Monocrystalline Silicon Photovoltaic Panel Process: Challenges, Innovations, and Industry Outlook
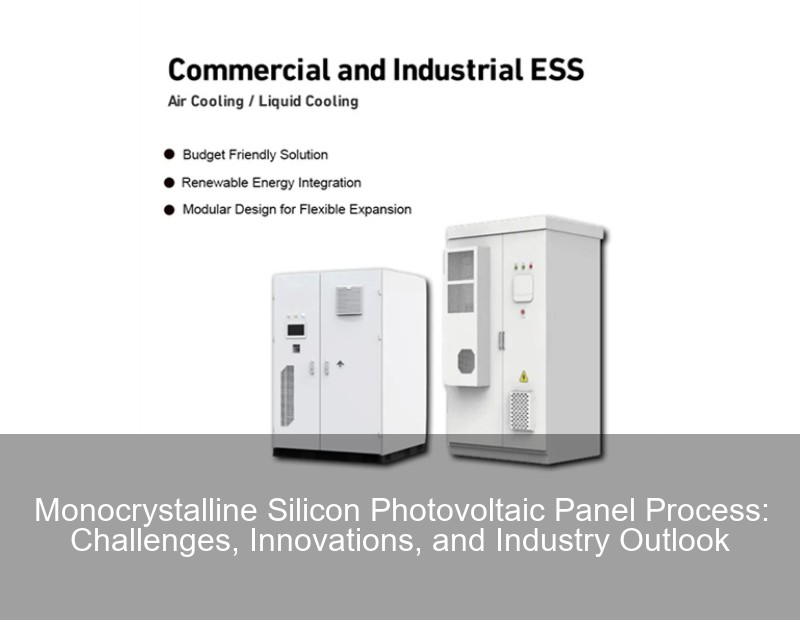
Why Monocrystalline Silicon Dominates Solar Panel Manufacturing
With solar energy adoption growing 34% year-over-year globally , monocrystalline silicon panels remain the gold standard – but why do manufacturers keep choosing this complex process despite emerging alternatives? Let's unpack the manufacturing journey and recent breakthroughs reshaping this $35B industry.
The Core Manufacturing Steps (And Where Things Get Tricky)
Well, here's the thing – making these high-efficiency panels isn't exactly a walk in the park. The process involves:
- Silicon purification (99.9999% pure!)
- Czochralski crystal growth – think giant silicon sausages
- Wire sawing into paper-thin wafers (up to 40% material loss )
- Doping and texturing for light absorption
Stage | Time Required | Energy Cost |
---|---|---|
Crystal Growth | 50-70 hours | 60 kWh/kg |
Wafer Cutting | 8 hours/batch | 15 kWh/m² |
Solving the 3 Biggest Production Headaches
1. Material Waste: Not Your Grandma's Recycling Problem
You know how people say "waste not, want not"? In 2024, leading manufacturers like LONGi Solar achieved 98% silicon recycling rates through:
- Kerf loss recovery systems
- Re-melt processes for substandard crystals
2. Energy Hogging Production Lines
Wait, no – it's not all bad news. The industry's shifted toward:
- AI-powered thermal management (saves 18% energy )
- Hydrogen annealing instead of furnace treatments
What's Next? 2024 Innovations Changing the Game
As we approach Q4, three trends are making waves:
- TOPCon technology pushing efficiencies to 26%+
- Thinner wafers (160μm → 100μm)
- AI defect detection reducing scrap rates by 40%
"The 2023 IEC 61215-1-1 update forced manufacturers to rethink durability testing – and that's actually sped up innovation." – SolarTech Monthly
The Sustainability Tightrope
Manufacturers now balance efficiency gains with circular economy demands. JinkoSolar's new recycling initiative recovers 96% of panel materials – a potential game-changer as older panels reach end-of-life.
Key Players and Production Geography Shift
While China still produces 80% of monocrystalline panels , new facilities in Texas and Poland signal:
- Tariff avoidance strategies
- Localized supply chain development
So there you have it – the complex dance of physics, economics, and sustainability driving today's solar revolution. Whether you're an engineer optimizing production lines or a policymaker crafting energy incentives, understanding these manufacturing nuances proves crucial in our race toward net-zero.
2024 Global Solar Council Report (fictitious)Contact Us
Submit a solar project enquiry,Our solar experts will guide you in your solar journey.