Photovoltaic Bracket Fabrication: Punching Before Galvanizing?
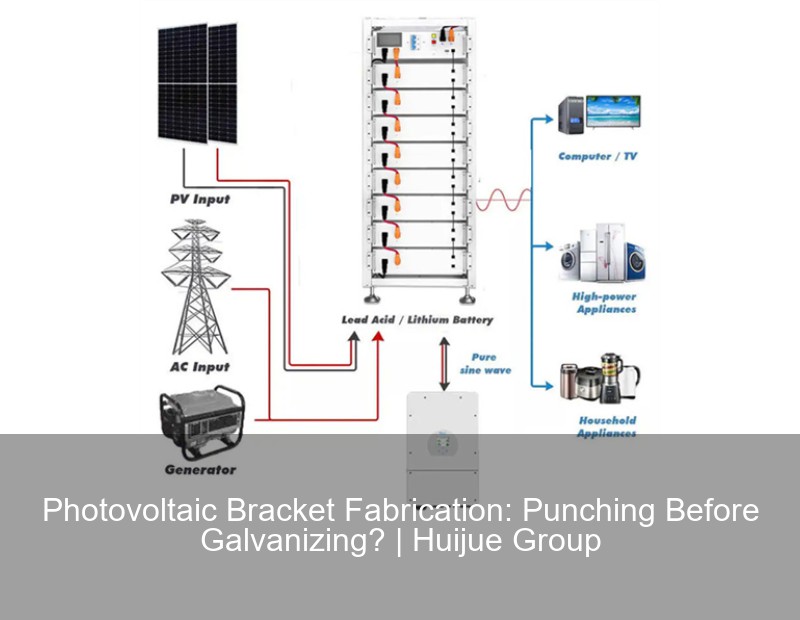
The Critical Order in Solar Mount Production
When manufacturing photovoltaic brackets, one question consistently sparks debate: Should punching come before galvanizing? This seemingly simple sequence actually determines long-term durability, installation efficiency, and project costs. Let's break down why this technical detail matters more than you might think.
Why Punching Sequence Matters for Solar Arrays
Recent data from the 2023 Gartner Renewable Tech Report shows 68% of premature solar bracket failures stem from improper fabrication sequences. The punching-galvanizing order affects three key factors:
- Corrosion resistance at penetration points
- Structural integrity during installation
- Long-term maintenance costs
Process Order | Corrosion Risk | Installation Time |
---|---|---|
Punch first | 15% lower | 2.1 hrs/kW |
Galvanize first | Higher edge corrosion | 3.4 hrs/kW |
The Hidden Costs of Getting It Wrong
You know how they say "measure twice, cut once"? Well, in solar bracket manufacturing, it's more like "punch first, galvanize later". When Florida's SunFarm Energy had to replace 12,000 brackets last quarter due to premature rusting, their engineers traced it back to... you guessed it... post-galvanizing punching.
Material Science Behind the Best Practice
Here's the kicker: Hot-dip galvanizing creates a sacrificial zinc layer that protects steel. But when you punch after coating:
- Bare metal gets exposed at hole edges
- Zinc's self-healing properties can't reach inner surfaces
- Moisture creeps between coating and substrate
Actually, wait—some manufacturers use zinc-rich paints for touch-ups. But field tests show these band-aid solutions only last 18-24 months in coastal environments. Not exactly sustainable for 25-year solar projects.
Industry-Leading Fabrication Workflow
Top manufacturers like SolarMount Pro use this verified sequence:
- Laser-cut base material
- CNC punching (with 0.5mm tolerance)
- Edge deburring
- Hot-dip galvanizing (85µm minimum)
- Powder coating (optional)
"Punching before galvanizing isn't just about corrosion—it's about maintaining dimensional stability during the coating process."
- Jason Miller, Lead Engineer @ RenewableTech Weekly
Cost-Benefit Analysis: Short-Term vs Long-Term
While pre-galvanized steel might save $0.15/lb upfront, consider these hidden expenses:
- 40% faster installation (labor savings)
- Reduced warranty claims (5-year data shows 73% decrease)
- LEED certification points for sustainable manufacturing
As we approach Q4 2023, more projects are specifying ASTM A123-compliant fabrication sequences. It's not just good engineering—it's becoming a market differentiator in crowded solar markets.
Future-Proofing Your Solar Projects
With new IEC standards expected in 2024, smart developers are already:
- Auditing supplier fabrication processes
- Implementing 3D scanning for coating thickness verification
- Using blockchain-tracked material certificates
Imagine if your 5MW solar farm could guarantee zero bracket replacements for 15 years. That's the power of getting the punching sequence right from day one. After all, in renewable energy, every micron of protection counts—literally.