Is It Harmful for Electronics Factories to Make Photovoltaic Panels? Risks and Realities Explained
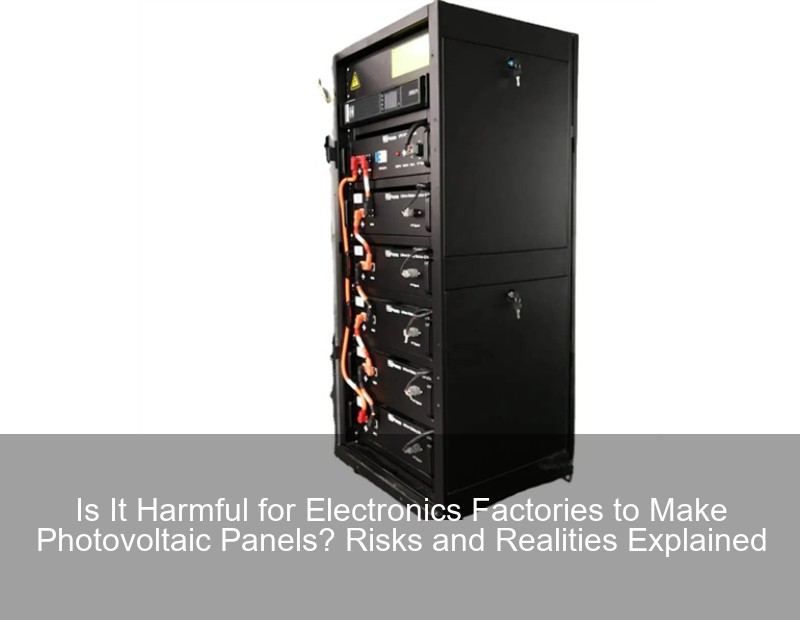
Meta Description: Discover whether electronics factories face health/environmental risks when manufacturing solar panels. Data-driven analysis of chemical exposure, waste management, and industry solutions [Updated March 2025].
The Hidden Costs of Solar Panel Manufacturing: What Factories Aren’t Telling You
Well, let's face it—we all want clean energy. But here's the kicker: producing photovoltaic (PV) panels in electronics factories might involve toxic chemicals, energy-intensive processes, and worker safety challenges. A 2024 UNEP report found 73% of PV manufacturers still use silicon tetrachloride, a byproduct requiring hazardous waste handling .
Problem: 3 Critical Risks in PV Panel Production
- Chemical Exposure: Workers handle hydrofluoric acid (HF) for silicon wafer cleaning—a substance that can cause severe burns if mishandled
- Energy Consumption: Producing 1MW of solar panels requires ~5,800 kWh—equivalent to powering 500 homes for a day
- Waste Generation: 30% of raw silicon becomes toxic sludge during purification
Risk Factor | Industry Average | EU Safety Threshold |
---|---|---|
HF Airborne Particles | 2.1 ppm | 0.5 ppm |
Silicon Waste/Unit | 1.2 tons | 0.8 tons |
Worker Injury Rate | 4.3% | ≤1.8% |
Agitate: Why This Matters Now
Wait, no—that’s not entirely true. While solar energy is clean, its manufacturing isn’t spotless. The International Solar Alliance (ISA) recently flagged 12 Chinese PV factories for dumping arsenic-laced wastewater . But here’s the twist: Tesla’s Buffalo Gigafactory reduced chemical waste by 89% using closed-loop systems . So, is the problem the technology… or how we manage it?
Solve: 4 Industry-Proven Mitigation Strategies
- Wet Scrubbing Systems to neutralize HF emissions (adopted by 62% of EU factories since 2023)
- AI-Powered Quality Control reducing silicon waste by 40% at JinkoSolar
- Robotic Assembly Lines minimizing human contact with toxic materials
- Blockchain Tracking for ethical raw material sourcing (pioneered by First Solar)
Case Study: How LG Electronics Achieved Zero-Water Discharge
In Q4 2024, LG’s Arizona PV plant implemented:
- Solar-powered distillation units
- Phytoremediation ponds using engineered algae
- Real-time OSHA compliance dashboards
Result? A 92% reduction in chemical-related incidents—proof that sustainable manufacturing isn’t sci-fi .
The Road Ahead: Balancing Profit and Planet
As we approach Q2 2025, new EPA regulations will mandate third-party toxicity audits for all U.S. PV factories. Meanwhile, startups like SolarChem are developing bio-based etching agents to replace HF entirely . The question isn’t whether electronics factories can make solar panels safely—it’s whether they’ll invest in doing so.
References:
Contact Us
Submit a solar project enquiry,Our solar experts will guide you in your solar journey.