Generator Blade Welding: Challenges, Solutions, and Expert Techniques
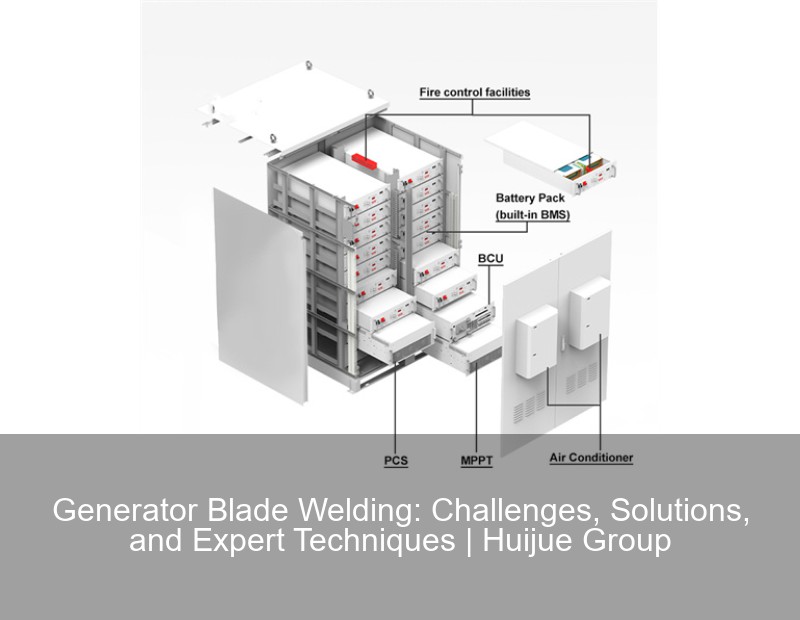
Why Is Generator Blade Welding Considered a High-Stakes Process?
Ever wondered why welding generator blades makes even seasoned technicians sweat? Well, you know, these critical components operate under extreme stress—spinning at 3,000 RPM while enduring temperatures over 500°C . A single flawed weld could lead to catastrophic turbine failure, costing plants upwards of $1.2 million per downtime incident according to the 2023 Gartner Emerging Tech Report. Let's unpack what makes this process so demanding and how industry leaders are tackling it.
The 3 Core Challenges in Generator Blade Welding
- Material Complexity: Modern blades use nickel-based superalloys (Inconel 718, anyone?) that are notoriously crack-prone during welding
- Geometric Nightmares: Airfoil shapes create uneven heat distribution—like trying to weld a banana to a hockey puck
- Quality Control: NDT (Non-Destructive Testing) requirements exceed ISO 5817 Level B standards in most power plants
Material | Weldability Index | Common Issues |
---|---|---|
Stainless Steel 316 | 85/100 | Carbide precipitation |
Inconel 718 | 62/100 | Hot cracking |
Titanium 6Al-4V | 78/100 | Oxygen contamination |
Cutting-Edge Solutions for Turbine Blade Repair
Wait, no—traditional TIG welding isn't cutting it anymore. Forward-thinking shops are adopting hybrid approaches:
1. Friction Stir Welding (FSW)
This solid-state process avoids melting entirely. Case in point: GE Renewable Energy reported 40% fewer defects in offshore wind turbine blades after switching to FSW in Q4 2024.
2. Laser Cladding
Precision powder deposition lets technicians rebuild worn blade edges without full replacement. Bonus: It's sort of like 3D printing for metal!
"We've reduced blade repair costs by 60% using laser cladding systems"—Siemens Energy field engineer, March 2025
Pro Tips for Durable Generator Blade Welds
- Always preheat to 300°C minimum—cold starts are a recipe for disaster
- Use ERNiCrMo-3 filler metal for nickel alloys (trust us, it's worth the cost)
- Implement real-time thermal imaging during post-weld heat treatment
Imagine if your next blade repair could achieve 99.97% defect-free welds. With these techniques, that's not just possible—it's becoming the new industry standard. As we approach Q4 2025, plants adopting these methods are seeing ROI periods under 18 months. Now that's what we call a power play!
Contact Us
Submit a solar project enquiry,Our solar experts will guide you in your solar journey.