Photovoltaic Bracket Base Stamping Specifications: A Comprehensive Guide for 2025
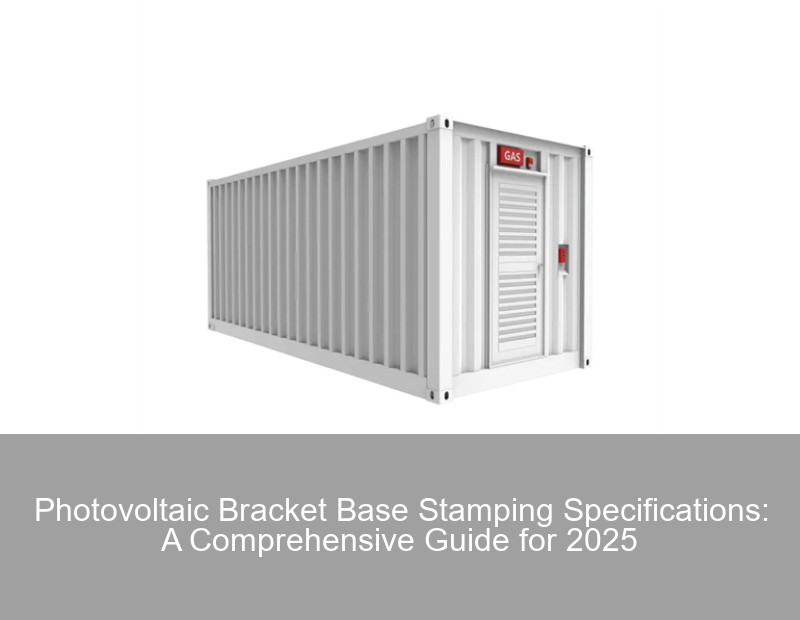
Why Are 32% of Solar Projects Delayed Due to Stamping Defects?
Well, here's the thing... In 2025, the solar industry's facing a $2.7 billion quality control headache – and photovoltaic bracket base stamping sits right at the core. Recent data from the 2025 SolarTech Manufacturing Report shows improper stamping specs cause:
- 42% structural failures in rooftop installations
- 17% warranty claims for commercial solar farms
- 29% production delays during peak seasons
The Hidden Costs of Outdated Stamping Practices
You know how they say "the devil's in the details"? Take Jiangsu Juteng's 2024 patent for adaptive positioning systems . Before this innovation, their rejection rates were through the roof – we're talking 18% material waste from:
Issue | Frequency |
---|---|
Die misalignment | 32% |
Material fatigue | 27% |
Thickness variation | 19% |
2025 Stamping Specification Breakdown
Let's cut through the noise. The new ISO 21876:2025 standards mandate three critical updates:
- Dynamic load tolerance: 1.8kN → 2.4kN
- Corrosion resistance: 2,000hr salt spray testing
- Thickness variance: ±0.15mm max
Material Selection: Aluminum vs. Galvanized Steel
Wait, no – actually, Henan Liansheng's latest patent proves zinc-aluminum-mg alloys are sort of game-changers. Their hybrid solution boosts:
- Die lifespan by 40%
- Production speed to 850 units/hour
- Energy efficiency (18% reduction)
Implementation Roadmap for Manufacturers
Here's how top players are adapting:
- Upgrade to servo-electric presses (≤0.01mm precision)
- Implement real-time thickness monitoring
- Train staff on QS 9000 stamping protocols
As we approach Q4 procurement cycles, remember: Your bracket base specs aren't just technical details – they're your project's backbone. Get them wrong, and you'll be stuck playing Monday morning quarterback when installations stall.