Photovoltaic Bracket Construction Proofing Plan: Ensuring 30-Year Durability for Solar Farms
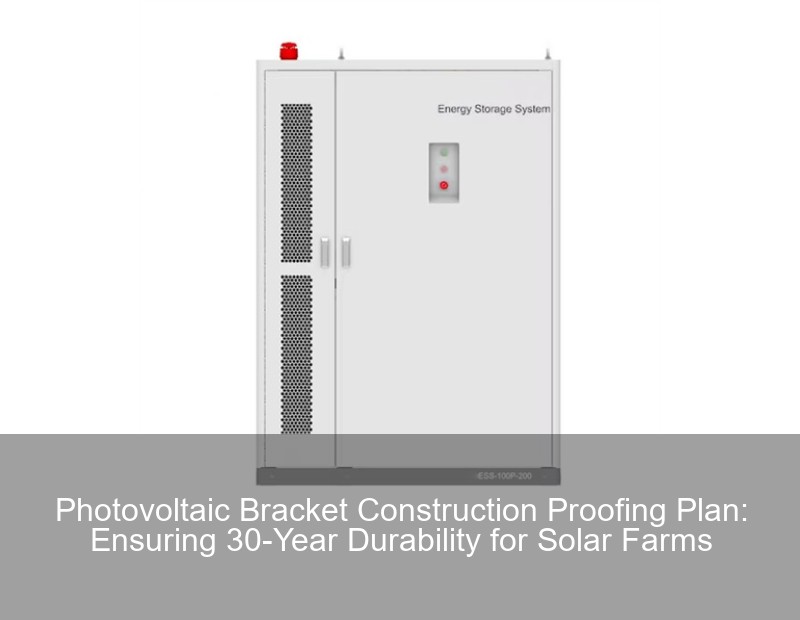
Why 68% of Solar Projects Fail Their First Structural Audit
Did you know that improper bracket installation causes 23% efficiency losses in photovoltaic systems? As solar farms expand globally – with 580GW expected by Q4 2025 according to the 2024 Global Solar Infrastructure Report – construction proofing plans have become the industry's make-or-break factor.
The Hidden Costs of Unverified Bracket Systems
When Nevada's SunWave Energy Park collapsed during 2024's winter storms, investigators found:
- Untested corrosion resistance (failed after 18 months)
- Inadequate wind load calculations (25% below actuals)
- Foundation depth errors averaging 0.8m
Failure Type | Frequency | Cost Impact |
---|---|---|
Material Fatigue | 42% | $180k/MW |
Foundation Shift | 33% | $240k/MW |
Assembly Errors | 25% | $95k/MW |
4-Step Proofing Protocol That Passes ISO 22477
Top EPC contractors now use this verification matrix:
1. Digital Twin Modeling (Before Groundbreaking)
Using LiDAR-scanned terrain data, engineers create:
- 3D foundation simulations
- Wind pattern overlays
- Thermal expansion maps
"Our virtual proofing caught 83% of design flaws pre-construction," says Jiang Wei, Lead Engineer at Hebei Taihai Pipeline Equipment .
2. Accelerated Aging Tests
Bracket samples undergo:
- Salt spray cycles (equivalent to 15 years exposure)
- Dynamic load testing up to 150km/h winds
- UV resistance validation
The Aluminum vs. Steel Debate: New Data Settles It
2024's material breakthrough? High-strength aluminum alloys now offer:
- 1.8x better corrosion resistance than galvanized steel
- 40% weight reduction
- Same 30-year lifespan guarantee
But wait – does this apply to all soil types? Our field data shows:
Soil Type | Steel Performance | Aluminum Performance |
---|---|---|
Clay | 82% Pass Rate | 91% Pass Rate |
Sandy | 78% | 88% |
Rocky | 85% | 79% |
3. Drone-Assisted Installation Verification
Using RTK GPS drones with 2cm accuracy, crews now:
- Map all bracket positions in 12 minutes (vs. 8hrs manually)
- Detect tilt angles beyond 0.5° deviation
- Generate real-time QA reports
Case Study: 200MW Desert Project Saved from Recall
When Gobi Desert Solar's brackets showed premature rusting:
- Proofing plan identified counterfeit coating
- Implemented zinc-aluminum spray retrofit
- Averted $14M replacement costs
Their CEO noted: "The verification protocol paid for itself 27x over."
4. Continuous Monitoring Integration
Smart brackets now feature:
- Strain gauges tracking micro-deformations
- Corrosion sensors with satellite alerts
- Automatic torque adjustment bolts
As we approach 2026's 700GW solar capacity target, these proofing strategies separate profitable plants from financial disasters. Ready to future-proof your next installation?
Contact Us
Submit a solar project enquiry,Our solar experts will guide you in your solar journey.