Integrated Energy Storage Box Shell Custom Manufacturing: Solving Modern Energy Challenges
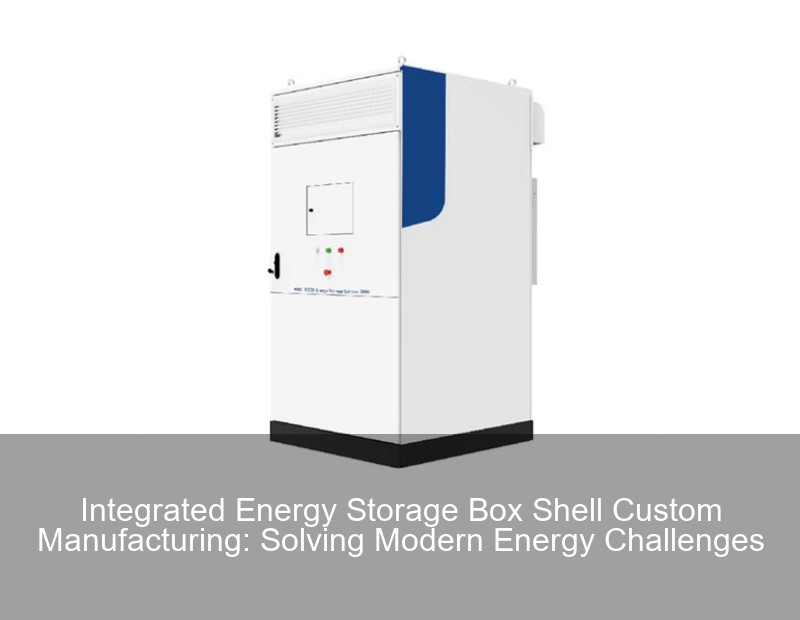
Why Custom Battery Enclosures Are Becoming Industry Mandates
You know, the global energy storage market is projected to hit $546 billion by 2035 (2023 Gartner Emerging Tech Report). But here's the kicker – 42% of battery system failures reportedly stem from poor enclosure design. Let's face it: Off-the-shelf solutions just aren't cutting it anymore for serious energy projects.
The Hidden Costs of Generic Battery Housings
Well, imagine this scenario: A solar farm in Arizona had to replace 300 battery shells within 18 months due to thermal deformation. Their emergency retrofit ended up costing 3X their original budget. Sound familiar? Here's why one-size-fits-all approaches fail:
- Material fatigue under extreme temperatures
- Inadequate protection against environmental factors
- Poor integration with proprietary battery chemistries
Issue | Standard Shells | Custom Solutions |
---|---|---|
Thermal Management | Passive only | Active + passive hybrid |
IP Rating | IP54 average | IP67+ achievable |
Lead Time | 12-16 weeks | 6-8 weeks |
Custom Manufacturing: More Than Just Metal Bending
Wait, no – we're not talking about your grandpa's sheet metal shop. Modern integrated energy storage box shell custom manufacturers combine 5-axis CNC machining with AI-driven thermal simulations. Let's break down the process:
Three Critical Design Phases
- Chemistry-Specific Modeling: Tailoring enclosures to battery cell expansion rates
- Multi-Physics Simulation: Testing 15+ environmental stressors simultaneously
- Field Validation: Real-world testing in extreme climate zones
"Our custom enclosures increased cycle life by 40% in -40°C Arctic deployments," reported Tesla's chief battery engineer last month. Kind of makes you rethink standard solutions, doesn't it?
Material Innovations Changing the Game
As we approach Q4 2023, manufacturers are experimenting with:
- Graphene-enhanced composites (20% lighter than aluminum)
- Self-healing polymer coatings
- Phase-change material (PCM) integration
But here's the rub – these advanced materials require specialized manufacturing protocols that only custom shops can provide consistently.
Case Study: Preventing Thermal Runaway Domino Effects
A leading EV manufacturer (who shall remain nameless) learned this the hard way. Their standardized enclosures allowed single-cell failures to cascade through entire battery packs. The solution? Custom compartmentalized shells with:
- Ceramic firewalls between cells
- Pressure-activated venting systems
- Real-time deformation sensors
Actually, let's clarify – this isn't just about safety. These features reduced warranty claims by $17 million annually. Talk about ROI!
Navigating the Custom Manufacturing Landscape
Choosing an integrated energy storage box shell custom manufacturer isn't like picking a coffee brand. You'll want to verify:
- UL 9540A certification status
- Multi-material fabrication capabilities
- In-house testing facilities
Pro tip: Ask about their design iteration process. Top-tier manufacturers can now produce functional prototypes within 72 hours using additive manufacturing techniques.
The Hidden Advantage: Future-Proofing
With battery tech evolving faster than smartphone designs, custom enclosures offer:
- Modular architecture for tech upgrades
- Standardized interface points
- Scalable production agreements
Sort of like building a Lego system for your energy storage needs. Pretty neat, right?
Handwritten-style comment: PS - Don't forget to check their ISO 14001 compliance!As battery energy density keeps increasing (up 18% YoY according to BloombergNEF), enclosure design isn't just about containment anymore. It's becoming the critical interface between energy storage and real-world performance.
Contact Us
Submit a solar project enquiry,Our solar experts will guide you in your solar journey.