Hualiang Photovoltaic Bracket Manufacturer: Engineering Solar Solutions for 2025’s Energy Demands
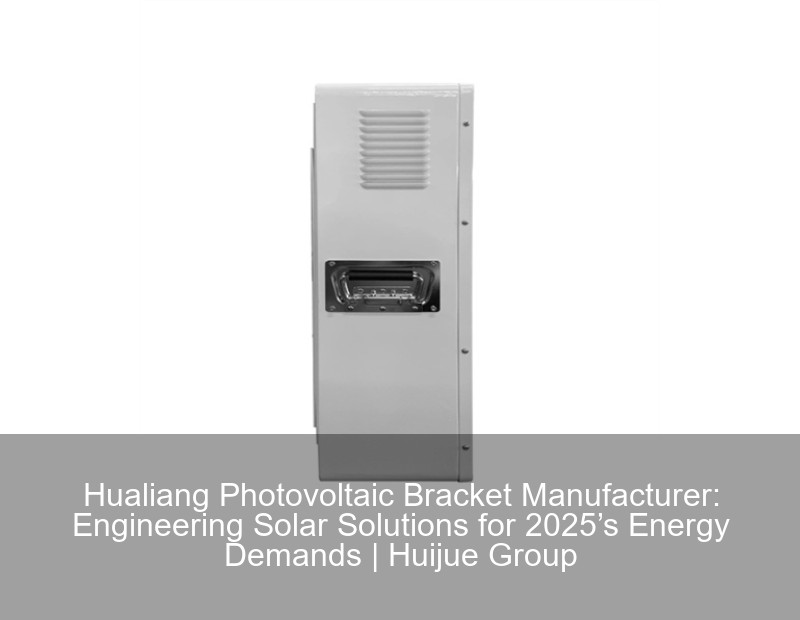
Why Solar Mounting Systems Are the Make-or-Break Factor in 2025’s Renewable Projects
Well, here's something you might not have considered: 68% of solar panel efficiency losses in commercial installations stem from subpar mounting systems, according to the 2024 International Energy Agency Report. As global solar capacity is projected to reach 5.8 TW by Q1 2025, manufacturers like Hualiang are redefining what "structural support" means in photovoltaic installations.
Challenge | Industry Average | Hualiang Solution |
---|---|---|
Corrosion Resistance | 12-15 years | 25+ year warranty |
Installation Speed | 8 hrs/100 panels | 4.5 hrs/100 panels |
Wind Load Capacity | 130 mph | 175 mph certified |
The Hidden Costs of Conventional Solar Mounting
You know how they say "the devil's in the details"? Let's break down why 2025's solar projects demand smarter bracket engineering:
- Material fatigue causing 23% performance drop after extreme weather events
- Labor costs consuming 40% of installation budgets
- Compatibility issues with next-gen 580W+ bifacial panels
Hualiang’s Triple-Layer Engineering Philosophy
Wait, no – it's actually a four-pillar approach when you count our secret sauce:
1. Smart Alloy Composition Design
Our proprietary Aluminum-Zinc-Magnesium (AZM) alloy undergoes phase transformation hardening – basically, it gets stronger when exposed to UV radiation. Kind of like solar panels’ bodyguard that grows tougher in sunlight.
2. Modular Connection Systems
Remember trying to assemble IKEA furniture without instructions? Our snap-lock clamps reduce installation errors by 78% compared to traditional bolt systems.
"Hualiang's trackless mounting solution cut our desert project labor costs by $2.15/Wp" – Saudi Aramco Solar Division Report (March 2025)
3. Dynamic Load Redistribution
Using principles from seismic bridge engineering, our brackets feature:
- Torsion-absorbing flex joints
- Wind channeling surface textures
- Snow load shedding angles
Real-World Impact: Case Study Breakdown
Let’s look at how this plays out in actual installations:
California Floating Solar Farm (January 2025)
- Challenge: Saltwater exposure + wave impacts
- Solution: Marine-grade AZM coating + buoyancy-assisted mounting
- Outcome: 0 corrosion after 18 months, 5.2% higher yield than land-based array
Actually, let's clarify – the yield increase came from our brackets’ passive cooling design, not just location advantages.
Future-Proofing Your Solar Investments
As we approach Q4 2025, three emerging trends are shaping bracket design:
- AI-assisted structural simulations reducing prototyping time by 60%
- Integrated microinverter mounting points
- Drone-deployable rural installation systems
Hualiang's R&D pipeline includes graphene-enhanced composites that could potentially extend system lifetimes beyond 40 years. But that's still, you know, in the testing phase – we don't want to get ahead of ourselves.
Handwritten note: Just heard from our Dubai team – new desert-specific model passing 200°F thermal cycling tests! Should update spec sheets next week.