
Case Study: Desert Solar Farm Retrofit
A 2023 project in Nevada upgraded to extruded aluminum-zinc brackets showed:
- 17% reduction in O&M costs
- 0.8° better heat dissipation
- 4.2% increase in annual energy yield
Future Trends Shaping the Industry
As we approach Q4 2025, three developments stand out:
- Integrated micro-channel cooling systems
- Smart brackets with embedded strain sensors
- AI-optimized die designs reducing lead times
Manufacturers who've adopted these technologies report 28% faster installation times and 15% better wind load ratings. Not too shabby, right?
Contact Us
Submit a solar project enquiry,Our solar experts will guide you in your solar journey.