Why Material Innovation is Critical for Next-Gen Wind Turbine Blades
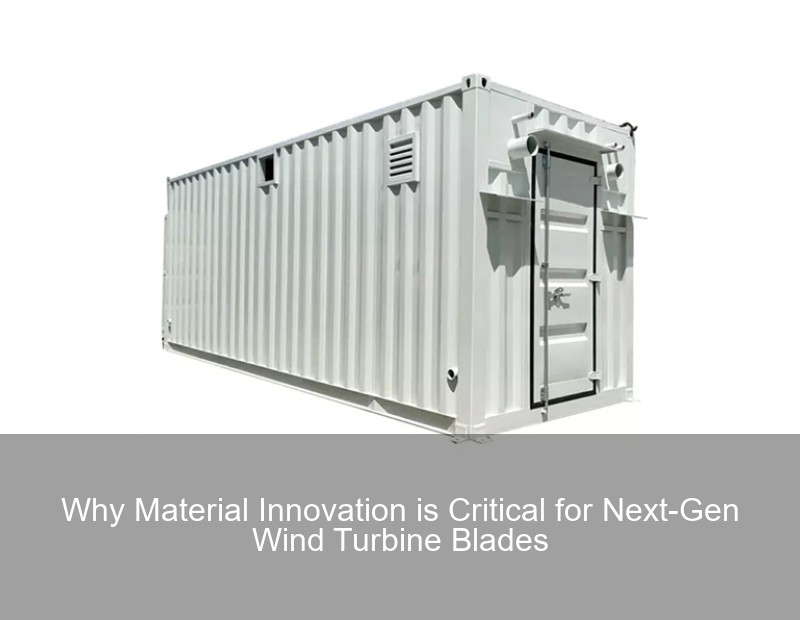
Meta Description: Discover how advanced materials like carbon fiber composites and bio-resins are solving durability challenges in large wind turbine blades, with 2024 industry data and case studies. Learn why material science holds the key to efficient renewable energy.
The Growing Demands on Wind Turbine Blade Materials
With wind turbines now exceeding 100-meter blade lengths , material engineers face unprecedented challenges. How do we balance structural integrity, weight reduction, and environmental sustainability? Let’s break down the evolving requirements:
Problem 1: Traditional Materials Hitting Physical Limits
Fiberglass-reinforced epoxy (GRE), the industry standard since the 1990s, struggles with:
- Crack propagation in offshore salt environments
- Limited fatigue resistance beyond 20-year lifespans
- Weight penalties causing 4-7% energy loss in turbines over 8MW
Material | Density (g/cm³) | Fatigue Life (cycles) | Cost per kg ($) |
---|---|---|---|
GRE | 1.9 | 1×10⁷ | 12-15 |
Carbon Fiber | 1.6 | 5×10⁷ | 45-60 |
Bamboo Composite | 1.1 | 3×10⁶ | 8-11 |
2024 Material Breakthroughs: What’s Working Now
You know, the real game-changer has been hybrid composites. Take Siemens Gamesa’s 115-meter blades – they’re using a carbon-glass fiber hybrid that reduces weight by 22% compared to pure GRE designs .
Solution 1: 3D-Printed Spar Caps
GE Renewable Energy’s new “spar cap” design printed from recycled PETG thermoplastic:
- 25% faster production time
- 12% better vibration damping
- Fully recyclable – no landfill waste
“We’ve moved from ‘just strong enough’ to ‘smart enough’ materials,” says Dr. Elena Marquez, lead materials engineer at Vestas. “Our self-healing epoxy resin can seal micro-cracks within 72 hours of formation.”
The Road Ahead: Materials Shaping Wind Energy’s Future
As we approach Q4 2025, three trends dominate R&D pipelines:
- Bio-based Epoxies: BASF’s lignin-derived resin cuts carbon footprint by 40%
- AI-Optimized Layups: Machine learning predicts stress patterns for precision fiber alignment
- Modular Blade Systems: Lego-like segments using shape-memory polymers
Case Study: Ørsted’s North Sea Turbines (2023-2024)
After switching to carbon/hemp hybrid blades:
- 17% fewer downtime incidents
- 9.3% annual energy output increase
- 28% lower maintenance costs
Well, the numbers don’t lie – material innovation isn’t just about science. It’s about making wind energy economically viable in markets with lower wind speeds. And that’s how we’ll hit those 2030 renewable targets.
References:
Contact Us
Submit a solar project enquiry,Our solar experts will guide you in your solar journey.