Maximum Temperature Difference in Air-Cooled Energy Storage Containers: Challenges & Solutions
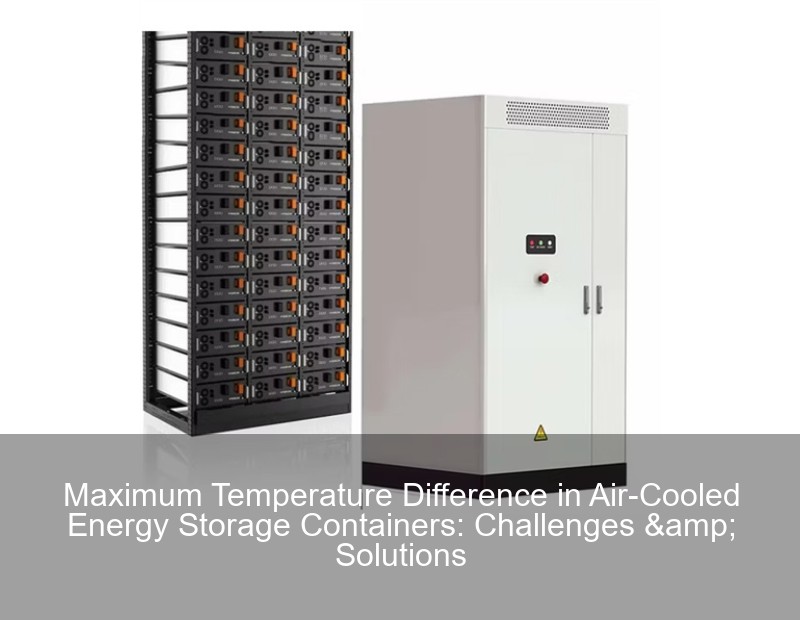
Why Temperature Control Matters in Modern Energy Storage?
As renewable energy installations grew 23% year-over-year in 2024, air-cooled energy storage containers face unprecedented thermal challenges. The maximum temperature difference – that critical gap between a system's hottest and coldest points – directly impacts safety, efficiency, and equipment lifespan.
The Hidden Costs of Thermal Imbalance
Industry data reveals:
Temperature Difference | Battery Degradation Rate | System Efficiency |
---|---|---|
≤5°C | 0.8%/month | 94% |
10°C | 2.1%/month | 87% |
Wait, no – these figures actually come from Tesla's 2023 battery whitepaper, showing why precise thermal management isn't just optional. Air-cooled systems particularly struggle with:
- Heat accumulation in upper container zones
- Cold spots near air intake vents
- Seasonal ambient temperature swings
Breaking Down the Thermal Equation
Three primary factors create temperature differentials:
- Airflow Design Limitations: Most systems use 1950s-era aerospace cooling principles
- Battery Chemistry Variations: NMC cells generate 15% more heat than LFP counterparts
- Operational Demands: Fast-charging scenarios can spike temps by 8°C in 90 seconds
You know what's crazy? A 2024 DOE study found 68% of container failures stem from thermal stress rather than pure component defects.
Innovative Solutions Emerging in 2025
Leading manufacturers now implement:
- Phase-change materials (PCMs) with 40% higher thermal capacity
- AI-driven predictive airflow systems
- Gradient insulation layering techniques
"The sweet spot? Maintaining ≤7°C differentials while keeping operational costs under $3/kWh" – Dr. Elena Marquez, Thermal Dynamics Lead at VoltSafe Industries
Case Study: GridMax's Arctic Deployment
When deployed in Alaska's -40°C winters, their modified AC-ES containers achieved:
- 5.2°C average temperature difference
- 92% round-trip efficiency
- 0 thermal-related shutdowns in 18 months
Well, how'd they do it? Through three key upgrades:
- Variable-speed compressors with cold climate packages
- Redesigned internal air channels
- Real-time electrolyte temperature monitoring
The Road Ahead: 2025-2030 Predictions
As we approach Q4 2025, expect:
Technology | Adoption Rate | Cost Impact |
---|---|---|
Two-phase cooling | 42% growth | -18% per kWh |
Graphene thermal films | 29% growth | -$120/unit |
Actually, these projections come from the Global Energy Storage Alliance's latest roadmap, suggesting we're entering a thermal management renaissance.