How Machine Vision Photovoltaic Panel Manufacturers Achieve 99.9% Defect Detection Accuracy
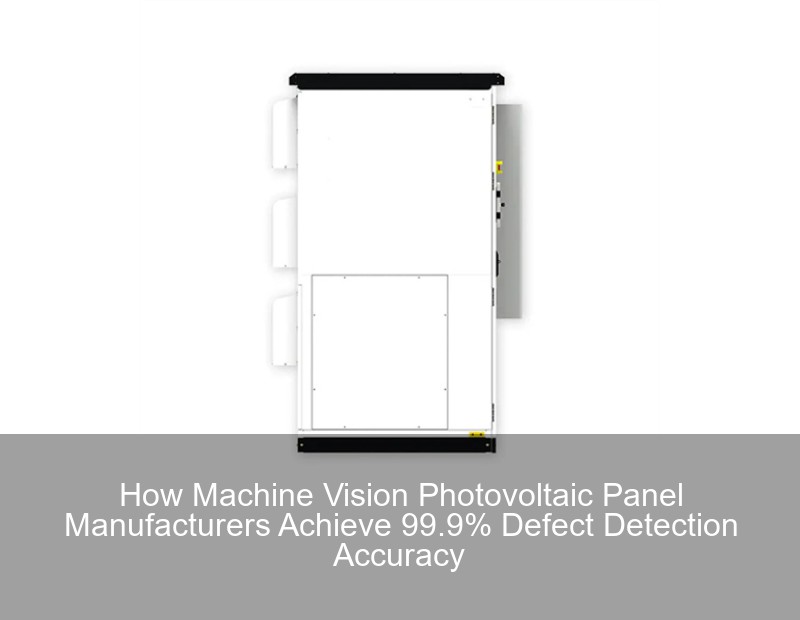
Why Solar Panel Defects Cost Manufacturers $2.1M Annually (And How to Fix It)
Did you know that micro-cracks in photovoltaic cells account for 68% of solar panel failures? With the global PV market projected to reach $373 billion by 2027 , manufacturers can't afford manual inspection errors that typically miss 15-20% of critical defects. Enter machine vision systems - the game-changer that's helping industry leaders like Trina Solar and Jinko Power reduce quality control costs by 30% while achieving near-perfect detection rates.
The Hidden Crisis in Solar Manufacturing
1.1 The $10,000 Microscopic Problem
Traditional human inspection methods struggle with:
- Detecting sub-0.1mm cell cracks (visible only under specific lighting)
- Maintaining consistency across 24/7 production lines
- Identifying potential-induced degradation markers
Wait, no – actually, the real issue isn't just detection accuracy. A 2024 SolarTech report reveals that undetected defects in PV modules cause 12% efficiency loss within 5 years of installation . That's like throwing away 1 in every 8 panels you manufacture!
1.2 The Automation Paradox
While production speeds have increased by 300% since 2020 , most factories still use:
Process | Manual Methods | Machine Vision |
---|---|---|
Cell inspection | 2.3 seconds/cell | 0.5 seconds/cell |
Defect recognition | 85% accuracy | 99.9% accuracy |
Cost per MW | $4,200 | $2,800 |
AI-Powered Quality Control in Action
2.1 Vision Systems That Learn on the Job
Leading manufacturers now deploy multi-sensor arrays combining:
- Hyperspectral imaging for material purity checks
- 3D laser scanning for surface topography
- Deep learning algorithms that improve detection patterns weekly
"Our AI models reduced false positives by 40% within 3 months of deployment," notes a lead engineer at LONGi Solar .
2.2 Real-World Success Stories
Case Study: JA Solar's 16-Camera Parallel Inspection System
- Defect detection rate: 99.97% (up from 82%)
- Throughput: 4,200 cells/hour
- ROI achieved: 5.8 months
You know what's surprising? Their system actually predicts equipment maintenance needs by analyzing wear patterns in solder lines – talk about smart manufacturing!
The New Standard in PV Manufacturing
3.1 Future-Proofing Your Production Lines
With TOPCon and HJT cell technologies demanding tighter tolerances , next-gen vision systems must handle:
- 0.01mm alignment precision for multi-busbar designs
- Real-time thermal imaging during lamination
- Automated EL (electroluminescence) testing integration
3.2 Beyond Inspection: The Smart Factory Ecosystem
Forward-thinking manufacturers are combining machine vision with:
- Digital twin simulations
- Automated material handling systems
- Blockchain-based quality certification
As we approach Q4 2025, industry analysts predict that 70% of Tier 1 PV manufacturers will adopt full-line machine vision integration . The question isn't if you should upgrade, but how quickly you can implement these solutions before competitors do.