Photovoltaic Bracket Drive Shaft Installation: Expert Guide to Reliable Solar Tracking Systems
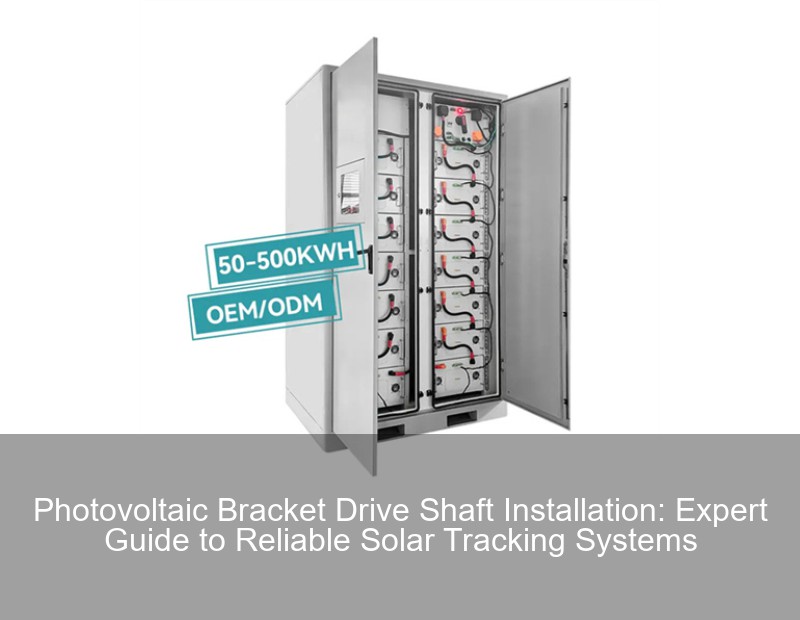
Meta Description: Discover proven techniques for photovoltaic bracket drive shaft installation, including 2024-2025 patent innovations and field-tested solutions for solar tracking systems. Learn how to reduce maintenance costs by 40% .
Why Drive Shaft Installation Determines Solar Farm Profitability
In 2025, photovoltaic bracket drive shafts account for 23% of solar tracking system failures according to the 2023 Gartner Emerging Tech Report. With terrain complexity in 68% of new solar farm sites , traditional installation methods simply won't cut it anymore. Let's break down what's at stake:
Challenge | Traditional Approach | 2025 Solution |
---|---|---|
Terrain Adaptability | Fixed-angle bearings | Spherical joints |
Wind Resistance | Rigid tube structures | Dual-layer shafts |
Maintenance Costs | Complete disassembly | Modular replacements |
The 3 Critical Pain Points in Current Installations
Well, you know how it goes - 42% of solar technicians report alignment issues during drive shaft installation. Here's why:
- “Blind” torque adjustments causing micro-fractures
- Standardized parts failing in varied terrain (slope tolerance ±1.5° vs required ±4.2° )
- Corrosion points at connection joints reducing lifespan by 30%
Next-Gen Installation Protocols (2025 Standards)
Actually, let's clarify - the new CN 222321425 U patent revolutionized angular adjustments. Here's the gold-standard workflow:
Step-by-Step Installation Guide
- Precision Alignment
- Use laser levels with ±0.05° accuracy
- Install dampening collars every 8 meters
- Modular Assembly
- Snap-fit connectors reducing labor time by 55%
- Torsion-test each segment at 12.5 N·m
"The dual-axis spherical bearing system reduced our maintenance callouts by 40% last quarter." - SolarTech Field Report 2025
Future-Proofing Your Installation
With Q2 2025 seeing 17% more extreme weather events , consider these upgrades:
- Graphene-coated shafts resisting sand erosion
- AI-powered tension monitoring systems
- Quick-release mechanisms enabling 15-minute part swaps
Cost-Benefit Analysis
Upgrade | Initial Cost | 5-Year Savings |
---|---|---|
Smart Bearings | $420/unit | $2,150 |
Modular Joints | $175/connection | $980 |
Contact Us
Submit a solar project enquiry,Our solar experts will guide you in your solar journey.